- Plan
- Part picking
- Offline
changeover - Production
- Performance
management
and analysis - Maintenance
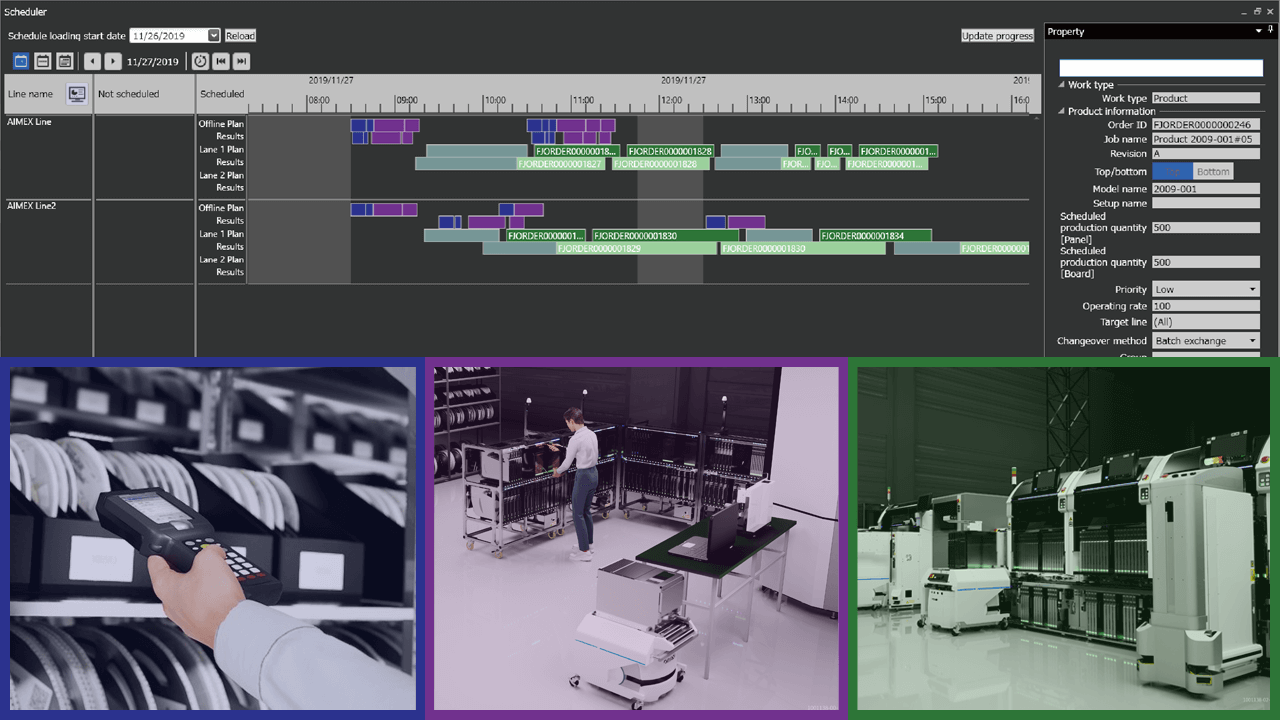
Create schedules for the entire production floor, including operation at the production line and offline tasks
Nexim Scheduler (scheduling tool)
NXTR SNXTR A
This can streamline the creation of production schedules which is a time-consuming manual process.
- Schedule planning (operating time, changeover method, etc.) optimized for production conditions
- Schedule planning based on desired conditions (production line specification, same reflow temperature profile, etc.)
- Imports created schedules from upper host systems to display in Gantt charts.
Prevent the repeating of tasks once production preparation has already begun
Nexim Scheduler (part allocation)
NXTR SNXTR A
It is possible to allocate (reserve) the required parts based on the set schedule. This makes it possible to check that the inventory is there, preventing the repetition of tasks due to a lack of the necessary parts after production preparation has begun.
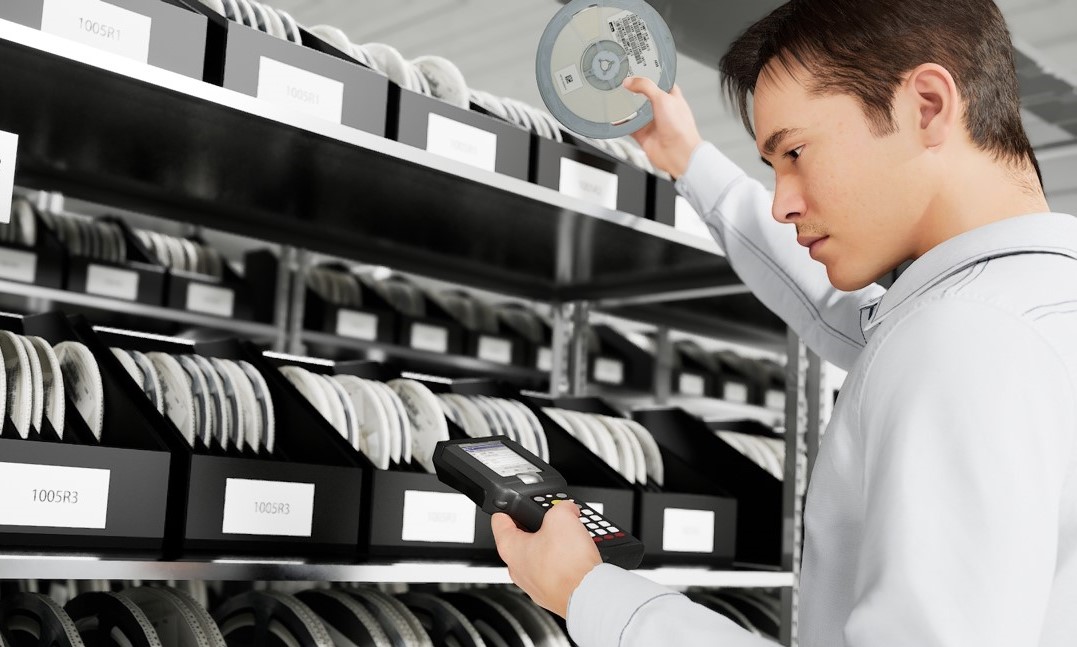
Efficiently collect the necessary parts using the shortest route
Material Navigator Mobile
NXTR SNXTR A
Parts are taken from the shelf in the order they are listed in Material Navigator Mobile, and scanned to complete the picking sequence.Note
Because work can be performed while checking against the system, even inexperienced operators can collect parts quickly and accurately.
