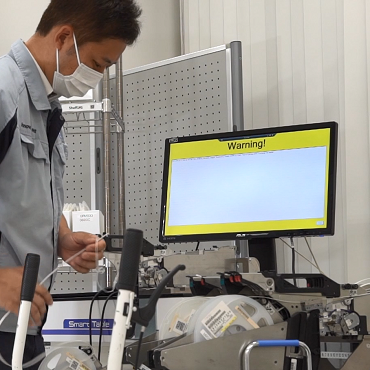
Learn fast, act quickly – Factory improvement solution, IPQC Expert
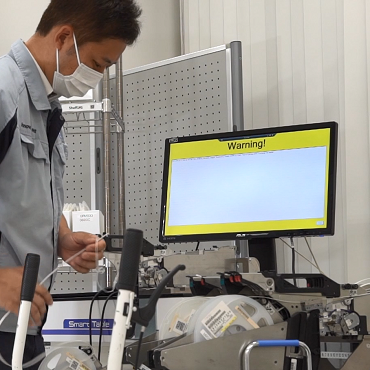
As globalization of supply chains is intensifying competition among companies, productivity has never been more important. Many companies therefore are working hard on improving productivity by leveraging digital technologies.
Meanwhile, in a customer survey we conducted we have found that more than 80 percent of our customers are facing productivity-related issues and have not seen visible improvements in productivity from their current efforts.
Here we introduce one of our productivity improvement solutions, IPQC Expert, which collects data from pick and place machine (chip mounter) production data, analyzes change points, and issues optimum guidance to respond to events that occurred.
In manufacturing in general, machine operators mainly perform relatively simple work such as attaching and removing parts to and from machines and putting away parts not to be used. When it comes to SMT lines, which consist of multiple types of machines, operators must learn to operate different types of machines and changeover work. In terms of changeover work, multiple types of materials are used to produce one product, requiring replenishment and exchange work for all of the materials. Besides this work, SMT lines involve many tasks that require operators to make their own decisions, such as checking panels that failed inspections by inspection machines and handling short stops, requiring operators to have a very high level of skills. Outside the line side, the minimum required quantity of parts must be prepared, distributed, and collected in a timely manner based on the progress status to prevent stagnation of materials on production floors.
Since the timing of performing such tasks is not set, which makes material management even more difficult, materials are managed by creating schedules for the SMT process alone separately from the overall product schedule.
Production environments such as SMT lines, where an operator needs to perform multiple tasks with a high level of skill, highly depend on individuals, resulting in variance of work time and quality.
Therefore, it is not easy to manage production so that it runs on schedule. To tackle such conditions, more and more companies are introducing monitoring tools to visualize production status in order to detect irregularities, such as progress delays and line stops, at an early stage and take the appropriate measures. However, while monitoring tools make it possible to check the statuses from the status of the entire floor to detailed production results such as nozzles and parts for each machine, they are not suited toward analyzing statuses from short-term trends when errors occur. Managers cannot always keep checking the monitoring tools because they are often away from their seats for meetings or other reasons. Therefore, it is difficult to provide prompt instructions for all error information.
Issues in the SMT process
· Management is difficult due to high dependance on human labor.
· It is difficult to analyze short-term trends when errors occur.
· Information from the monitoring tool cannot be effectively used.
IPQC Expert is a factory improvement solution that covers such issues in the SMT process.
Features of IPQC Expert
1. Captures irregularities occurring in production lines as trends
2. Allows anyone to take appropriate action immediately
3. Easy to introduce
Ideally, the part pickup rate should be maintained at 99.95% or higher during the part placement process.
However, in actual production, even if the pickup rate drops below 99.94% (three errors occur during 5,000 pickup operations), it is likely that most companies continue production and see what happens. What is important is to pay attention to when and how often pickup errors occurred. By focusing on this, we may notice serious causes that cannot be detected by monitoring tools.
For example, if these three errors occurred during the last 30 pickup operations, the pickup rate during this period would be 90.0%, indicating a very serious condition. However, because monitoring tools use the cumulative pickup count as a denominator, it is difficult to grasp such short-term worsening trends, which may lead to missing serious conditions.
Even in such a case, IPQC Expert can check the pickup rate in short-term periods, such as 30 pickup operations, to detect a rapidly deteriorating pickup rate trend and alert operators for further action at an early stage.
When multiple errors, long waits for the previous or next stage, or other problems occur during production, operators must take action to return production to normal. While experienced operators can take appropriate action immediately, new operators may not know what to do and may take a long time before taking action, causing the line to stop. IPQC Expert eliminates these differences from person to person, helping any operators to handle problems appropriately.
IPQC Expert can also be used to register appropriate actions taken by experienced operators as knowledge. If a problem occurs on production lines, IPQC Expert provides guidance on the appropriate action along with a warning. IPQC Expert can also designate terminals to display warnings and operational guidance, directing them to operators who can reliably handle the condition and prevent it from worsening.
IPQC Expert is an information-based solution for pick and place machines (chip mounters). Therefore, data linkage with other machines including inspection machines is not required, enabling easy introduction.
Even for users who find it difficult to obtaining the knowledge of experienced operators in a short period of time, the default registered data is available for use immediately after setup. You can use the default data to start improvement activities for the time being and gradually customize the work guidance so that it is optimal to your company's needs.
We introduced only a portion of the events for which IPQC Expert is useful.
Other examples include:
· Waiting periods for the previous/next stage
· Error occurrences at certain units
· Cycle time imbalance
· Vision processing error occurrences
IPQC Expert captures serious conditions that are difficult to be detected by monitoring tools and supports to maintain and improve productivity by preventing error stops and delays in response. It is easy to install and ready to use immediately after installation.
For more details, please feel free to contact us using the contact form. Casual inquiries welcome.
Applicable machines: NXT III, NXT IIIc, AIMEX III, AIMEX IIIc, NXTR S model