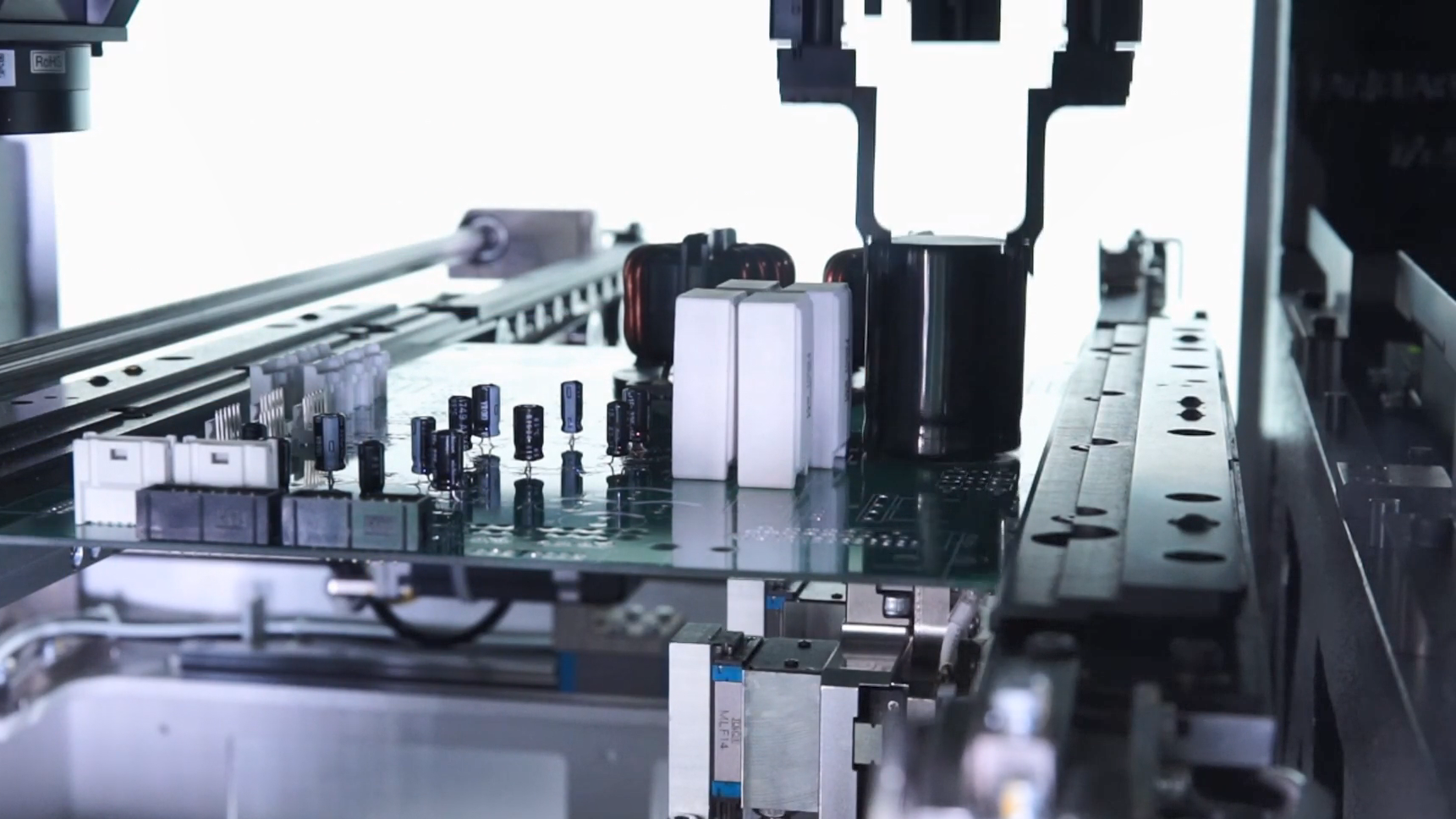
Road to automating insertion processes – Key points to success and Fuji solutions –
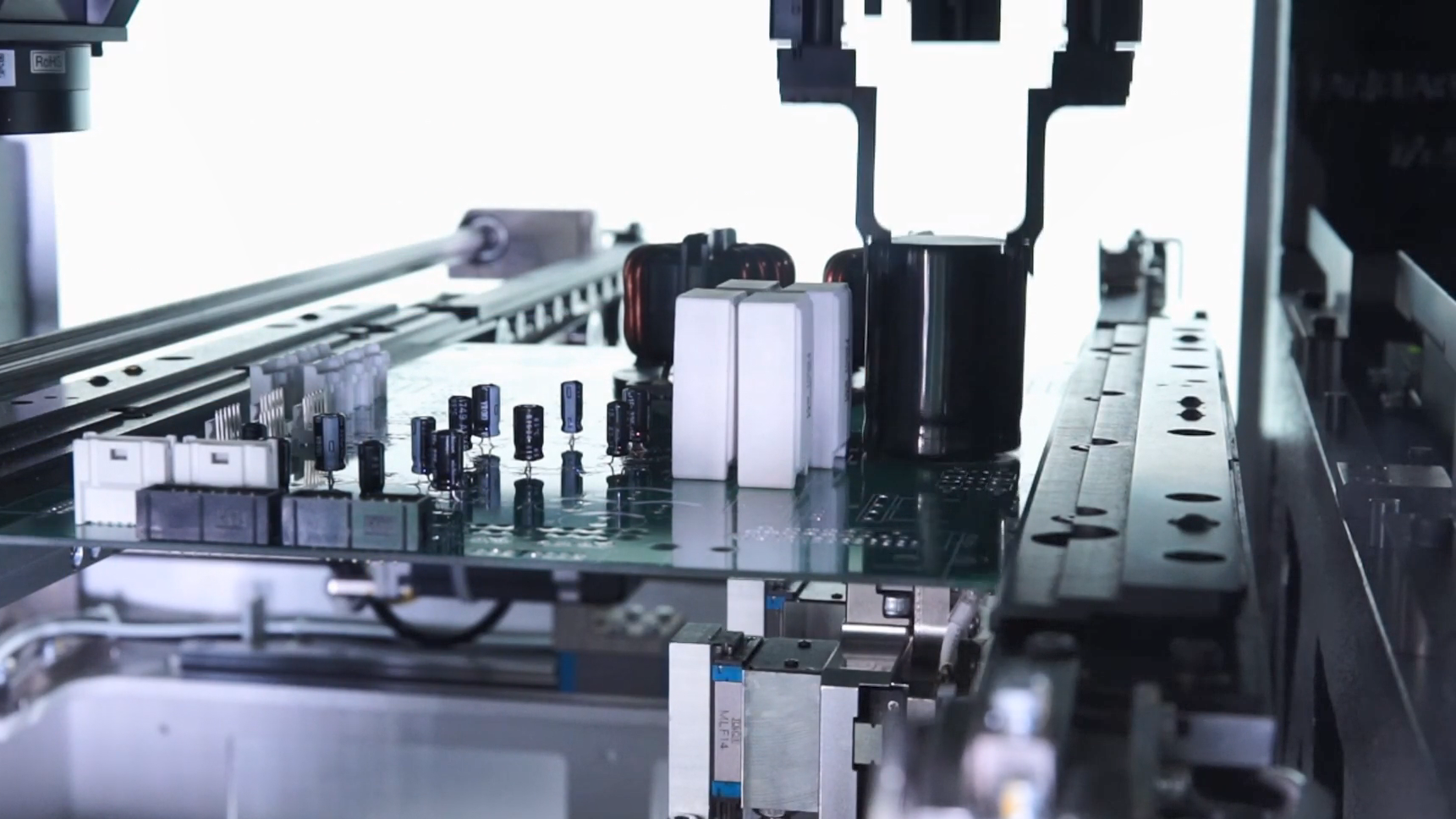
In recent years, robots have been introduced into various fields worldwide. This introduction was accelerated by the need for robots driven by the Covid-19 outbreak from 2020 onwards. In the manufacturing sector, the shipped value of goods in 2025 is expected to more than double that of 2020. Among these, surface mounting technology (SMT) related business has been particularly strong against the backdrop of IT investment and the electrification of automobiles, leading to increased investment not only in line expansion but also in the automation of manual insertion processes that still remain after the SMT stage.
In addition to the desire to improve quality and productivity, the reasons for increased investment in automation solutions for manual insertion work include human-resourcing issues such as chronic labor shortages and soaring labor costs, and risk management in response to unpredictable and sudden changes in market conditions.
