1. はじめに
スマートフォンやウェアラブル端末などの電子機器では、さらなる小型化・高性能化が求められています。またIoT(Internet of Things)の普及により、自動車や家電などあらゆるものに通信モジュールやセンサーが組み込まれる時代が到来し、SiP(System in Package)/モジュール部品に対する需要は増加しています。SiP/モジュール部品の製造プロセスで共通していることは、高密度化、薄型化、多層化などの最先端の実装技術が織り交ざっているということです。
FUJIは、こうしたSiP/モジュール部品製造に対する様々なソリューションを展開しています。今回、各機能・ユニットの中で、高密度化と薄型化に対するソリューションをご紹介します。(図1)
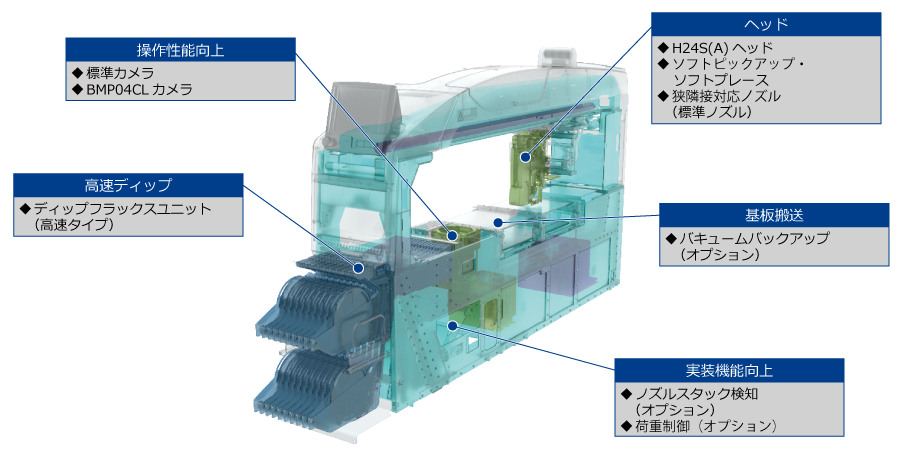
図1 SiP/モジュール部品の製造向けソリューション
2. 高密度化への取り組み
高密度化が進むことによる課題と対策をご紹介します。
2-1. 装着する部品点数の増加
電子機器の高性能化を実現するために、SiPに装着される部品の点数は増加傾向にあります。RFモジュールに装着される部品点数が2年で約1.2倍に増加した例もあります。SiP 1個あたりに装着する部品の点数の増加により、生産に時間がかかるため、SiP自体の生産数が減ってしまいます。生産数を上げるために、実装機のスループット向上が要求されます。
NXT III + H24S(A)ヘッドで42,000cph(chip per hour) (生産優先モード)の高スループットを実現します。基板デザインに合わせて、生産性を重視した生産優先モード、標準モード、高精度な装着を重視した高精度モードの3つのモードを使い分けることができます。
また、SiPに装着される部品は受動部品だけでなく、バンプサイズの小さいWLPの装着数も増加しています。通常、受動部品は、はんだペーストを印刷し、部品を装着、最後にリフローではんだペーストを硬化させて基板と部品を接合させています。しかし、WLPのバンプ部分に受動部品と同じようにはんだペーストを印刷する場合、メタルマスクの開口サイズが小さくなるため、印刷は困難です。このため、WLPにはバンプへはんだペーストもしくはフラックスの転写が必要となります。転写工程にも、吸着と装着の工程同様にスループットの向上が求められます。
