AIMEX III
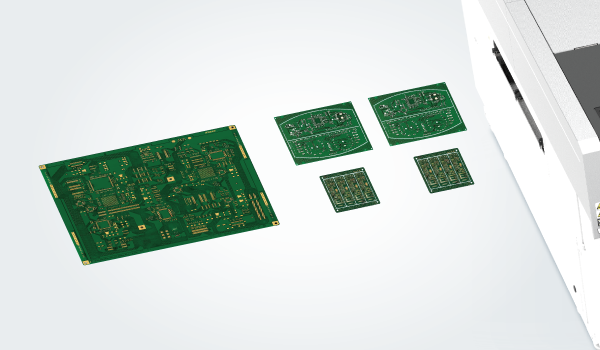
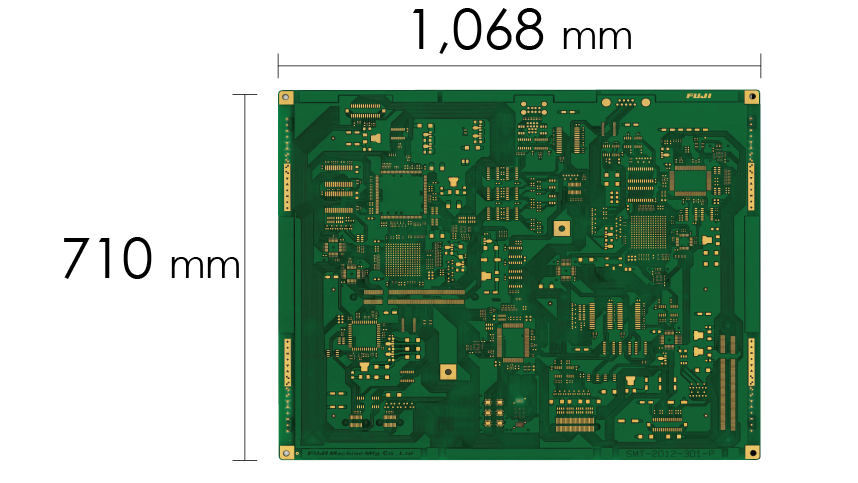
シングルコンベアで最大1,068×710mmまでの大型基板生産に対応できます。
(※オプションでwidth:1500 mmまで対応)
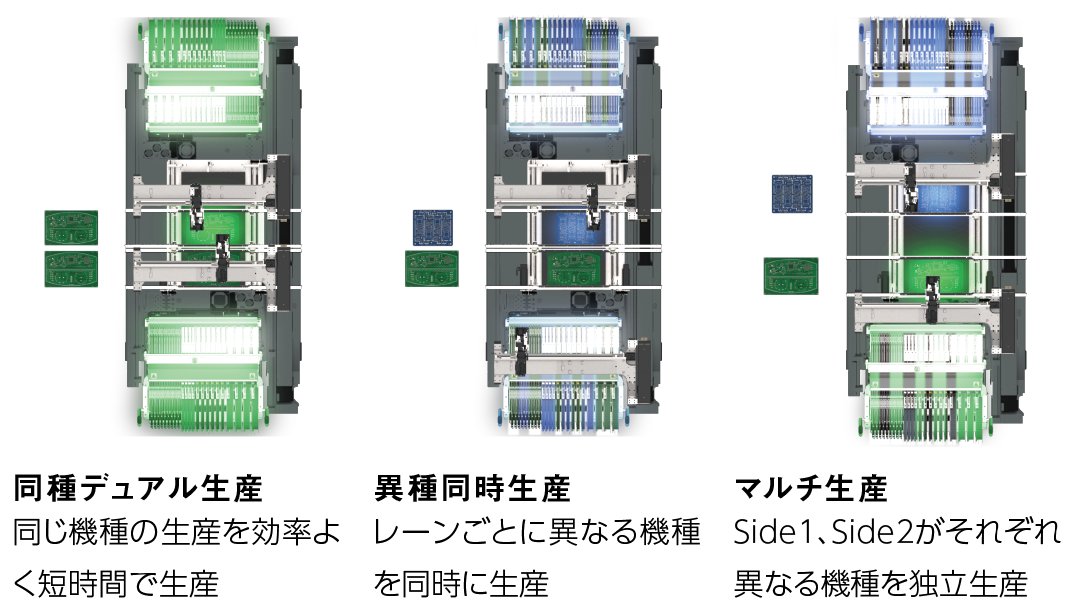
ダブルコンベアにより異種の製品を同時に生産し、基板の搬送時間を実質ゼロにすることが可能です。また、2ロボット仕様にすることで生産の幅を広げます。
