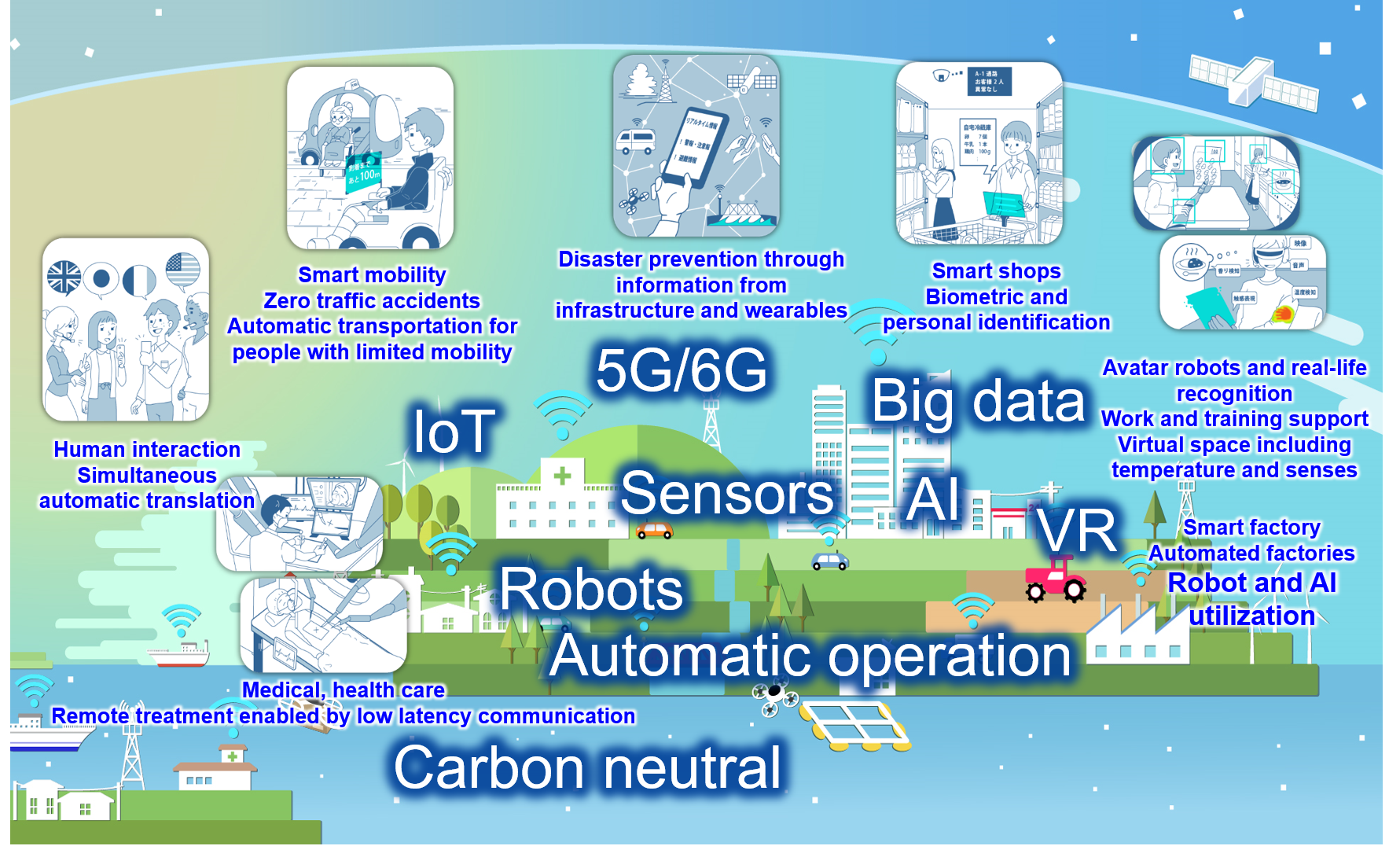
Placement Technology Trends for 2021 and Latest SMT Solutions
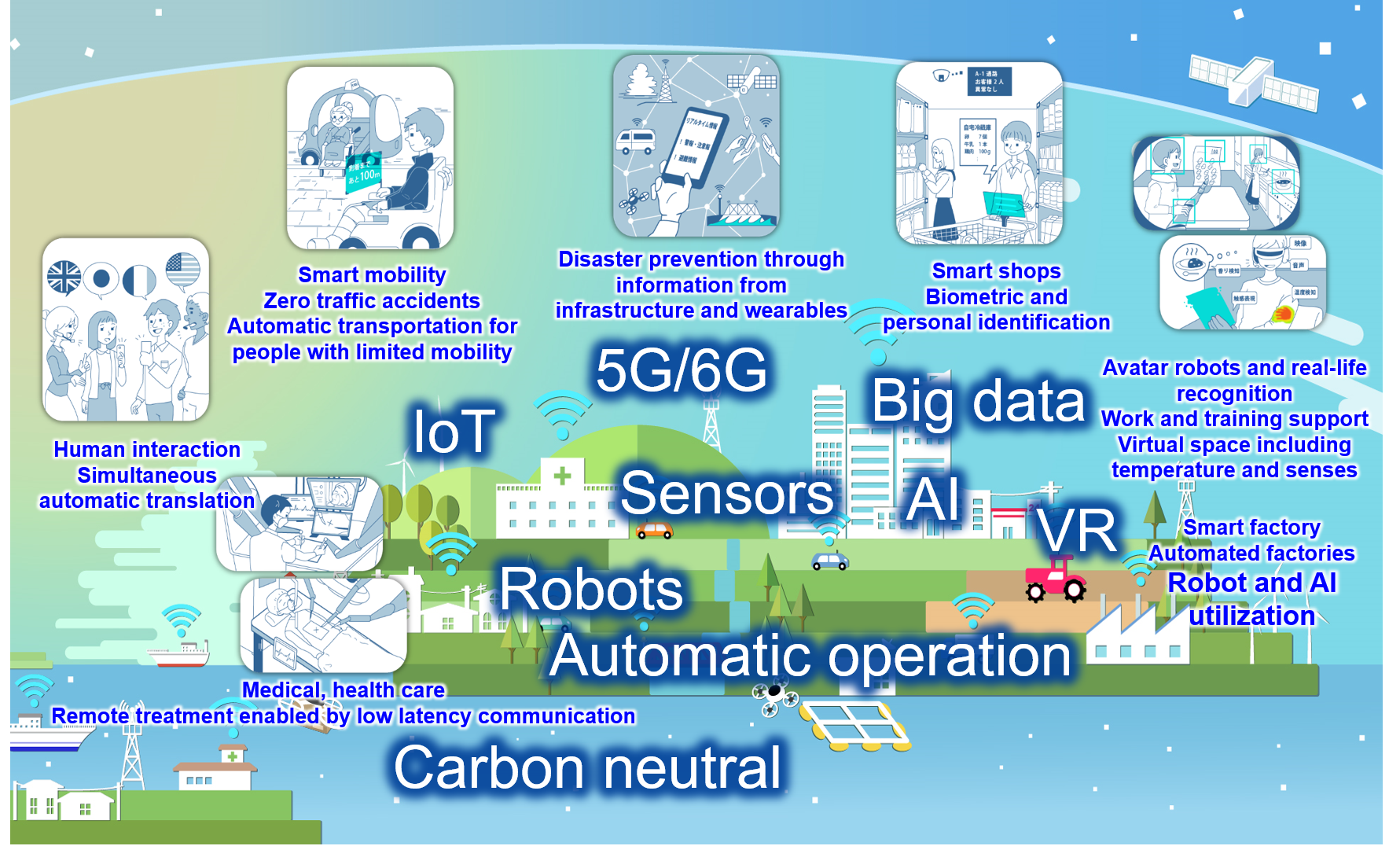
The worldwide spread of the COVID-19 has had a major impact on political, economic, and social activities, and has forced a rapid transformation of lifestyles. The COVID-19 era is changing workstyles with the rapid spread of teleworking from home and online meetings. In the past, robots were expected to improve the efficiency of business operations and to compensate for the shortage of workers due to the declining birthrate and aging population, but they are now finding new value in various industrial fields as service robots to realize "remote," "non-contact," and "non-face-to-face" operation that reduces the risk of infection. In addition, in order to curb the spread of infections and raise alarms, you may have heard about human contact data based on location information of communication terminals in the news. There is an awareness of the importance of how to go about utilizing the data already present in the field in both software and hardware applications.
We would like to demonstrate our vision of a future society which is an age of linking people, things, data, and processes (figure 1). In the "age of linking people, things, data, and processes", information that can be difficult to grasp, such as information related to behavior, including food, clothing, housing, health, purchasing, and transportation, and information related to the environment, such as climate and traffic, and information related to the business and operations of companies, will be digitized and centrally managed by connecting to a network, thus creating new value. While what we do here at Fuji is only a drop in the ocean compared to what is happening across society as a whole, we are keeping ahead of the curve. In this article we will cover the placement technology trends for 2021 and then introduce our efforts for digital twin solutions.
Figure 1: Future society an age of linking people, things, data, and processes
The number of placements on boards continues to increase due to the increasing number of multifunctional and high-performance communication devices such as smartphones and smartwatches, the expansion of network infrastructure and sensor devices with the spread of 5G and IoE, and the spread of electric vehicles. This section shows the size trend for SMT parts and the trend for semiconductor packages.
