Offline setup for production is still a process that relies heavily on human labor and thus has a higher risk of mistakes when compared to increasingly automated production lines. The frequency of changeovers and number of part types required when changing product models has increased in recent years with the shift to high-mix production, resulting in a higher risk of mistakes. It is also a difficult task to track for management, as progress is hard to quantify.
This page contains information pertaining to parts management solutions for production using Fuji intelligent feeders.
Do you have any of these issues when preparing for production?
Picking parts takes a long time
Picking can take a long time if workers do not have clear instructions for where they can find the parts that they are looking for
Picking errors occur
Parts are checked simply by looking at them, so the wrong parts are sometimes picked up by mistake
Setup work takes a long time
Setup work can take a long time because it is necessary to check that the loading position is correct for each part feeder
Line stops caused by parts running out
The realization that there are not enough parts often comes after preparation for production has begun, resulting in sudden scheduling changes and the corresponding extra work required, as well as stop time at the production line
Parts remain on the production floor
Parts that are no longer needed in production remain on the production floor without being collected, making it impossible to accurately determine the quantity of parts in stock.
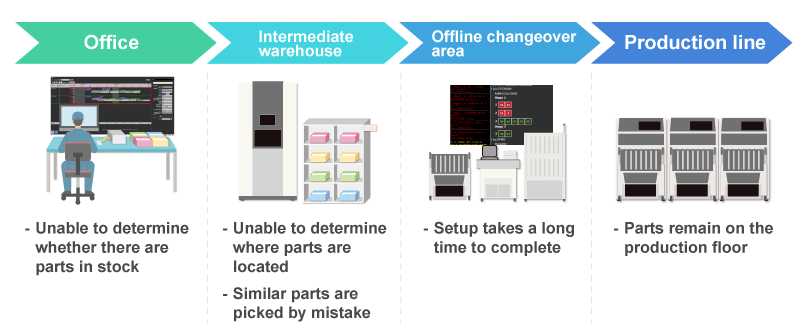
Nexim part management solutions
Nexim part management solutions are used to track the movement of parts by scanning the ID codes that are affixed to parts and units.
The Integrated Production System - Nexim collects, organizes, and updates scan data in real time, creating a state in which information is matched up with its physical counterpart, helping to ensure that there is no waste, unevenness, or needless work while preparing for production.
Planning phaseSchedule creation
No more downtime due to parts shortages, preventing part backlogs from occurring- Nexim Scheduler
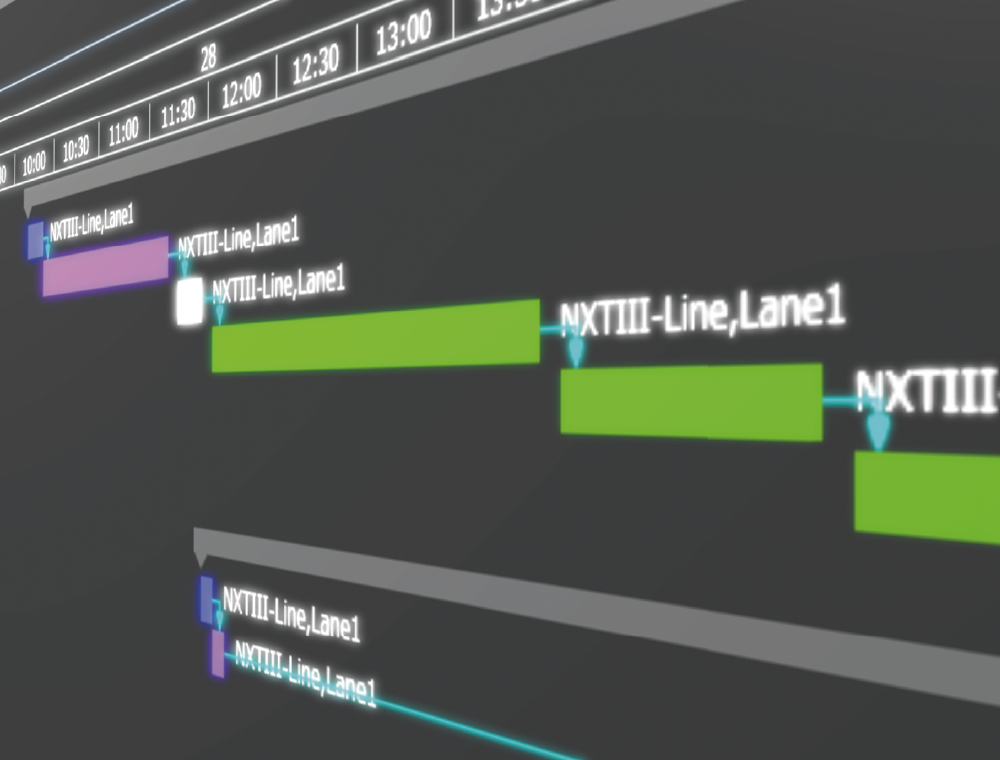
By allocating (reserving) the necessary parts when creating a schedule, it is possible to check the inventory before starting to prepare for production and ensure that the required parts are not used at another production line.