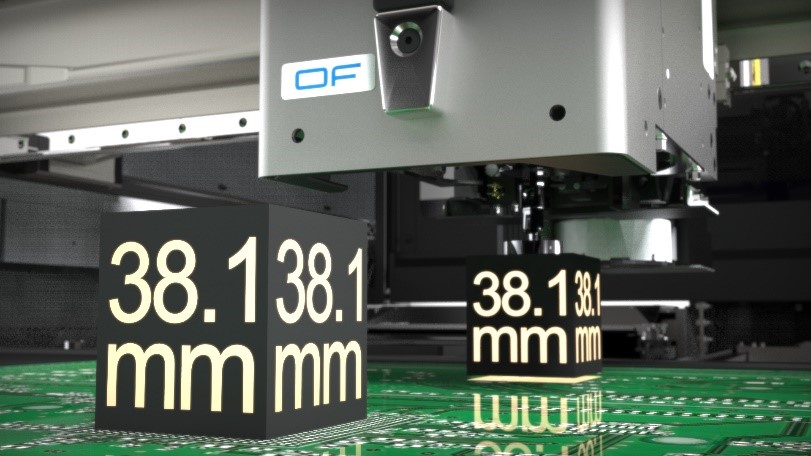
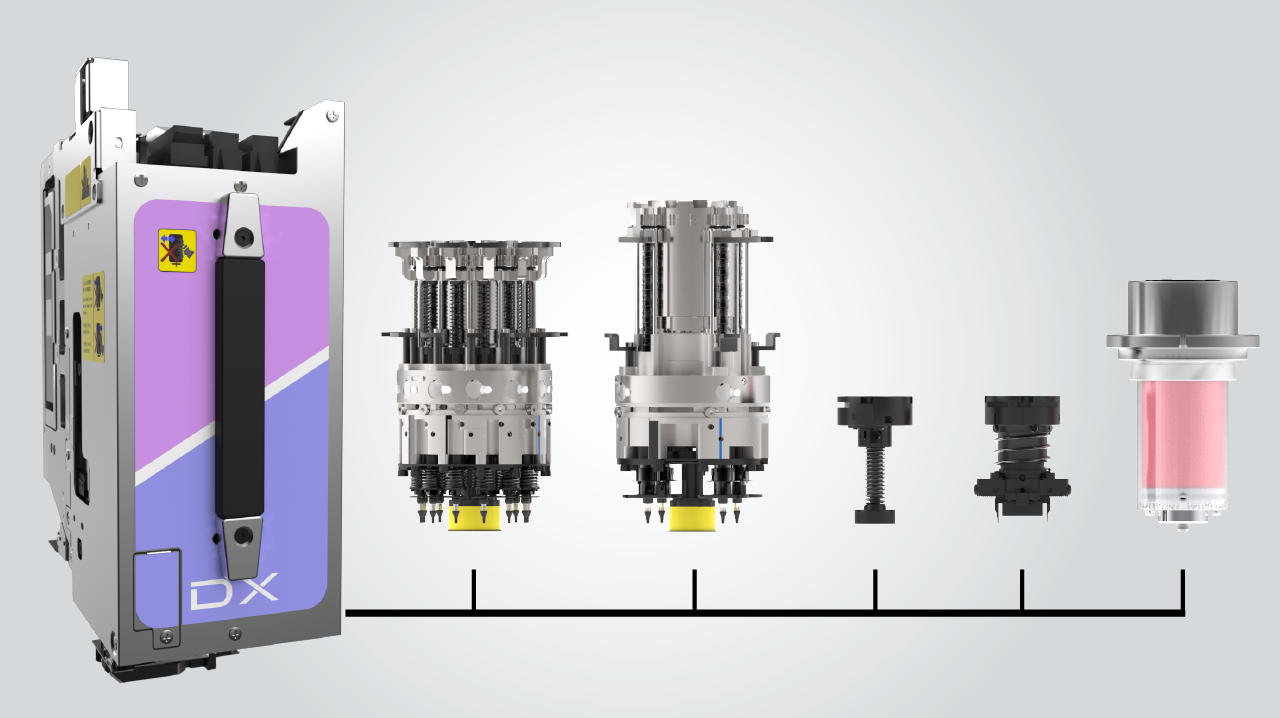
DXヘッドは、チップから大型・異形部品まで、部品サイズに合わせて専用ツールを1アクションで交換します。グルーツールを使用することで、グルー塗布と部品実装を同一モジュールで実現します。
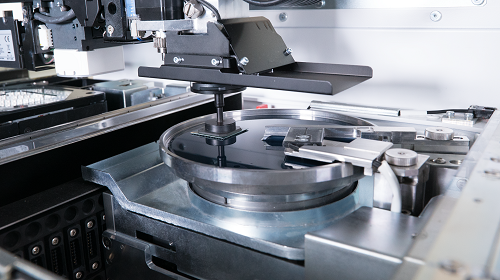
DXヘッドや専用ユニットを搭載するだけで、グルー塗布やフラックス転写のような特殊工程をインライン化できます。仕掛品在庫を削減し、専用機への投資を抑制できます。