According to the 2019 mounting technology roadmap (JEITA Electronic Technology Industry Association), the composition ratio of multilayer ceramic capacitors reached the crosspoint between 0603 (0201") and 1005 (0402") in 2018, with the composition ratio of 0603 (0201") being the highest. Smartphones require compact placement areas and three dimensional placements in order to have more functions and maintain battery area. As a result, the proportion of 0402 (01005") parts is expected to grow in the future and reach around 20% by 2025. 0201 mm (008004") parts are also expected to see increased usage through 2022. In addition to the miniaturization of passive parts, the gap between adjacent parts is also becoming narrower every year and it is expected to reach around 50 microns by 2024. When placing parts onto panels with fine pitches between parts, there are cases in which the tip of the nozzle may come in contact with an already placed part if the nozzle tip protrudes from the edge of the held part, leading to placement defects. In such cases, optimal nozzle design and nozzle selection are important. In the future, placement quality will need to be more strictly controlled, but we will continue to develop placement machines that are both faster and more accurate while ensuring quality so that users can mount their products with peace of mind.
Next, we will cover semiconductor package trends. Semiconductor packages are becoming thinner and narrower from the demand for more pins, and they are shifting from large QFPs (Quad Flat Package) to BGAs (Ball Grid Array), and from small QFPs to QFNs (Quad Flat No-leads) and WLPs (Wafer Level Package). On the other hand, there is a demand for large and heavy BGAs for server products, and the NXT modular placement machine currently supports sizes up to 102 x 102 mm for standard specifications and up to 150 x 150 mm with custom specifications. Although there is a common trend toward more pins for the higher performance of equipment, the size and weight characteristics differ depending on the application.
A common theme in the production processes for SiP (System in Package) and module parts is the intertwining of cutting-edge placement technologies such as those for higher density placements, thinner structures, and multilayering. Figure 2 shows some of Fuji's solutions for producing SiP and other module parts. In addition to the figure below, as panels become thinner, it is necessary to be able to retain panels while correcting the deflection of the panel and keeping the height of the panel placement surface at a uniform height so that placement quality can be kept stable. In line with this, vacuum backup is effective for retaining thin panels. Vacuum backup uses vacuum pressure to retain thin panels on the upper surface of a vacuum plate to ensure that the part placement surface is at a uniform height. Vacuum backup also helps to reduce the impact of panel warpage and vibrations on the panel from the load to a minimal amount when parts are placed.
Figure 2: Fuji's solutions for producing SiP and other module parts
By using digital twin technology with smart factories, SMT lines are becoming more automated and digitalized. Digital twins are constructions of real world environments in a virtual world, to simulate those environments in the virtual space, and to predict and control what may happen in the real world in advance. We create proposals that incorporate digital Twins because we envision cases in which peripheral equipment such as AGVs are operated in concert with our pick and place machine, the NXTR (figure 3). This section explains our initiatives in the virtual and real worlds.
Figure 3: The NXTR pick and place machine
Models are created (figure 4) and then deployed in a virtual space to verify whether efficient production without waste can be achieved by changing operation through the introduction of automated equipment. Simulations are set up using parameters based on actual data from SMT lines, and it is possible to determine the necessary resources such as equipment and manpower, and the load ratio for each operation such as production, changeover, and parts supply, as well as to understand information related to operation such as how many AGVs are required in advance.
The operation of the entire SMT line can be accurately reproduced through simulation, and decisions on equipment selection and operation, which used to rely on the experience of the person in charge, can be visualized in an objective manner in a virtual space.
Figure 4: Simplified model of an SMT line
In order to expand the simulation conducted in the virtual world from 3-2-1 to production in the real world, it is necessary to create accurate production plans, and this has probably been a dedicated task because this requires know-how and skills. Therefore, we have a production scheduler tool in the host system that helps to create concrete production plans. This tool uses the various required data, such as the actual data for each process, the cycle time of each machine including the placement machines, and the production times, to create production plans for the entire SMT floor. It can also reflect various conditions such as the timing of parts running out, the number of parts, the floor life of parts, and the maintenance period of each unit, to help make the task of creating accurate production plans for the entire SMT floor as easy as possible.
We have been actively working to automate the external changeover area (the area where materials necessary for the next production are prepared) and the areas around the placement machines to support highly efficient production that does not depend on the skills of operators. However, we have not yet reached the point of fully automating entire SMT lines and reducing the number of operators to zero. For production lines, unintended problems and downtime may occur depending on the work starting time and work order. This means that there is a gap between the simulation of the virtual world and production in the real world that has been described so far, and it is difficult to say that smart factories evolving through digital twins has been realized. While our goal of "zero" downtime remains unchanged, we have developed software that guides the operator through the work in the optimal order and with sufficient time to ensure that downtime is as close to zero as possible. By guiding operators through the necessary tasks according to the progress of the schedule, such as picking (collecting materials required for production), changeover, distribution of materials to equipment, parts replenishment, and maintenance, operators can engage in tasks with confidence and minimize downtime, and this will help minimize downtime. In order to reduce the gap between the virtual world and the real world to "zero", efforts to monitor and control production conditions in real time and to achieve both high quality and high productivity will be continued, and this will support the realization of the evolving smart factory using digital twin technology.
