Challenges in LED display production
In today's LED display market, there is a growing demand for higher definition images.
This trend is also driving significant changes in display technologies and production processes, which have resulted in the following challenges when manufacturing LED displays.
Marketplace demands
- Smaller and more complex parts
- Finer pitch circuits
- Increased number of placed parts
Current status of SMT production sites
- Labor shortages and surging labor costs in the manufacturing industry
Solutions from Fuji
In response to these market trends and production site issues, Fuji has the optimal solutions.
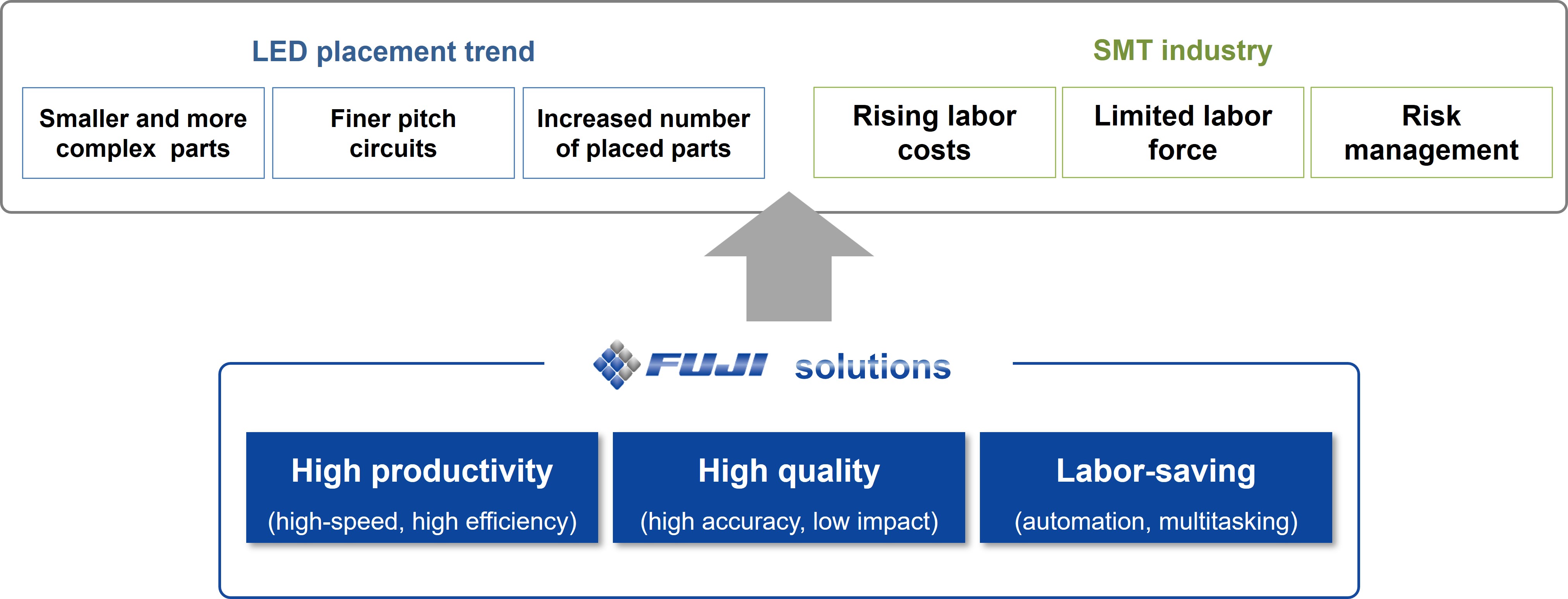
Based on our three key strengths of "high productivity", "high quality", and "labor saving", we can offer the following solutions.