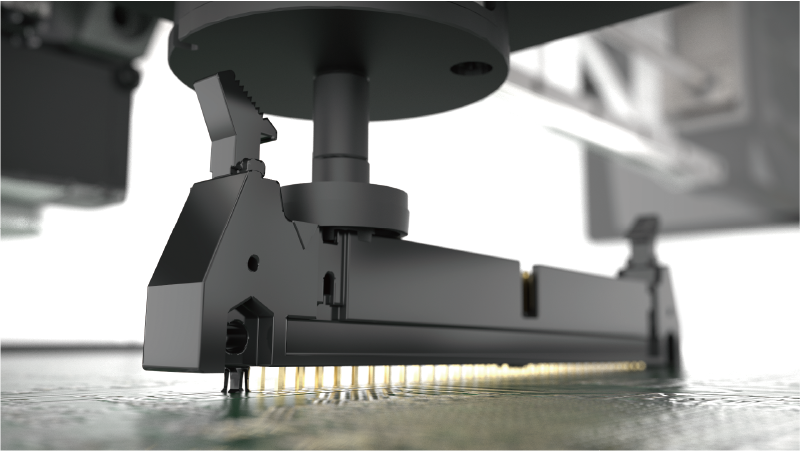
通常部品から大型・異形部品まで幅広く対応するうえ、大型コネクタなどの圧入やクランプ圧をコントロールした部品ハンドリングなど多才な部品実装に対応します。
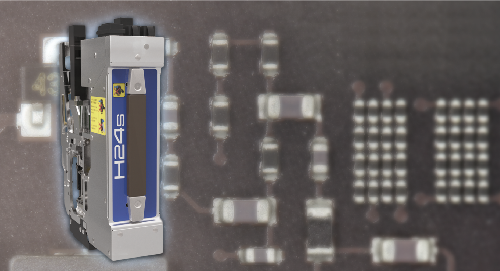
03015部品を±0.025mmの精度で実装するH24Sヘッドを搭載可能です。2ヘッド構成時に最速80,000cphを実現する生産優先モードにも対応しています。
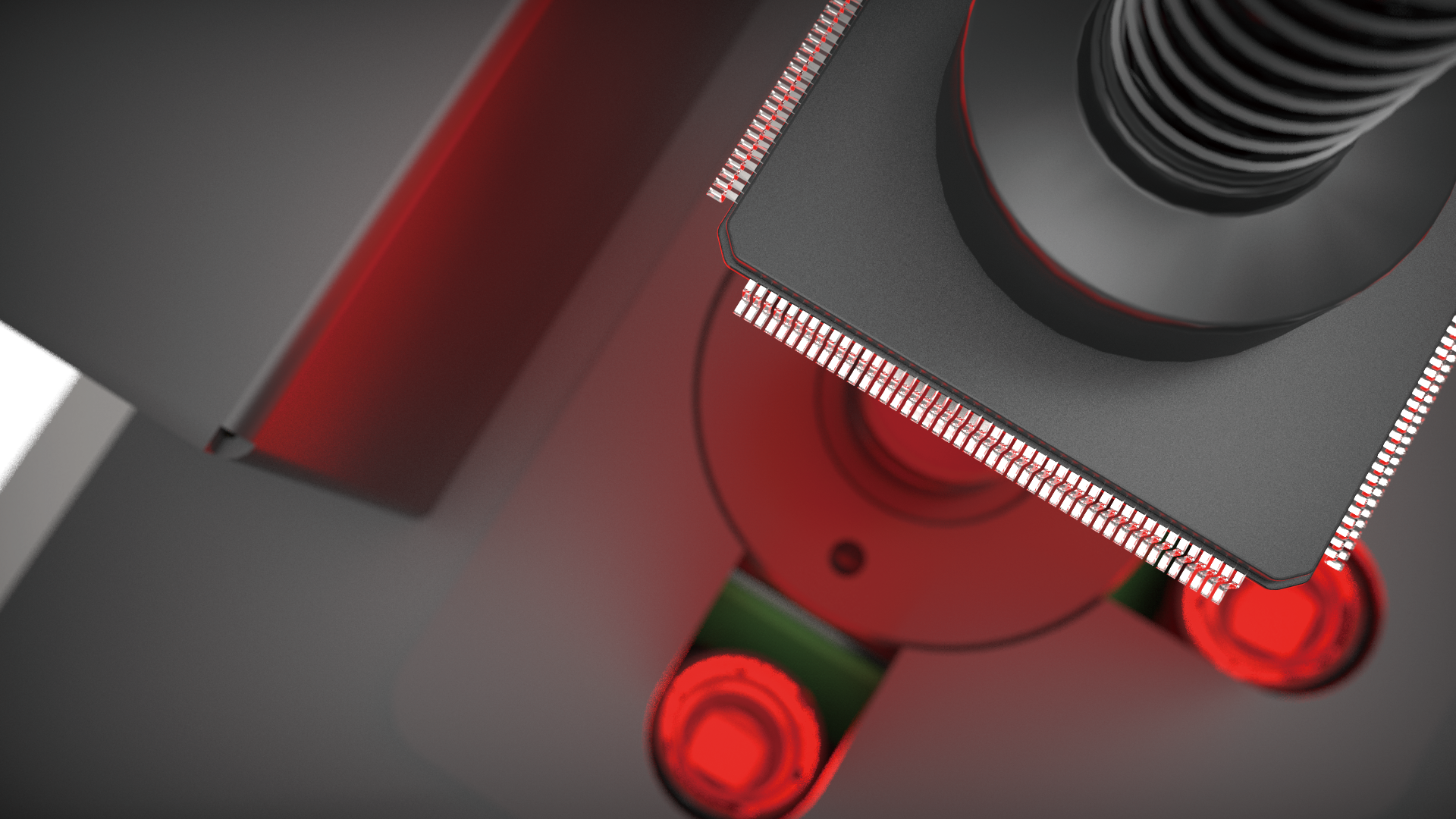