Note: When using Nexim Scheduler
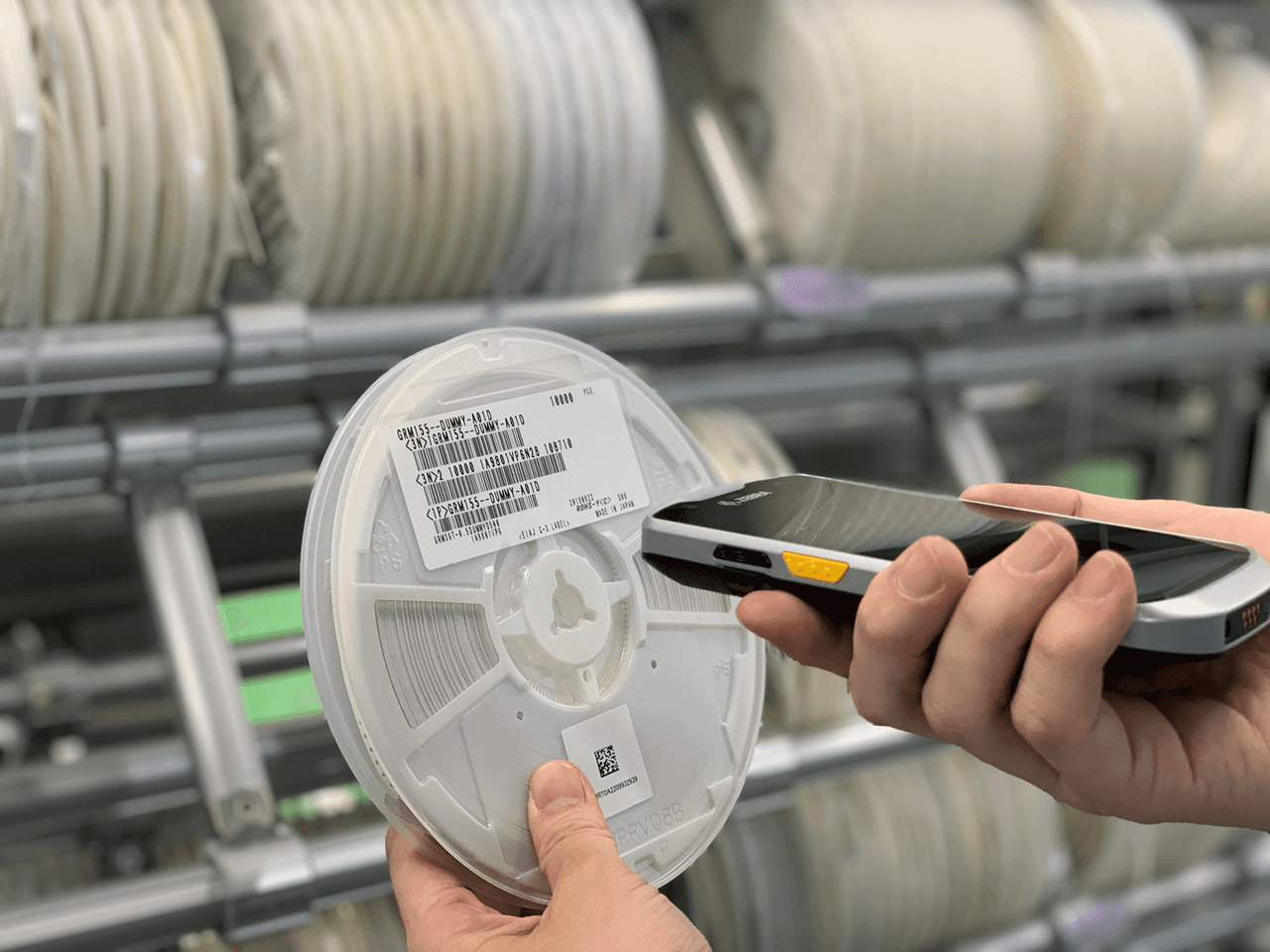
Error-free checkout of the necessary parts
Linking with an automatic part warehouse
NXTR SNXTR A
Parts can be checked out of an automatic part warehouse simply by sending the information for the necessary parts from Integrated Production System - Nexim to the automatic part warehouse.
This automated work drastically reduces the time taken compared to manual processes, as the right parts can be picked without the need to search for them.
To learn more about material storage solutions that support automatic checkout, please contact us.
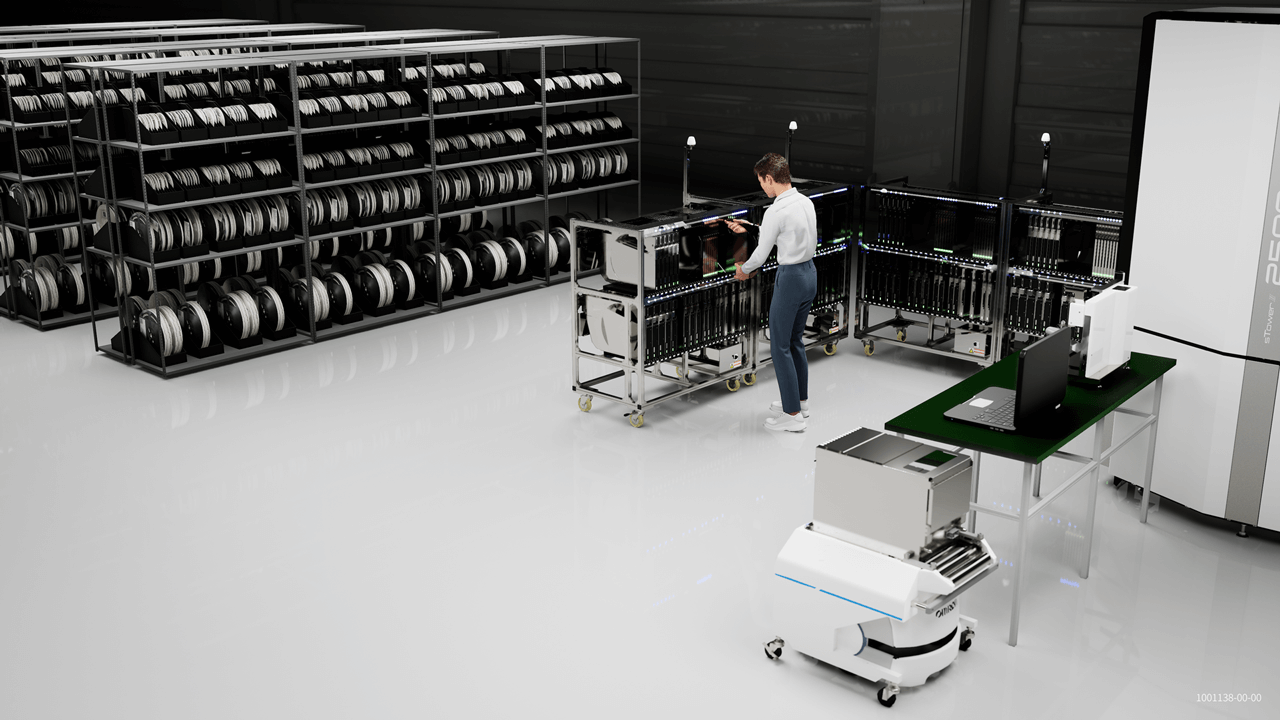
Guidance is issued for the work that needs to be done and the order that it should be done in based on priority
Kitting navigation
NXTR A
Guidance is issued so that operators know what work needs to be done in what order to ensure that the necessary parts can be supplied to the placement line without delay.
Since the feeders are loaded to the placement line by the Smart LoaderNote, the operator can concentrate on the task of packetizing reels into feeder magazines without needing to worry about the position they are loaded to. Packetizing simplifies the work process, preventing downtime caused by operator mistakes and operational delays.
Note: An automatic feeder exchange system that is used for NXTR A model
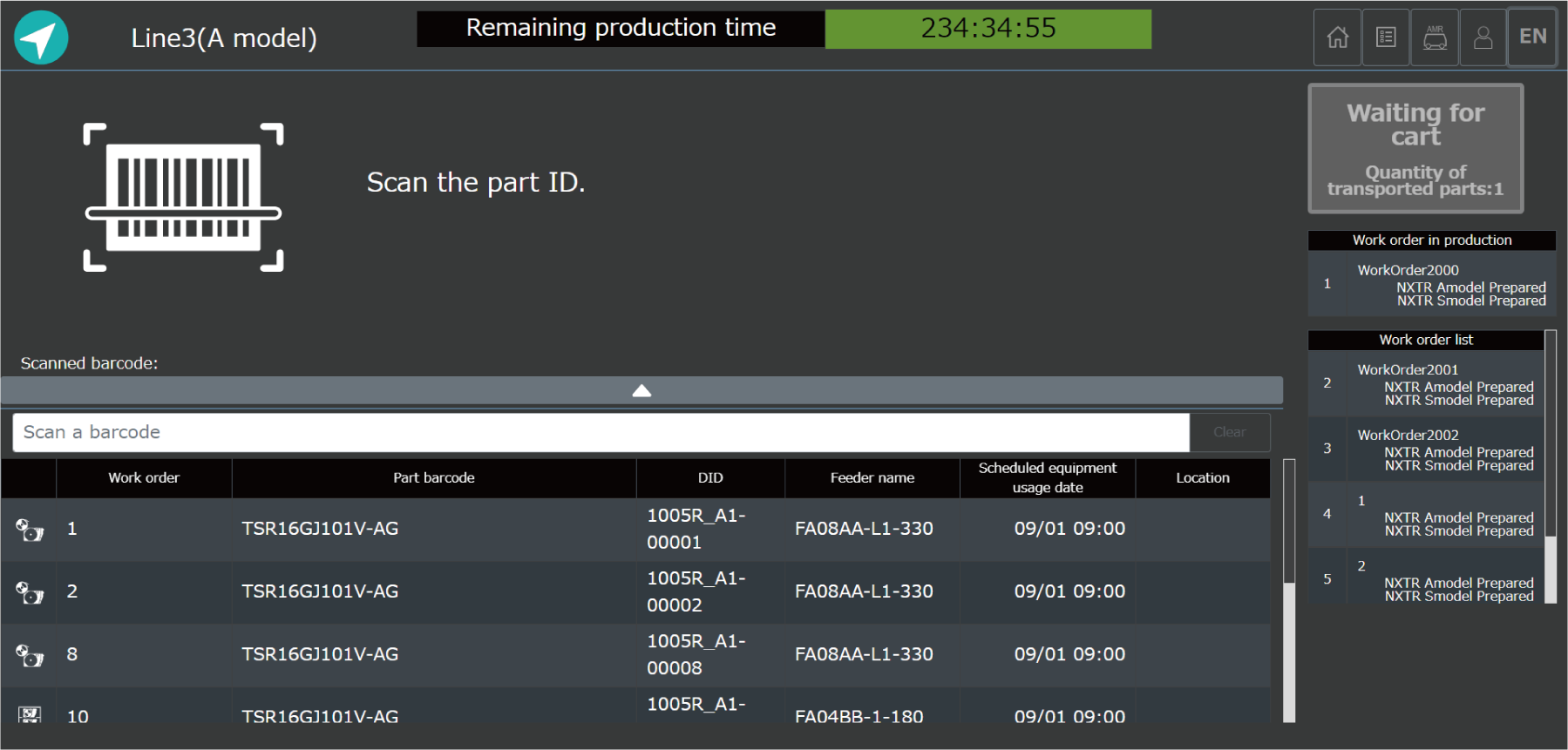
Check the status of feeders at a glance with LEDs
Advanced feeder stand
NXTR A
Advanced feeder stand indicates the status of a loaded feeder using LED patterns. The visual identification of whether a feeder is usable or not makes it possible for operators to tell which feeders can be removed without hesitation.