そこで、高速化が難しいといわれる転写工程において、高速ロータリーヘッドの転写対応を行い、高速化を実現しました。H24S(A)ヘッドの高速転写のスループットは、最大で18,500cphとなり、大幅に生産性が向上します。(図2)
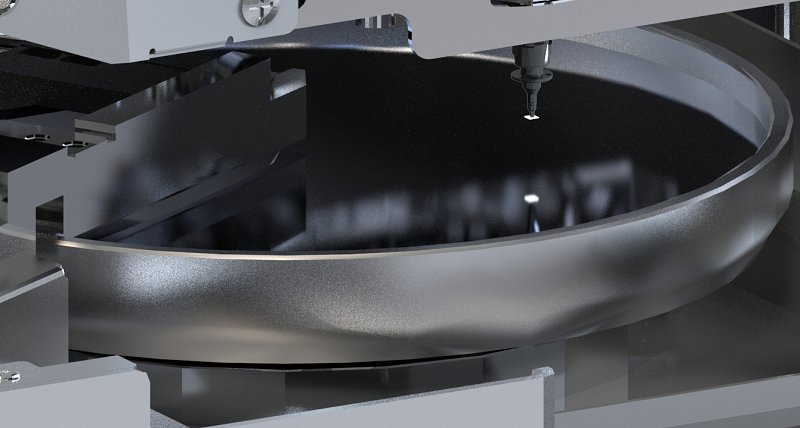
図2 H24S(A)ヘッドによる高速転写
2-2. 部品間の狭小化
前項でふれた通り、SiPに装着される部品の点数が増加していますが、増加した分の実装エリアを大きくしてしまうとSiP自体も大きくなり、さらには電子機器も大きくなってしまいます。例えば、スマートフォンでは使用されるバッテリサイズを大きくするために、実装基板の小型化への要求もあります。それらを解決するために、部品間の隙間を狭くして実装エリアを小さくする傾向にあり、狭隣接に対する実装性能の向上も求められます。
2つの対策について、ご紹介します。
部品間の隙間が狭い基板に部品を装着する場合、吸着ノズルの先端が部品よりもはみ出すと、装着済みの隣接部品にノズル先端が干渉し、実装不良が発生する場合があります。隣接部品との干渉を防ぐためには、部品吸着時にノズル先端が部品からはみ出す量が小さいことが必要になります。なお、SiP向けの部品間の隙間の動向としては、100μm以下が多くあり、中には65μmというかなり狭いケースもあります。今後、部品間の隙間はさらに狭くなることを予想しています。(図3)
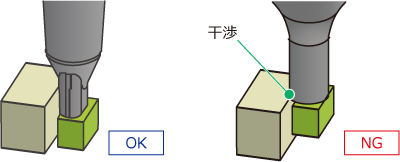
図3 隣接部品の実装
狭隣接実装を可能にするために、標準ノズルにて狭隣接の対応をすることで、ノズル先端のはみ出し量を抑えることができます。(図4)
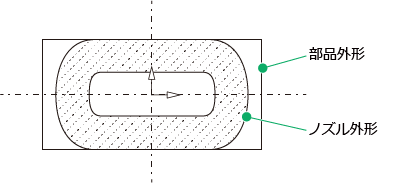
図4 狭隣接対応のノズル形状
SiPでは、部品間の隙間を狭くするために、フィレットレスでの部品接合が多くなっています。マザーボードのように小型の受動部品からICやコネクタなどの大型部品の混載がないことが理由です。また、SiPは最後に部品装着面を樹脂で封止するため、はんだ接合に部品と基板の接合部の強度を求めないケースもあります。これらにより、使用されるはんだペーストの量が少なくなる傾向にあります。はんだペーストの量が少なくなることで、部品をはんだ上に保持するタッキング力が低くなりますが、低タッキングの条件下に対しても安定した装着が必要になります。(図5)
