Introduction
The annual amount of data generated by the world's IoT devices is increasing every year. In recent years, the increase pace has been accelerating, driven by the rapid spread of generative AI. The power consumption required for data storage is thus projected to reach approximately 15% of the world's total power generation by 2030.
At the same time, awareness towards environmentally friendly products and services is continuing to grow, underscoring the greater importance of efforts to achieve carbon neutrality in corporate activities.
These trends have extended to the field of electronic panel manufacturing. SMT equipment is now facing strong demand for improvement in productivity while reducing power consumption.
Turning to the product side, more and more electric panels are designed with reduced wiring and space to lower power consumption of electric devices, leading to higher density placements. As a result, it has become more difficult to transfer the right amount of solder in the right shape, and thereby the man-hours required to maintain quality are on the rise.
In addition to this trend, from the perspective of the SDGs, which are closely related to carbon neutrality, functions and automation technologies that can reduce operator workloads have become indispensable.
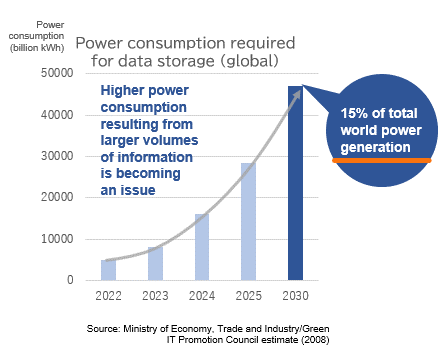
Issues and dilemmas in the solder printing process
To maintain productivity while improving the working environment, it is necessary to reduce losses during production and appropriately distribute the workload, which is not an easy task.
In order to minimize drops in quality and rework losses, it is very important to manage materials such as squeegees and masks, and to be able to adjust print conditions such as those for cleaning. However, as production needs to be ramped up in a short time, these tasks often rely on experienced operators with know-how, resulting in a greater workload on them.
Once production has started, it is necessary to ensure that the solder amount and roll shape are appropriately maintained and the set conditions are functioning as expected to maintain quality. During changeover, it is also necessary to prevent solder from falling off the squeegee and foreign matter from entering the solder.
To improve productivity, machine downtime must be reduced to increase the operating rate. Factors that cause the operation rate to drop, excluding unexpected ones, include machine stops to replace consumable materials such as paper and solder during production, preparation for ramping up new models, and changeover. The key to improving the operating rate is how to reduce these downtimes.
Another barrier to solving these issues is the labor shortage and rising labor costs in recent years, making it difficult to secure sufficient personnel at production sites around the world.
As a solution to these issues, we propose "automation" of the printing process.
Automating tasks that are performed manually can be effective in a variety of aspects, such as distributing the workload that is disproportionately allocated to specific operators and reducing error stops caused by human errors. This allows for high productivity even with fewer personnel.
More information on automating the solder printing process is available in the following reference webinar. (Approx. 16 minutes)
Reference webinar
Solder printing today becomes more difficult the greater the part density is on electronic panels, and a high level of management is required.
However, the results can vary greatly depending on the environment inside the machine. Solder printing quality often relies on the know-how of the operator, and it is a difficult process to standardize.
This seminar focuses on issues that stem from operator-dependent tasks in solder printing, and introduces ways that automation can resolve these.
Webinar summary
1. Challenges at production sites
Organizes the requirements for printing equipment from the perspective of achieving carbon neutrality and the SDGs.
2. Issues faced during normal production and how to solve them
Provides solutions to issues arising from consumable part replacement and changeover.
3. Issues when setting up new models and how to solve them
Introduces solutions for preparation work that often relies on the skill and experience of the operator.
4. Issues when performing changeover and how to solve them
Presents solutions to reduce the workload and man-hours required for changeover work.