Parts that can be allocated are not limited to the parts warehouse. It is also possible to allocate parts within the entire production floor, including those at the line side, thus preventing parts that have already been used in production from remaining on the production floor for a long period of time.
Production preparation phasePart picking
Picking guidance issued by location minimizes operator work paths and reduces workloads- Material Navigator Mobile*1
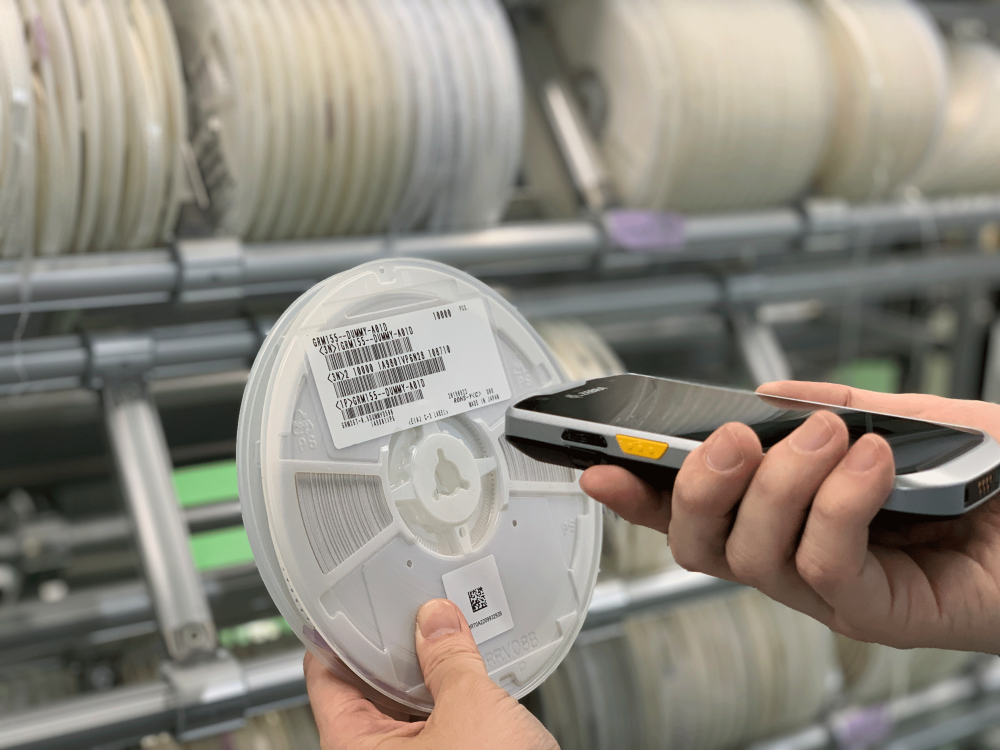
Because the parts to be picked are listed by shelf, part picking takes the shortest route possible.
Picking completion information is updated in real time, enabling multiple people to pick at the same time.
By scanning the ID code on the parts reel when picking, the status that picking has been completed is registered automatically in Nexim. The ID codes on parts reels are simultaneously checked against the information in the system when scanned, preventing picking errors.
This prevents omissions while parts are being moved around, and ensures accurate management of part locations and stock levels.
*1: Material Navigator Mobile is software for PDA terminals that supports offline preparation work such as picking.