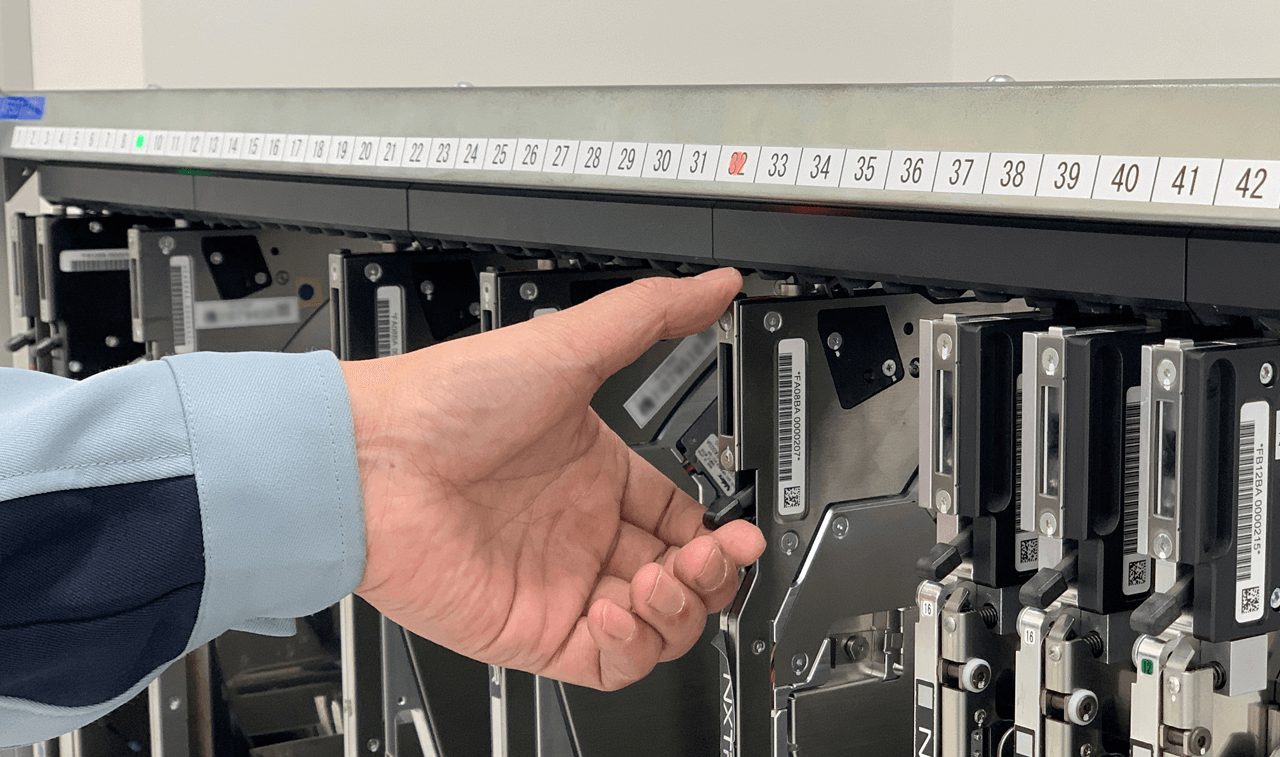
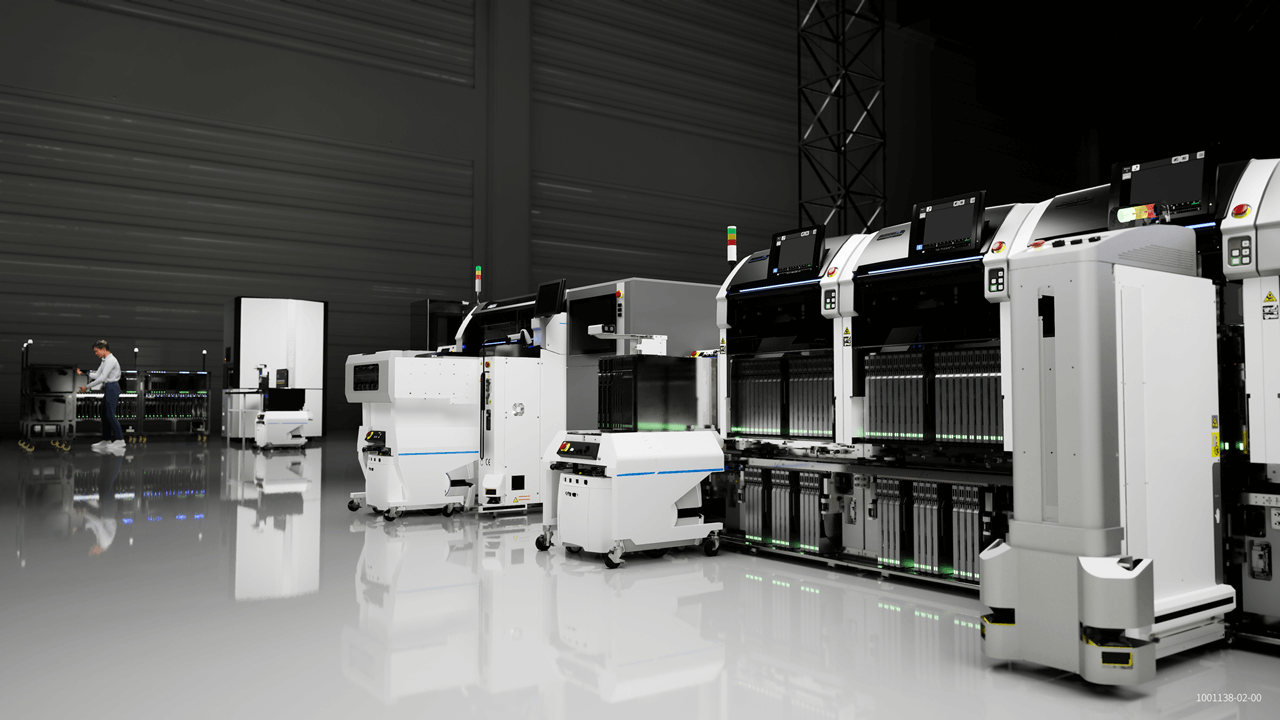
Scanning an ID code changes the production program for the entire line
Automatic changeover for entire lines
NXTR SNXTR A
Programs for all machines in the line configuration can be changed just by scanning the kanban ID or panel ID code.