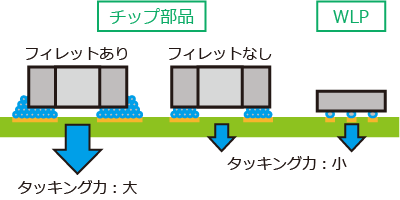
図5 部品と基板間のタッキング力
NXT III + H24Aヘッドによる部品装着時の最適なエアーコントロールによって、低タッキングの条件下においても安定した装着を実現します。H24Aヘッドではエアーコントロールのタイミングが部品毎に設定ができるようになりました。タイミングを変更することで、状況に応じた最適な部品の装着を行うことができます。例えば、下降端で真空破壊を完了した後、ノズル上昇の設定を行うことで、真空破壊時のエアーが原因の不良発生を防ぐことができます。(図6)
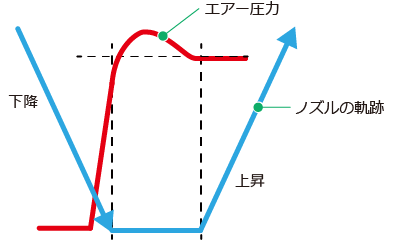
図6 ノズル先端とエアー圧力
2-3. WLPのバンプサイズの微小化
前項でふれた通り、実装エリアを小さくするために部品は狭隣接になり、装着される部品のサイズも小さくなります。SiPで使用される受動部品は0603サイズから0402サイズ、さらには0201(0.25mm×0.125mm)サイズと小さくなっています。混載されるWLPも同様に小型化が要求されます。加えて、こうしたSiPでは、WLPの高性能化のために多ピン化が進み、バンプサイズが微小化しています。極小の受動部品や微小バンプのWLPを装着するためには、スループットだけでなく高品質に装着する能力も必要です。WLPの装着能力で重要になるのが、微小バンプの認識と基板に装着する技術です。
SiP向けに使用されるWLPのバンプサイズの動向として、φ70~φ100μmサイズが増加しています。さらに、一部のメーカーではφ70μm以下のサイズのWLPが使用されつつあります。これらの微小バンプを認識するためには、より高い分解能の画像処理技術が必要です。微小バンプのWLPの装着を可能にするために、FUJI独自のサーボ技術と画像処理アルゴリズムにて微小バンプを認識しています。
さらに、WLPのバンプを認識するうえで、バンプ面にある回路パターンがバンプの認識に悪影響を及ぼしています。BMP04CLカメラでは、標準カメラの機能に加え、ライティングの点灯パターンを細分化し、光源色も追加することでバンプのみを認識します。これにより、バンプ認識時の回路パターンの写り込みを防止します。(図7)