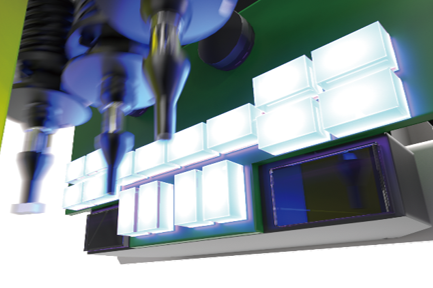
IPS(Intelligent Part Sensor)により、以下のような幅広いチェックが可能です。
・吸着確認および装着後の持ち帰り確認
・部品立ち吸着検知
・部品高さ確認機能
・リード部品の表裏判定
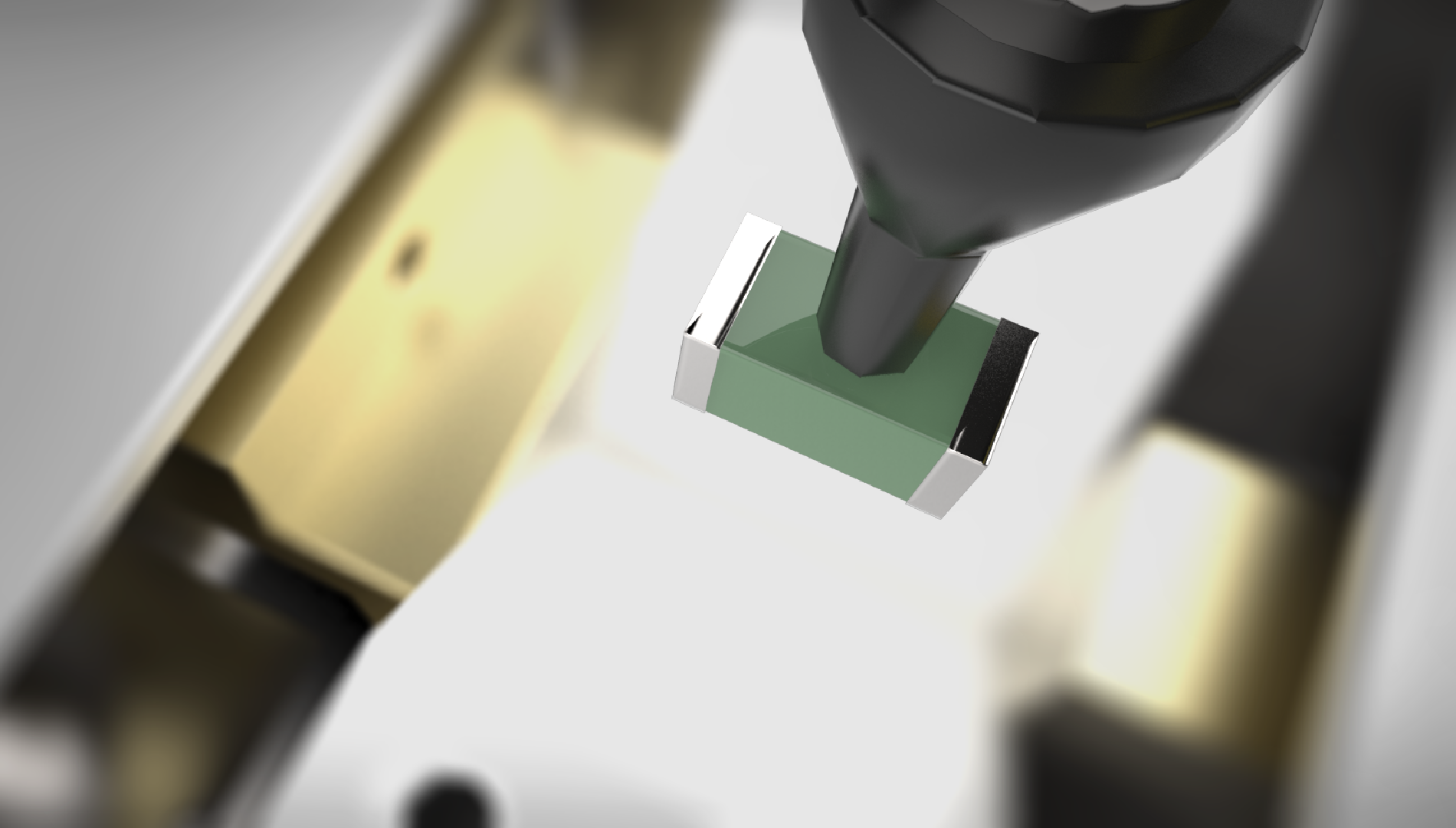
LCRチェックユニットにより、受動部品(L:コイル、C:コンデンサ、R:抵抗)の定数を実装前にチェックできます。それにより、外観検査では検出不可能な誤定数実装が防止できます。