This removes the risk of selecting the wrong program and reduces the workload during changeover, leading to an improved operation rate.
Maintain solder printing quality by linking with SPI machines
Feedback from SPI to printer
NXTR SNXTR A
Inspection results are received from the SPI, and the appropriate response to trends that show a change in conditions can be performed automatically.
Because changes such as positional deviations and smeared or missing solder are responded to before they lead to problems, high-quality solder printing is maintained.
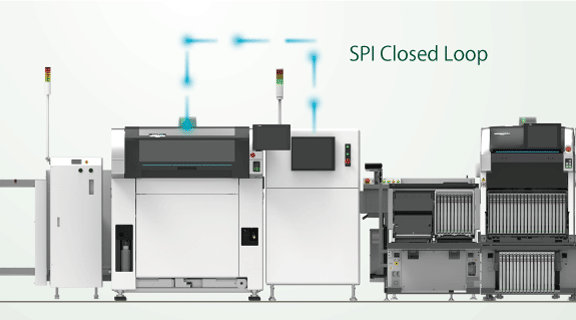
Maintain high-accuracy parts placement by linking with AOI machines
Offsetting the placement position
NXTR SNXTR A
Trends in changes in placement accuracy are picked up on based on the AOI inspection results, and placement positions are corrected automatically.
Because these changes are responded to before they lead to problems, high-accuracy part placement is maintained.
In the unlikely event that the AOI detects a sudden defect, the line is stopped to prevent defective products from continuing to the next stage.
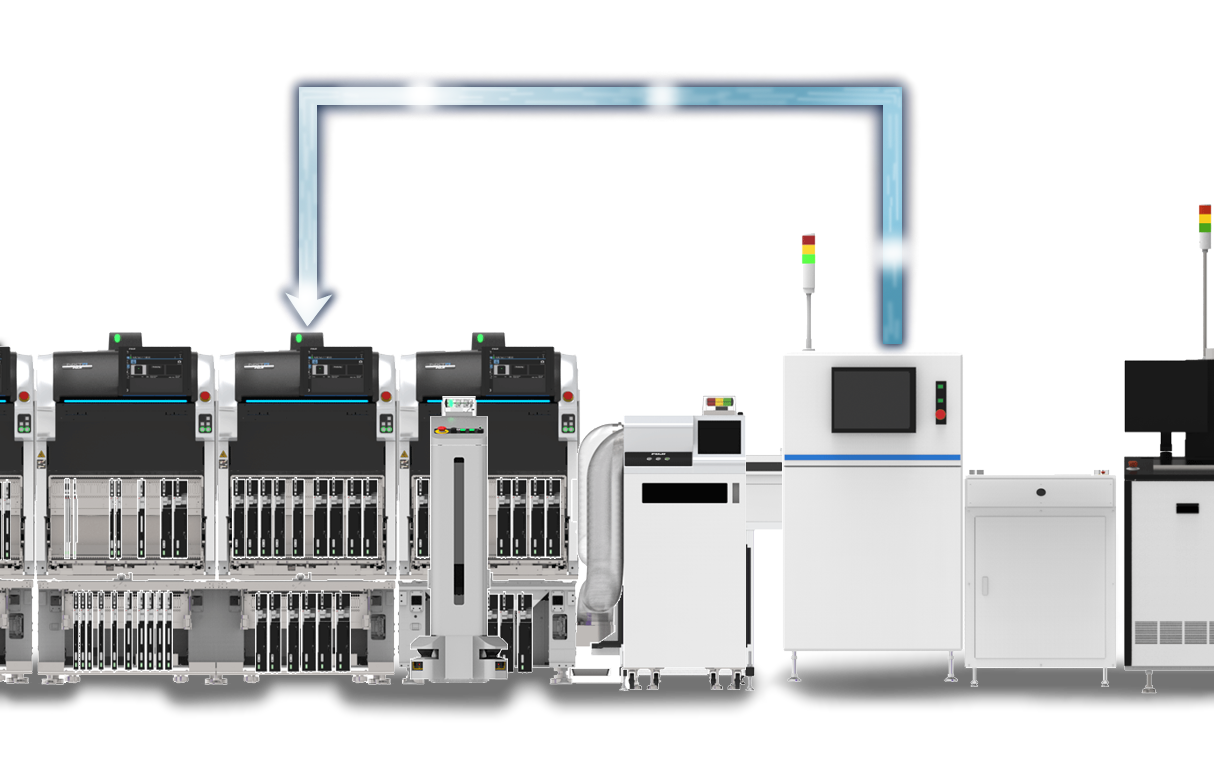
Avoid placing parts on boards that have poor solder print quality
Remote board skip
NXTR SNXTR A
Part placement is skipped for boards that have poor solder printing based on the SPI results, preventing the production of defective products.
It is also possible to skip part placement on boards that have not passed inspection on multiboard panels.
Verifying materials before use prevents setting mistakes and stops parts that are past their use by date from being used
Verification for printers and pick and place machines
NXTR SNXTR A
The IDs for the parts and materials to be used in production are scanned and verified with the system to prevent setting mistakes.
It is possible to manage the use by dates for solder and the usage count for materials, preventing materials that might cause defects from being used, for continuous high-quality production.
Never overlook line errors
FSF Mobile Conductor
NXTR SNXTR A
Error and warning notifications are sent to mobile terminals held by operators. By preventing error and warning signs from the equipment from being overlooked and encouraging prompt action, the system helps to maintain uptime with fewer personnel.
It can also be used as a notification tool to implement work in a timely manner.
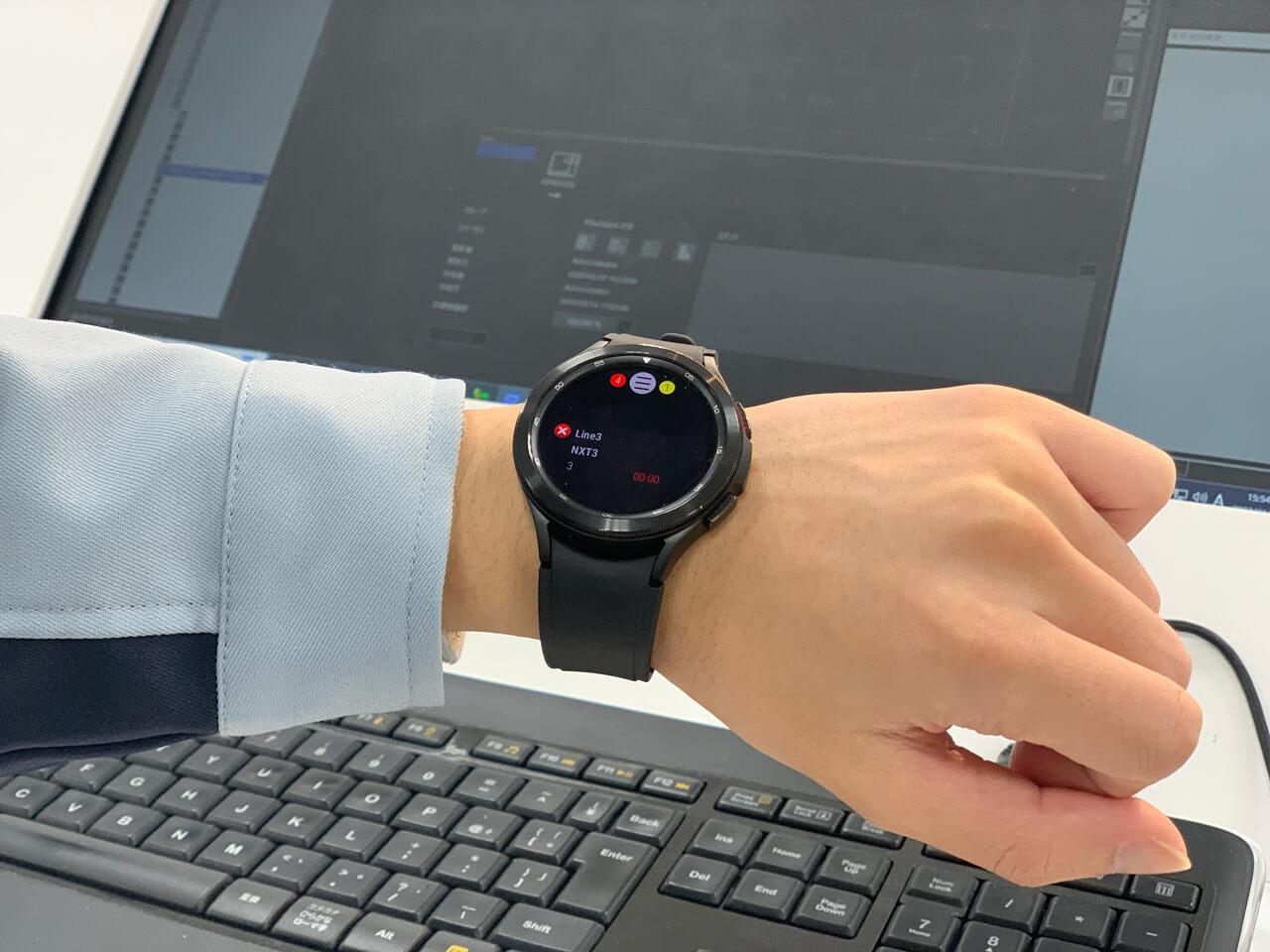
Learn fast, act quickly when line errors occur
IPQC Expert
NXTR SNXTR A
This system analyzes information collected from the pick and place machine production data to check for changes and provides guidance for the best remedy to the problem that has occurred.