A large portion of the workload in the SMT process is related to part and short stops occur due to issues such as pickup errors when supplying parts. In order to resolve this issue, Fuji has developed various automation units including auto loading feeders. The already mentioned NXTR takes automation a step further to completely automate the process of setting feeders in the placement machines. With the world's first ever "Smart Loader" for distributing, changing, and setting feeders for the placement machine, it is possible to automate part exchange work. On NXTR lines, by simply setting feeders at buffer stations positioned before the modules, the Smart Loader exchanges the feeders in production automatically according to parts out warnings and the changeover schedule.
Figure 5: Part exchange work by Smart Loader
Introducing the NXTR to SMT lines changes what manual work needs to be performed by automating the work related to part supply, as we explain below in steps. We envision a transformation from traditional "single stage" operation to "multi stage" operation. (Figure 6) In multi stage operation, preparation and collection work related to parts is centralized in one place, enabling production with a minimum number of workers. However, this is meaningless if production support with the minimum number of people causes an increase in the operator work load or downtime of the machines. These are simulated in the virtual world in advance, and accurate production planning and navigation tools for operation will enable you to achieve operation that is reasonable and has no waste.
Step 1: Single stage operation
A large number of operators for single stages that specialize in feeder replacement are assigned to deal with parts running out or being replaced in the conventional way (Multiple people working on one line).
Step 2: Multi-unit operation
By using a Smart Loader and having one person perform part exchange work at a buffer station, it is possible for one person to support multiple units (One people working on one line).
Step 3: Multi stage operation
By having feeder magazines (magazines in which feeders are set) on the buffer station being exchanged by AGVs, the work performed in front of the machine by operators becomes "zero".
Figure 6: Changes in manual work through automation
In addition to automating SMT processes, we have also been automating insertion processes for the stages after the SMT processes with the multipurpose automated fabrication machine - sFAB-D. In 2021, as new solutions for the manual insertion process, we have developed the sFAB-SH (figure 7), which maintains the excellent flexibility, scalability, and productivity of the sFAB-D, while focusing on the functions required of a standard panel assembly machine, and we have developed the Panel Assembly Robot Cell - SmartWing BA (figure 8) as part of the Advanced Robot Cell series for the compact multijoint robot SmartWing. sFAB-SH flexibly handles everything from high-speed insertion to insertion of large parts up to 55 mm in height and 200 g in weight with two types of heads; the sH08-SH head and the sH02-SH head. This machine also supports part lead chucks and cutting and clinching to support reliable insertion quality. In addition, defects that are the cause of repair work after parts have been soldered are prevented. Such support includes the high-resolution vision processing system that prevents inserting parts in the incorrect direction and an optimal motion sequence that pushes the part securely with insertion detection to prevent floating parts. The SmartWing BA excels in the automation of limited types of parts such as connectors, coils, relays, transformers, and large electrolytic capacitors by using a horizontal articulated (SCARA) robot. Part insertion using a SCARA robot may not be new robot technology, but the SmartWing BA is low cost and enables short setup times by providing the necessary functions as a package, and it can be put into the production line immediately without requiring manual work and system setup by system integrators.
Figure 7: Multipurpose Automated Fabrication Machine – sFAB-SH
Figure 8: Panel Assembly Robot Cell - SmartWing BA
A board on which parts from small sized parts to large and heavy parts that were automatically inserted by an sFAB is shown in figure 9. It is possible to automate the insertion of various parts such as these. There are various requirements for automating insertion. They range from low-cost automatic insertion of just a few parts to high-speed automatic insertion of all parts. We will intently listen to the voices of our users regarding the future vision of their processes and factories, provide optimal solutions, and promote proposals for the realization of smart factories that revolutionize manual work through automation and achieve high operation rates and high profitability, just as we do with placement machines.
Figure 9: Board with automatically inserted parts by an sFAB
In this article, we have introduced our initiative for simulating the real world in the virtual world for the SMT stage as well as covering our various solutions for automating the insertion process. We will continue to support our users' realization of smart factories with the evolution of digital twin to link SMT lines with the digital world. We ourselves believe that automation is one of the ways to reduce the gap between the virtual world and the real world to "zero", but we believe that this is not the only answer. We will continue to listen to our users and develop products and services that exceed their expectations.
Note: This article is a modified version of an article that appeared in the journal "Robot" issue 263.