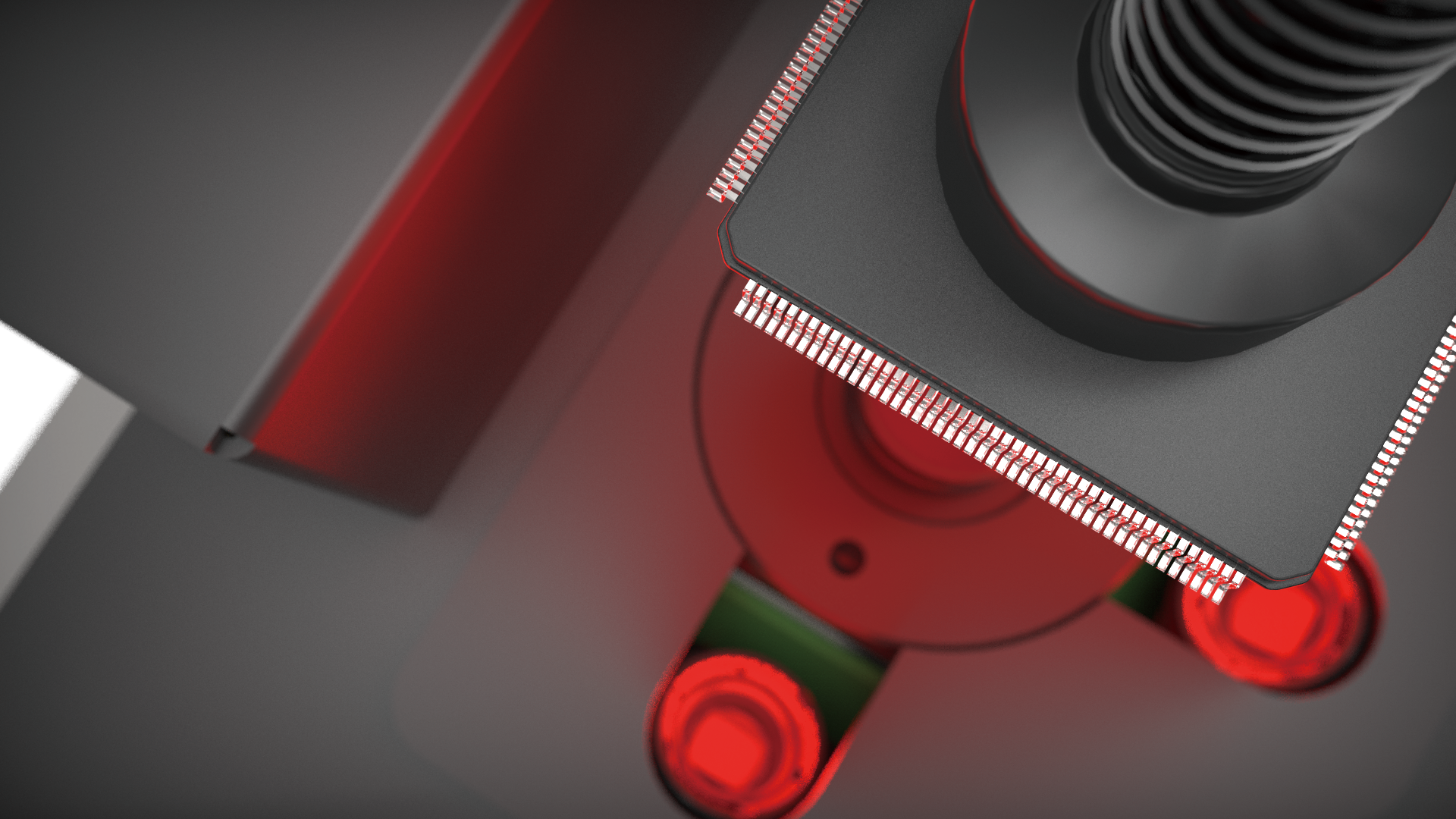
接触不良の原因となるコネクタの端子やICチップのリードの変形を装着前に全数検査して不良部品の使用を防ぎます。装着後では検出できないBGAやCSPのバンプ欠損の確認も可能です。

レーザーセンサーで実装前に基板の反り量を自動測定します。許容範囲内の基板のみを実装するので、不良基板の生産を未然に防止できます。
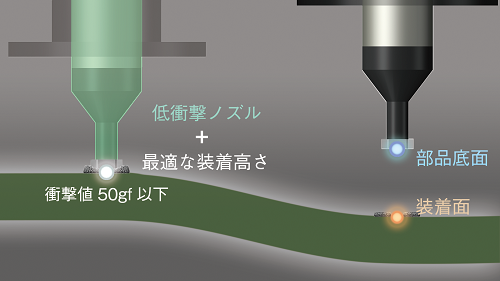
IPSで測定した部品高さを、基板の反り量から得られた装着面に反映することで、押し込みすぎや空中散布を未然に防ぎます。