Errors can be picked up on based on short-term trends, so that the issue can be addressed before it becomes a larger problem.
Managing the use-by time restrictions (floor life) of parts that are sensitive to humidity
Dry components
NXTR SNXTR A
Steam ruptures during reflow can occur for parts that are sensitive to moisture. Managing the floor life after opening the parts’ moisture-proof packaging prevents this from occurring.Note
It is possible to bake these parts in a dry oven to reset the floor life.
Note: It is necessary to register the storage location in Nexim
Feeders are set and collected automatically
Smart Loader
NXTR A
Feeders are exchanged automatically starting from the machines that have already finished production, keeping down time for changeover to a minimum. Feeder exchange for parts resupply and collection of feeders that are not scheduled for use are performed automatically, greatly reducing the amount of time operators need to be present at the production line.
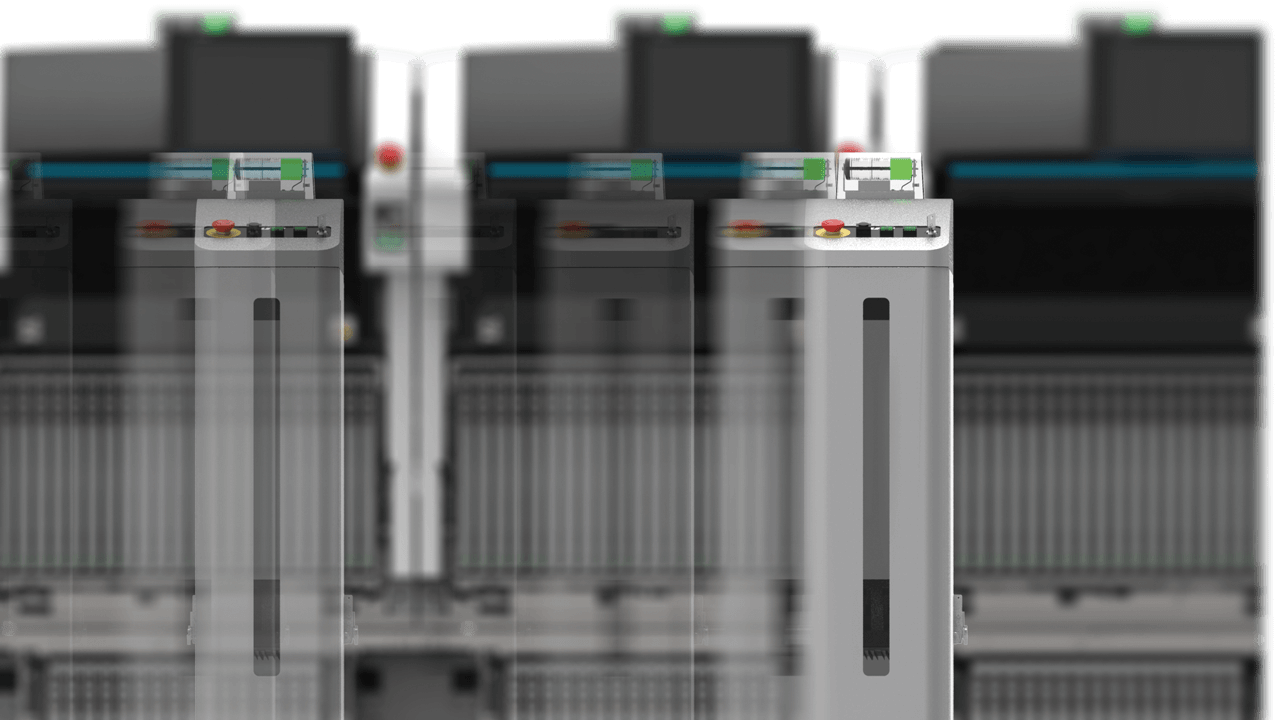
Maintaining quality and productivity through automatic exchange of printing materials
PM Smart Changer
NXTR A
Automatic exchange of metal stencils and backup blocks reduces operator workloads and changeover time.
In addition, the machine's internal temperature can be maintained because material replenishment can be completed without opening the front cover. Since this reduces changes in the state of the solder, high-quality printing can continue even after changeover.
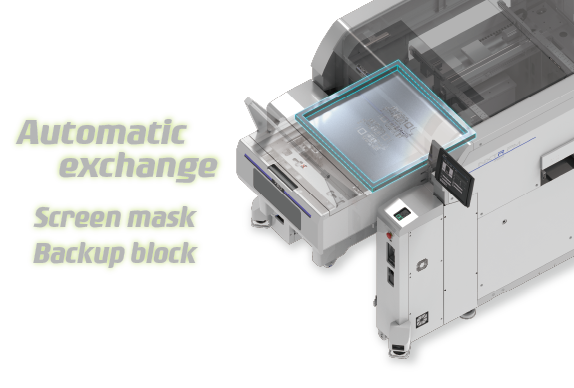
Automating material transport
Automatic transport by AMRs
NXTR A
The necessary feeders, metal stencils, and backup blocks are automatically transported to and loaded into the line by AMRs, which also collects these items after use.Note
Automating transport to the line helps to reduce operator workloads, something that is much needed at production sites facing staff shortages.