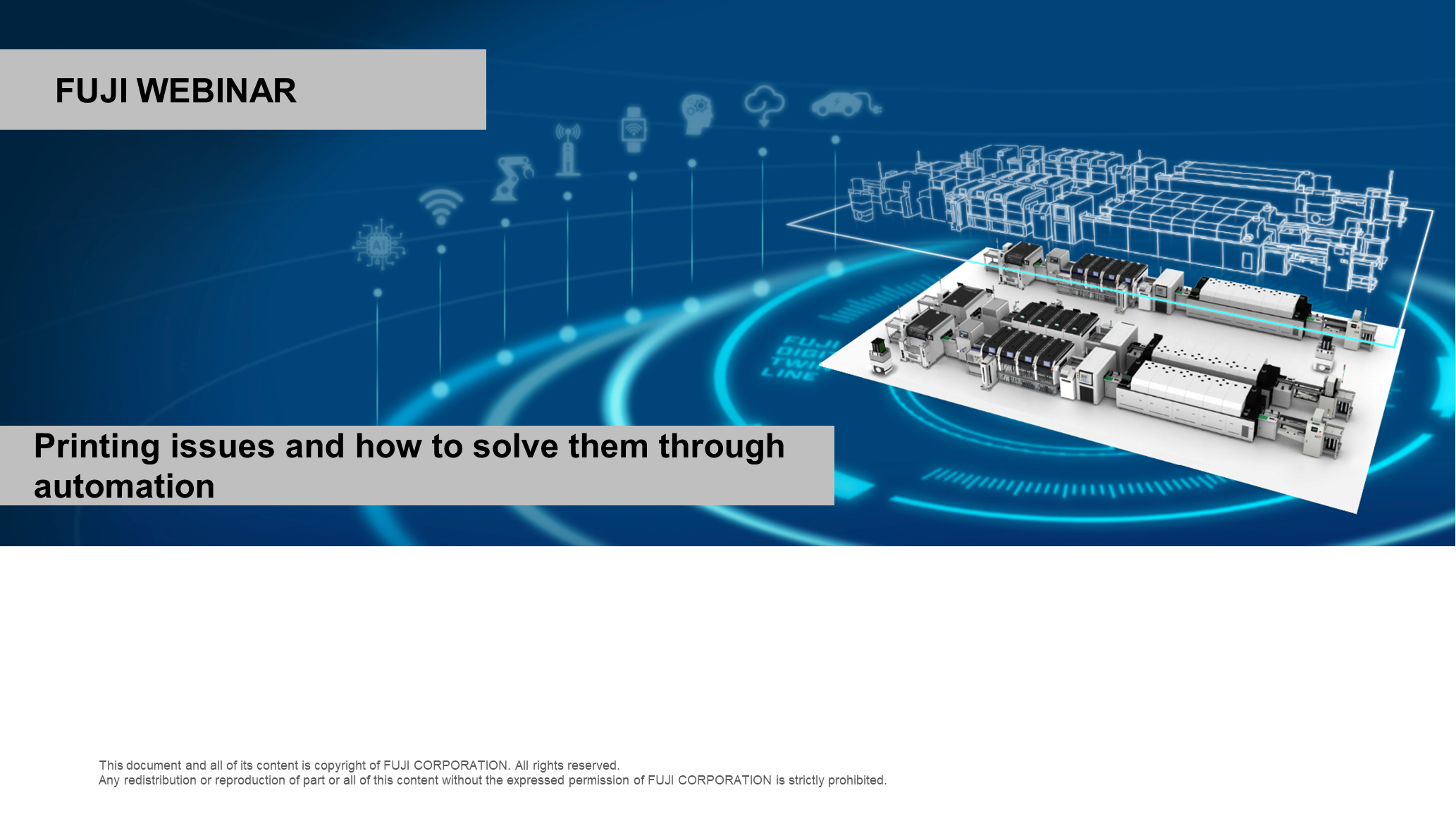
Note that Fuji SMT site membership is required to view webinars or download catalogs.