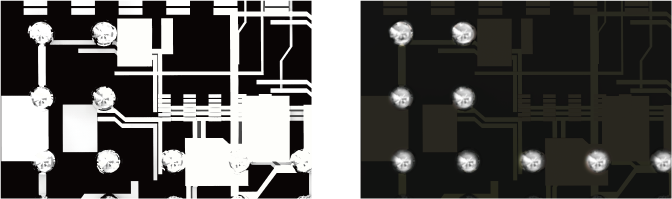
図7 ライティングパターン切り替えによる効果
WLPのバンプを画像認識した後はWLPを基板に装着しますが、バンプが微小になれば基板上のランドも小さくなります。微細なランド上にWLPのバンプを装着するためには、実装機の高精度化が求められます。
装着精度は、NXT III + H24S(A)ヘッドで15μm(高精度モード)とNXT-Hで8μmの高精度化を実現します。NXT IIIではサーボパラメータの最適化を行い、スループットの低下を最小限にとどめています。また、NXT-Hは高剛性構造設計をベースにして、リニアモータ駆動、高性能カメラを装備して、高精度化を行っています。
3. 薄型化への取り組み
SiPの薄型化は、今後さらに進んでいくと考えられます。課題と対策を紹介します。
3-1. 部品の薄型化
高性能化の要求に対応するため、部品の素材も変化しています。素材によっては部品の厚みが薄い場合、装着時の衝撃荷重が大きいと破損する可能性があります。部品へダメージを与えないように、装着時の衝撃荷重を低減しなければいけません。
FUJIのノズルは先端の可動部の小型化・軽量化と2ピース構造により、部品装着時の衝撃荷重を抑えています。H24S(A)ヘッドのような高速ヘッドで使用するノズルでは、装着スピードを低下させることなく0.5Nの低荷重による部品装着を実現します。(図8)
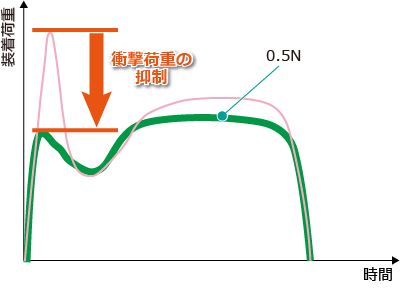
図8 装着荷重のイメージ
また、SiPでは低荷重での装着だけでなく、適正な荷重での装着も求められます。
この対策は、ロードセルを使用した荷重制御にて実現します。装着荷重は押込み量を変更することで制御しており、押込み量を増やすと装着荷重は大きく、押込み量を減らすと装着荷重は小さくなります。(図9)
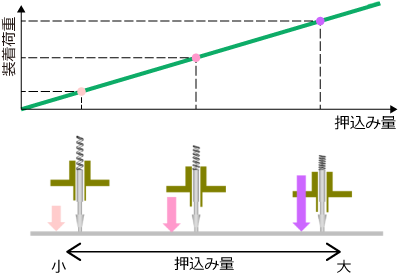
図9 荷重制御
装着荷重は押込み量を変更することで、ばねのたわみ量を制御していますが、ばねにはばらつきが存在しており、このばらつきによって荷重誤差が発生します。適正な装着荷重にするために、ロードセルを使用してばね特性の誤差分を補正し、装着荷重の精度を上げます。(図10、11)