Note: Dedicated transfer carts are used for transport
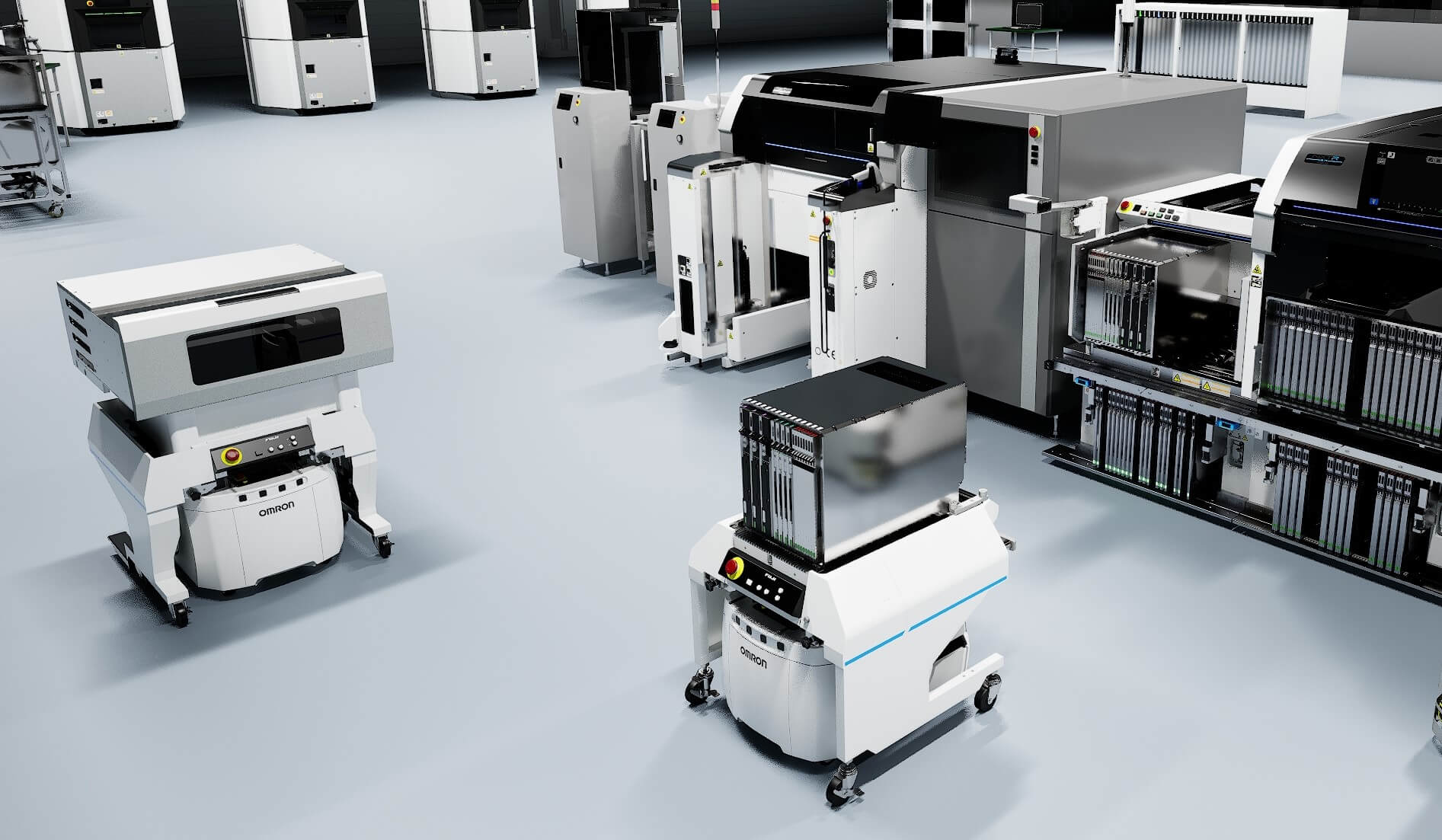
Efficient waste tape collection
Waste tape collection unit
NXTR A
Waste tape is expelled from each pick and place machine and collected into one location.
The collection of waste tape can be emptied at any time without stopping the machine.
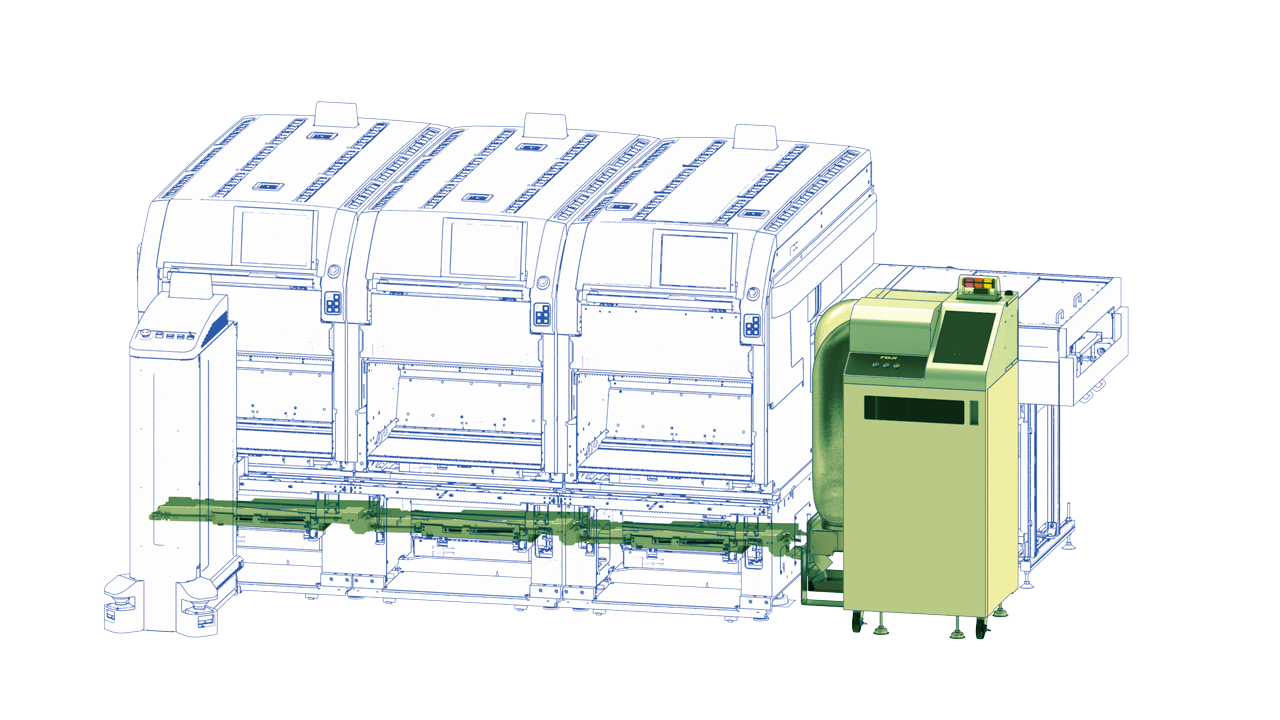
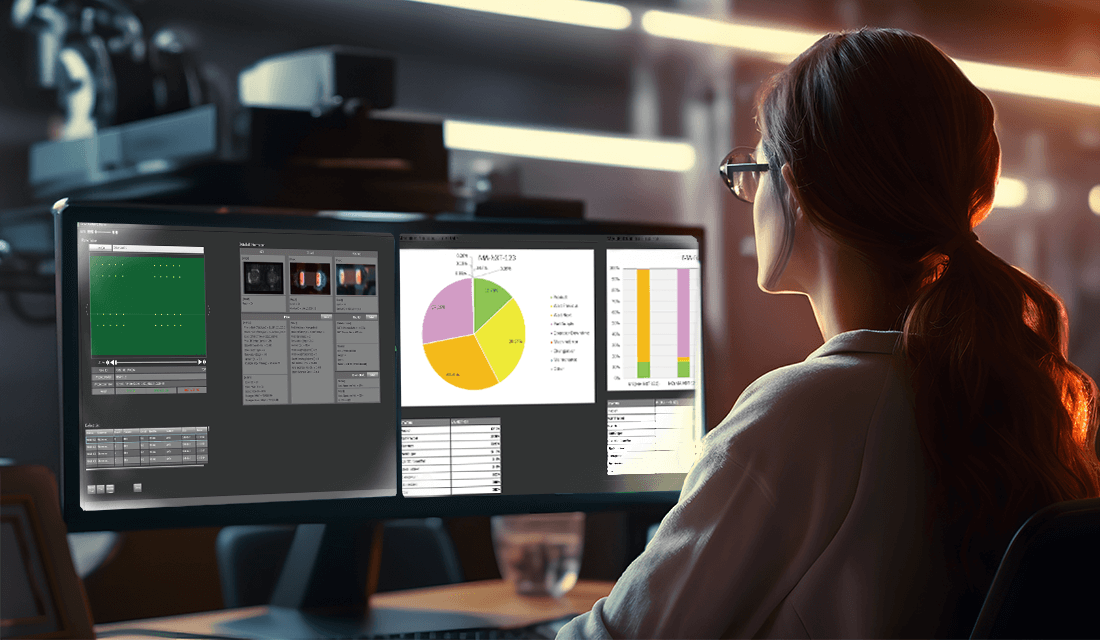
Visualize data at multiple levels, from visualization across all lines to visualization of detailed statuses of each machine
Management Monitor
NXTR SNXTR A
The operation status of all production lines is shown in a single screen. Visualized error notifications encourage prompt responses.
Detailed information for lines at which an error has occurred can be checked by individual machines, making it possible to quickly identify and respond to the cause of the error, preventing any further repercussions.