Production preparation phaseOffline changeover
Effective offline changeover in a short time without any confusion- Nexim Kitting Station and offline changeover power unit
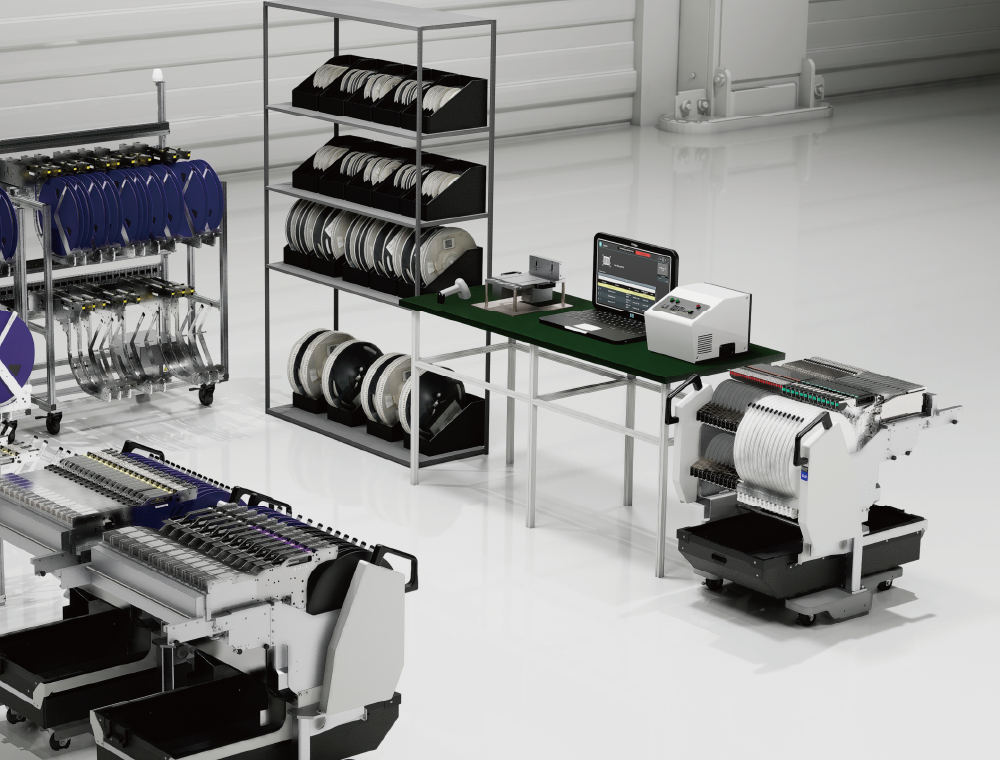
When an ID code on a parts reel is scanned, guidance is displayed on the Nexim Kitting Station monitor.*2 An icon changes color to indicate whether the correct feeder was loaded, ensuring that the work is done correctly even when performed by inexperienced operators.
It is easy to remove parts from feeders that are no longer needed in production using the automatic rewinding operation on feeder carts. When preparing for next production, only the parts that are not scheduled to be used can be rewound, eliminating the need for confirmation and thus making the task more efficient.
*2: It is necessary to register this in Nexim in advance.
Check the status of feeders at a glance with LEDs- Advanced feeder stand for Fuji intelligent feeders
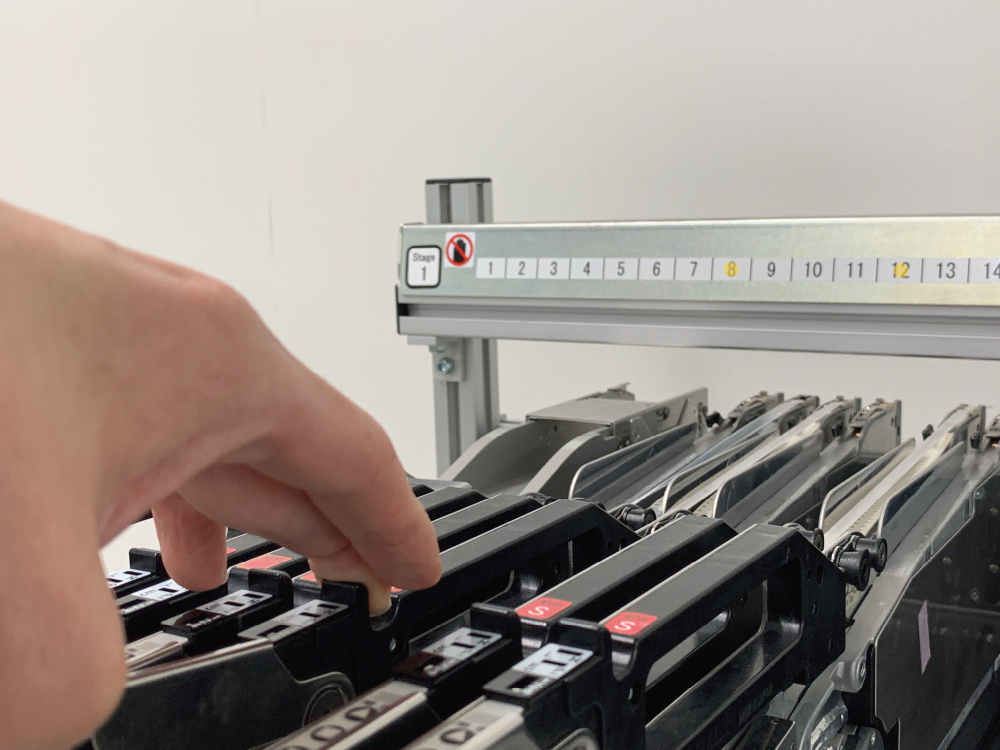
The advanced feeder stand for Fuji intelligent feeders indicates the status of a loaded feeder using LED patterns based on the production schedule.*3 Usable feeders can be ascertained at a glance, taking the pain out of looking for feeders and improving work efficiency.