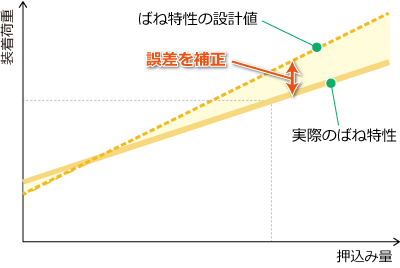
図10 ロードセルを使用した荷重制御
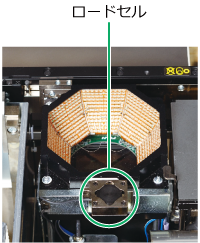
図11 ロードセル
ノズルの定期メンテナンスにより品質は保たれますが、生産中にノズルのスタックなど異常が発生した場合、装着時に部品へダメージを与えるため、ノズルがスタックしていないか確認したいという要求があります。
これに対し、ロードセルを使用してノズルスタックを検知し、部品への過大な荷重を防ぎます。 (図12)
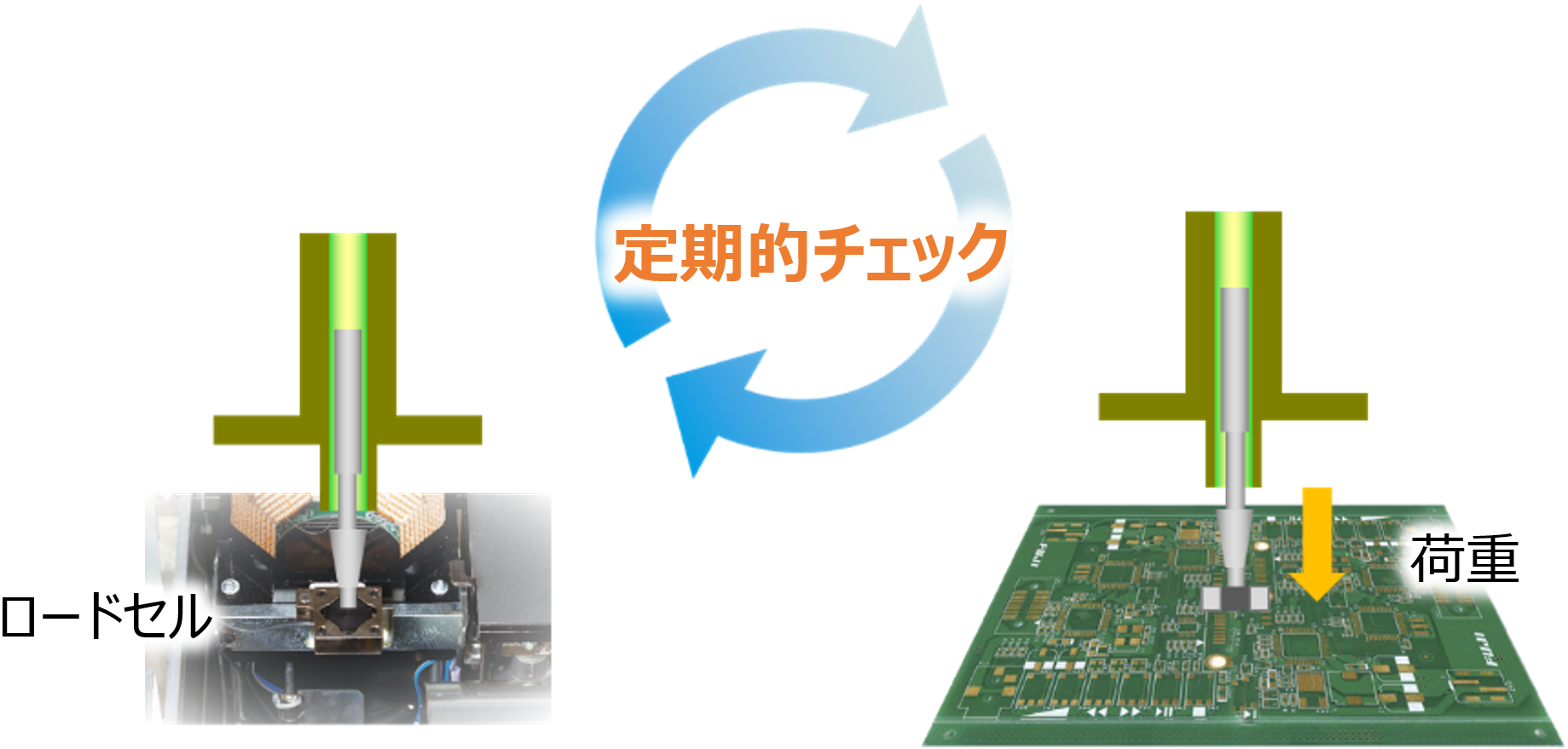
図12 ノズルのスタック検知
また、部品を装着する際、基板接触時の衝撃荷重を可能な限り低減するための低速ノズル下降や、部品装着後に持ち帰り防止のための低速ノズル上昇などの要求もあります。この場合でも生産効率はできるだけ落とさないことが重要です。
そのために、部品毎に最適な動作が可能なソフトプレース機能があります。H24ヘッドなどの高速ヘッドでも使用でき、下降動作のみ、または上昇動作のみの適用やZ軸の移動速度と速度変更高さも個別に設定することができ、必要な動作が当該部品のみに適用され、スループット低下も最小限で実現できます。
3-2. 基板の薄型化
基板が薄くなる中で、実装品質を安定させるためには薄厚基板のたわみを矯正し、部品装着面を一定の高さで保持しなければなりません。
薄厚基板の保持にはバキュームバックアップが有効です。バキュームバックアップは、薄厚基板をバキュームプレート上面で吸着固定し、部品の装着面を一定の高さで保持、また、部品装着時の荷重による基板振動や基板反りの影響を最小限にします。(図13、14)
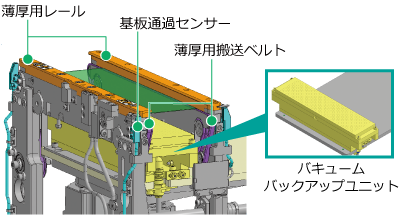
図13 薄厚基板の搬送・クランプ方法
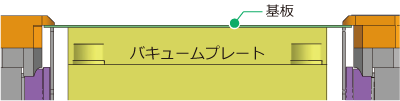
図14 薄厚基板のバキュームクランプ時の状態
4. おわりに
SiP/モジュール部品に対するソリューションをご紹介しました。今後、装着する部品点数の増加、部品間隙間の狭隣接化、WLPのバンプサイズの微小化、部品や基板の薄型化は、より一層進んでいきます。これらの最先端の実装技術を先取りした開発を行い、SiP/モジュール部品製造に対して積極的に取り組んでいきます。