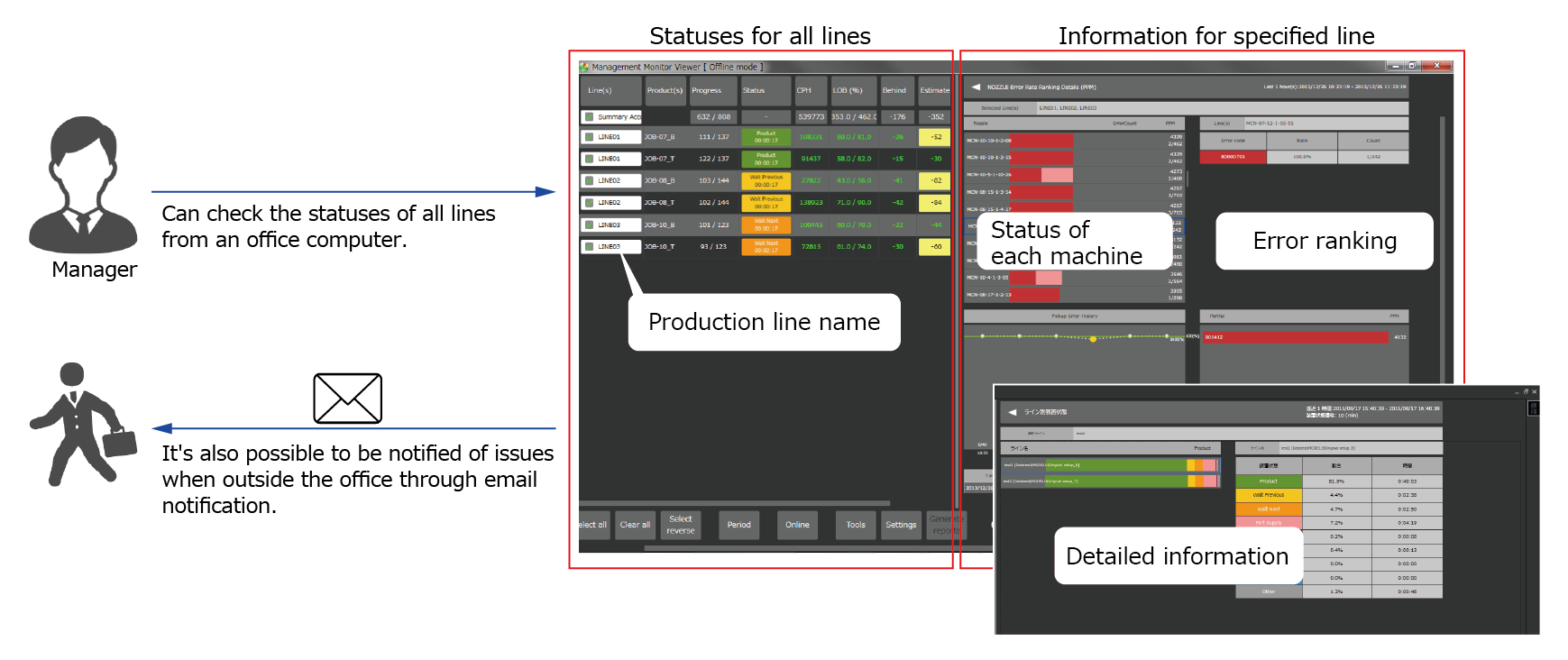
Display the production status of each line in one screen
Advanced Dashboard
NXTR SNXTR A
The machine conditions and production status for a line are shown in line images and graphs.
Various information, including the progress status and quality drop trends, are displayed graphically, allowing operators to grasp the production status of the target line at a glance.
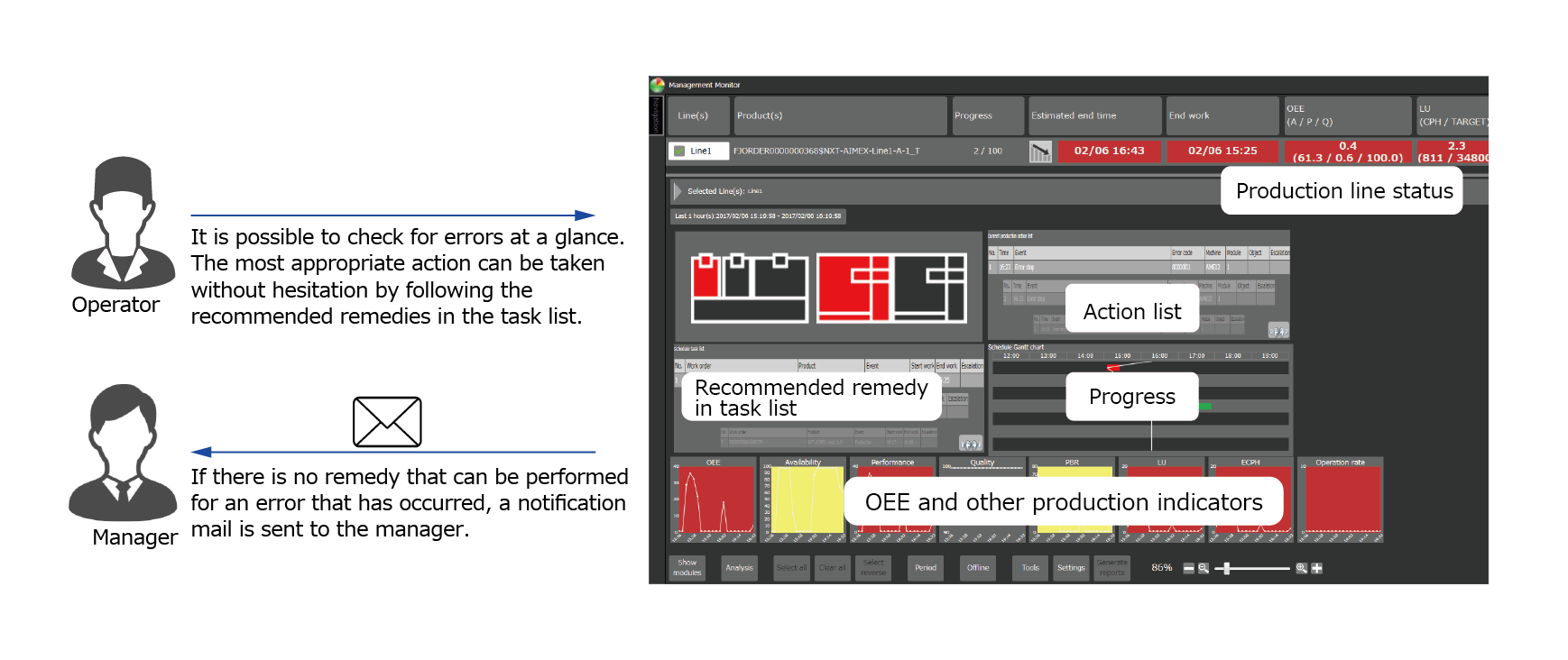
Display traceability data and inspection images for target panels in one screen
Defect Analyzing Master
NXTR SNXTR A
SPI and AOI inspection images, settings for each machine, and performance information are all displayed in one screen based on the ID code for panels determined to be defective.
Inspection images can be used to narrow down which process caused the defect, enabling quick identification of the cause.