It is possible to identify feeders that need maintenance and feeders that are loaded with parts for which the floor life has expired, so it is possible to avoid using parts that might lead to defective products, and prevent the deterioration of production quality.*4
*3: When using Nexim Scheduler.
*4: When using option functions “Advanced Feeder Maintenance” and “dry components”.
Effective changeover in a short time- Nexim Kitting Station
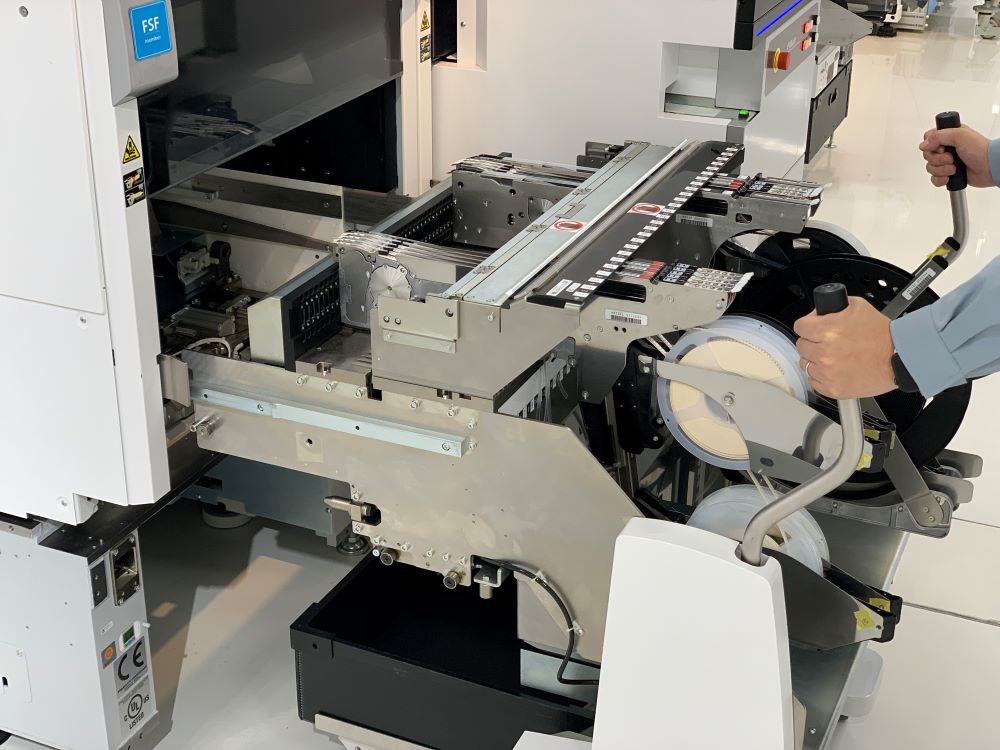
It is also possible to check the destination for prepared feeder carts (line name, machine name) in Nexim.
This makes it easy to identify the target machine for changeover, and enables reliable work in a short time, while also reducing workloads.
The Nexim parts management solutions introduced here support production preparation, from parts picking to offline setup, so that work can be performed without hesitation and without waste. These solutions are also effective for improving the efficiency of management operations because production activities can be conducted in a state in which information is synchronized with its physical counterpart.
The units and functions to be used may differ depending on the machine. Please contact us if you have any further questions about these or any other solutions.