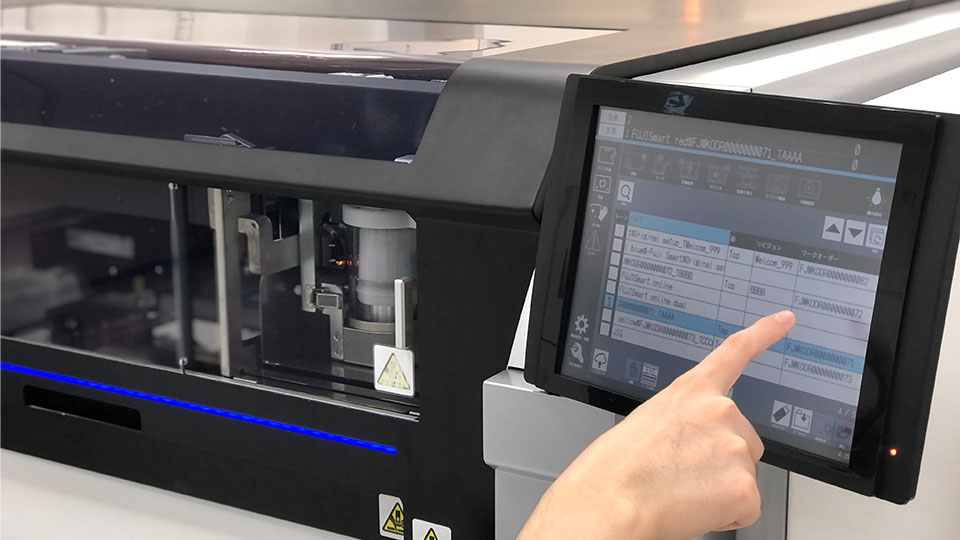
New model ramp-up time reduced by 57% Printing navigator
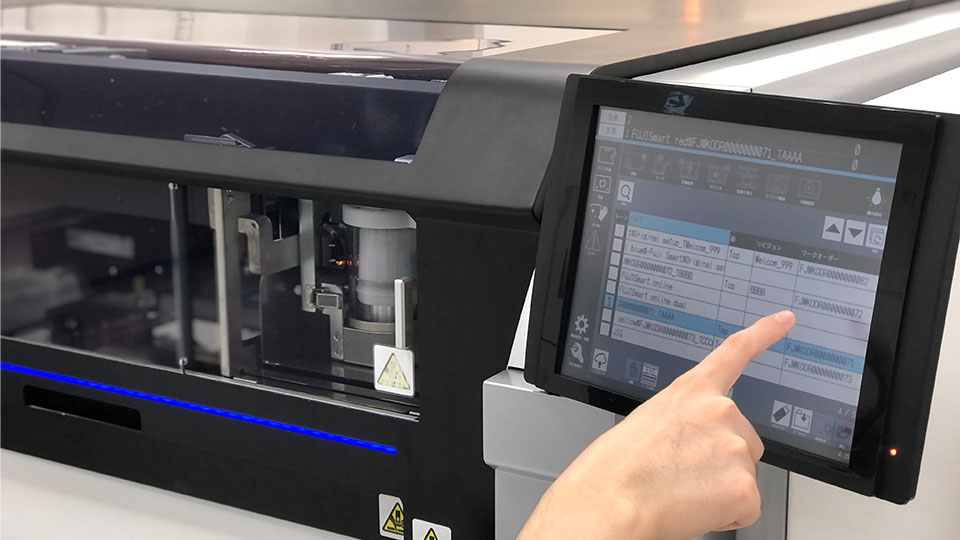
Ramping up a new model involves a time-consuming process of determining the right printing conditions to use, which largely depends on individual operator skills. Furthermore, the fact that the result cannot be known until actual printing makes it even more difficult.
Even after trial production with the right printing conditions is successfully performed and it comes time to go into full production, the printing conditions may need to be fine-tuned if the first pass yield at the SPI is poor and the quality is not stable, resulting in additional time spent.
Fuji has a solution to this challenge with its printing navigator, making it more efficient to set printing conditions, which currently depends on operator skills.
With the printing navigator, recommend parameters based on the accumulated data and quality data calculated from the first pass yield are presented, simply by entering printing conditions.
In addition, inspection results are automatically accumulated through SPI linkage. The more that gets registered to the system, the more it will evolve into a database that matches your needs, and more practical printing conditions can be provided.
Through this, printing conditions (parameters) can be determined while comparing quality data and cycle times, without relying on the operator's intuition. When performed under conditions at Fuji, this system reduced the startup time by 57%.
1. Setting parameters
2. Optimal print conditions are searched for based on past results, and parameters linked to inspection results are displayed
3. Comparing results against desired conditions
Enter the parameters such as the metal stencil thickness or solder particle diameter.
Entered information
Panel information, metal stencil information, solder information, squeegee information
Desired production conditions
Cycle time, transfer volume, important quality items
Parameter input screen
The system extracts data close to the ideal print quality from the past results database and displays recommended parameters. Up to 10 patterns of recommended parameters are displayed, from which the optimal parameter can be selected.
Top 10 conditions for high quality scores output screen
Compare the displayed results with the desired production conditions and determine the printing parameters. Printing quality can be checked without actual printing, making printing condition setting more efficient.
<Applicable machines>
NXTR PM V1.00 or later
GPX-CII, GPX-CSII V1.50 or later Note: The screens and operation methods are different.
We hope that the information presented for the printing navigator has been satisfactory.
This printing navigator, which enables ramp-up of new models without relying on the operators' skills and intuition, helps to reduce preparation time in the printing process. Using the printing navigator is recommended when wanting to reduce preparation time.
Fuji’s printers are also equipped with many other functions that are useful for production, such as functions to maintain quality and to improve the efficiency of changeover work.
If you would like to know more about this product, feel free to contact us.