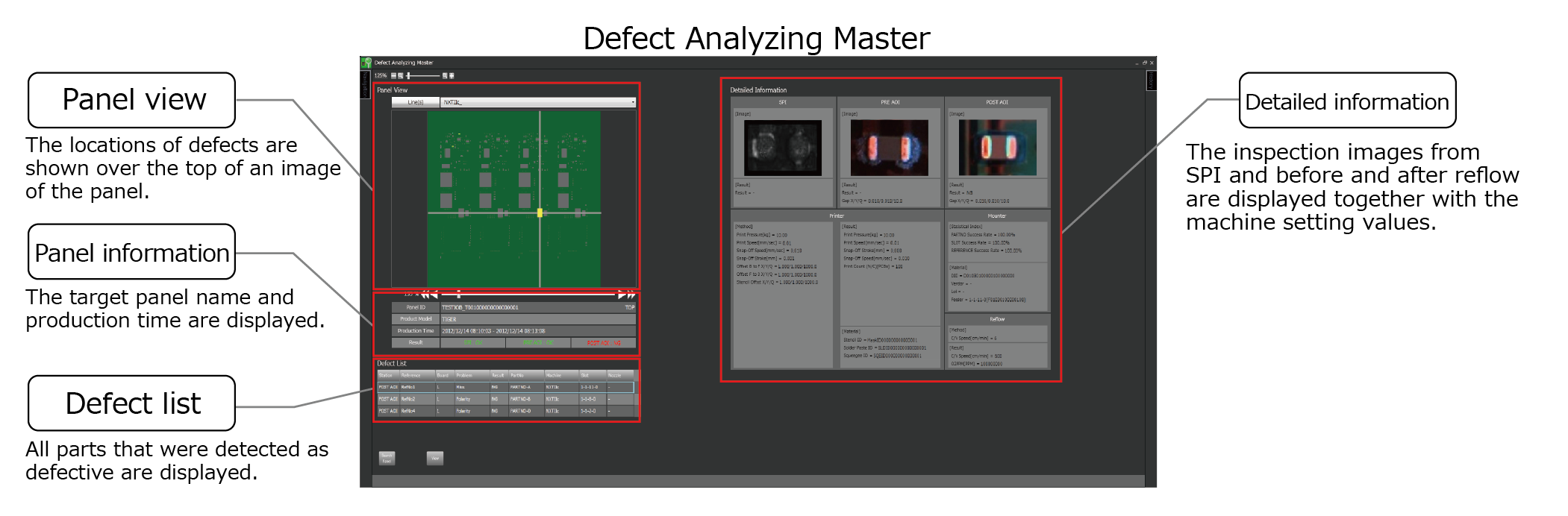
Automatically output reports that are useful for identifying areas that can be improved
Production reports
NXTR SNXTR A
Easy to read reports of production results for a set period of time can be collated and then output.
There are various types of production data such as the operation statuses and error information that can be used to identify areas that can be improved.
Automatic sending to set email addresses is also possible.
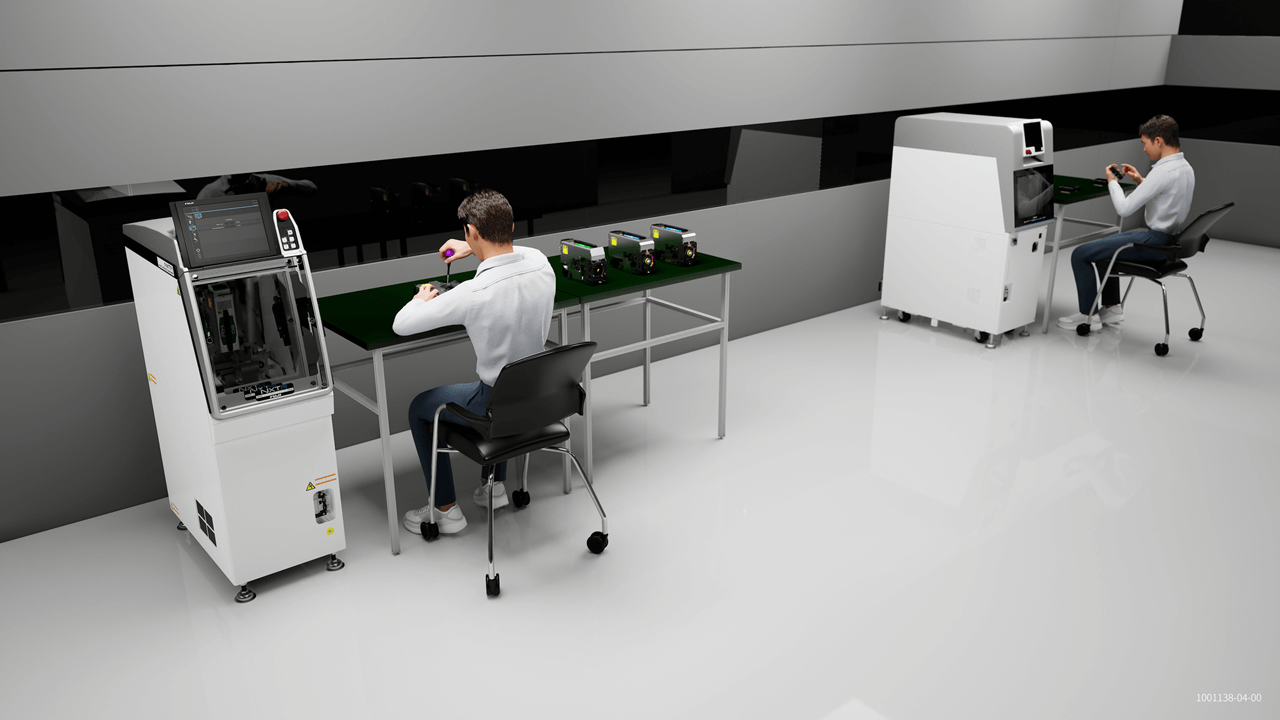
No need to have dedicated manpower for maintenance
Automatic maintenance units
NXTR SNXTR A
Automatic maintenance of feeders, nozzles, and heads removes the dependence on experienced staff.
Fuji’s automatic maintenance units clean and check the performance of maintenance items, to enable production that remains stable without fluctuations in quality.
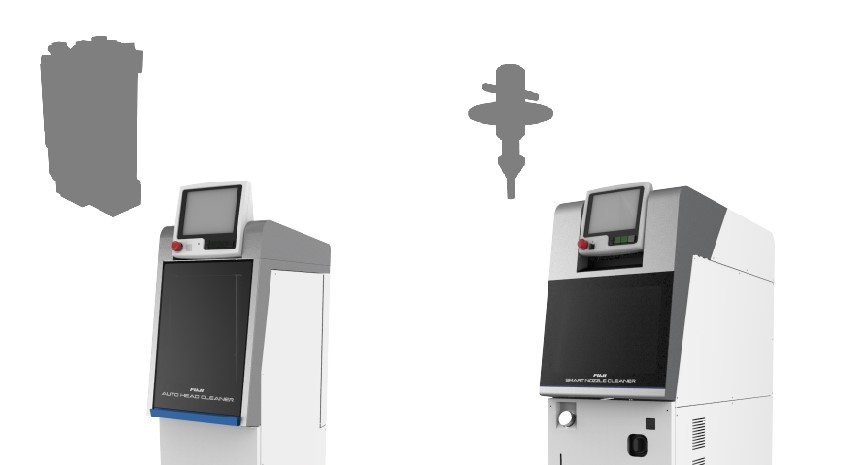
Taking the hassle out of maintenance management
Advanced maintenance
NXTR SNXTR A
Data such as the pickup rates and usage time is collected. Once a unit has reached a predetermined threshold, guidance is issued for the time to perform maintenance.Note
Follow the guidance in advanced maintenance to keep your equipment in top condition for production with little effort.
Note: For heads and nozzles
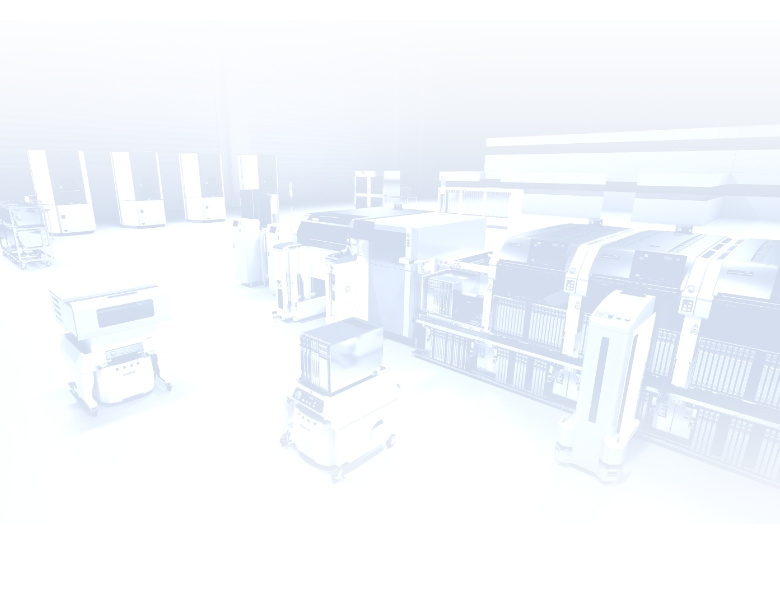