さらに、独自設計の低衝撃ノズルがはんだ潰れや部品クラックを防止します。
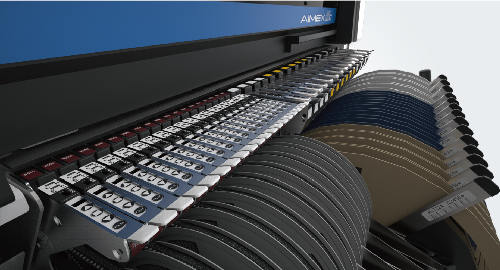
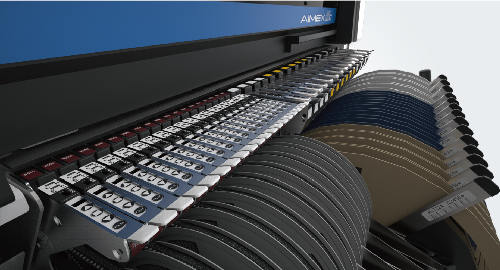
最大130スロットの大容量デバイスを備えており、必要な部品をすべて搭載できます。MFUを一括交換することで、段取り替え時間を最少化します。
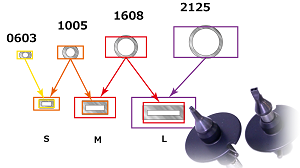
複数サイズのノズル4種( 0603, 1005, 1608, 2125 )を3種( S, M, L )に集約。ノズルを共有化することでノズルの切り替えが削減・サイクルタイムが向上します。
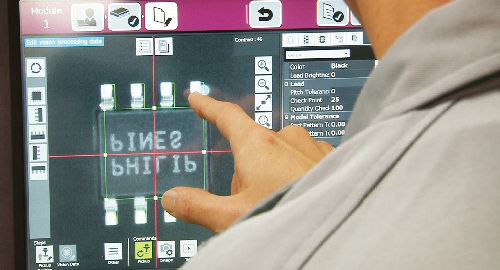
自動データ作成と大型タッチパネルを使った機上編集機能により、新規生産立ち上げのほか、部品やプログラムの急な変更への迅速な対応を支援します。
また、ASG2.0(Auto Shape Generator 2.0)により、これまで自動生成が不可能だった特殊な形状の部品にも対応しました。装置上で部品形状データを更新できる機上ASGにも対応し、調整に要する時間を削減します。