With this article we aim to provide companies that are looking to introduce automatic insertion machines and individuals who would like to know more about the automation of manual insertion processes with information concerning the latest robotics and current trends for insertion machines. We also provide check points from the point of view of a robotics manufacturer that should be covered when looking to select the right automatic insertion equipment.
The insertion machines that are currently used in SMT processes can be broadly classified into two types; linear XY robots and multijoint robots.
The advantages and disadvantages of each are as follows.
Type | Advantage | Disadvantage |
---|---|---|
Linear XY robot | High positioning accuracy Ease of changeover |
Large installation area Less suited to complex operations |
Multijoint robot | High degree of freedom of movement and can be used in a variety of processes | Incurs costs when starting up or relocating The positional accuracy is lower than that of an XY robot |
In the panel assembly process, linear XY robot-type insertion machines are the mainstream because their operation method is similar to that of SMT machines (pick and place machines), and they offer high speed, high precision, and ease of setup.
Careful consideration is taken when planning to use robots to automate tasks that were previously performed manually such as manual insertion, to make sure that clear benefits will be gained. This often results in hesitancy to introduce automation solutions.
When we asked our customers who have inquired about automatic insertion machines what their concerns were in introducing them, we found that they fell into three main categories.
Points of concern when introducing automatic insertion machines
1. Maintenance and management
Whether the equipment can be used effectively when no one has specialist knowledge on automation machines and there is no specialist department at the company
2. Automation rates
Whether only a set type of parts is applicable for automation, and whether automation is possible for specialized odd-form parts
3. Versatility
The ease and cost of changing handled parts or relocating equipment
With high-mix production becoming the norm, it is natural to be concerned about the scope and versatility within the range of what can be automated. This is an even greater concern for production that requires specialist jigs or uses specialist parts.
Automatic insertion machines come under the umbrella of production robots. Robot technology has evolved remarkably in recent years, and performance has greatly improved compared to a few years ago. With that in mind, just how far can contemporary automatic insertion machines go to alleviate these concerns. Here we would like to present a few examples using Fuji products.
Equipment installation is performed by engineers dispatched by the manufacturer. When setting up multijoint robots, qualified SIers, or system integrators, spend several days performing setup work for movement settings and starting production, which may give the impression that it is difficult to change processes or relocate the equipment.
Once purchased, equipment is to be used over a long period of time. To ensure that the equipment can be used for a long time, it is imperative that customers are able to start production, and create and edit production programs on their own.
Both types of automatic insertion machines offered by Fuji, the linear XY robot type and SCARA robot can be programmed by specifying coordinates, making it possible for customers to create and edit their own production programs. We also have support systems in place including training and online learning systems for customers that are introducing robots for the first time.
If, despite purchasing a robot for automation, the parts applicable for automation are limited, it will not be possible to achieve the desired result in terms of productivity and quality. Reasons automation may be difficult include parts that are supplied in packaging that cannot be supplied to automated machines as is, or part forms that are difficult to handle.
For example, parts that are delivered arranged in trays with a lot of play in the cavities or parts that are delivered loose in a bag. Usually, to automate insertion of these parts, it is necessary to transfer them to special trays or sticks.
Our lineup of insertion machines can handle a wide range of packaging, part shapes, and sizes through utilization of well-rounded supply units, handling tools, and image recognition systems, achieving a high rate of automation.
Recent products are being built to produce using multiple types of parts using one robot or one production line. However, that is not enough to make a product something that can be used long-term. The life cycles of electronic devices are becoming shorter, and there is more scope for line configuration changes and equipment relocations than in the past. Because of this, many customers have expressed concern about the cost of having engineers dispatched on a case-by-case basis. If their own staff could easily change product models and line configurations, these concerns would surely be alleviated.
In addition to their ease of changeover, our insertion machines are designed so that customers can relocate and start up the equipment themselves, meaning that there are no headaches resulting from ongoing costs after purchase.
Work required from engineers for standard robots
Here we will explain the check points to cover in order to avoid automation failures for manual insertion processes, using the key words "automation rates" and "versatility," which are the aspects customers are most concerned about, and "production quality," which customers who are considering automation expect.
■ Automation rates
• Coverage of supply units
Insertion parts not only come in packages such as tape, trays, and sticks that are designed with the intention of being supplied to automated machines, but are also supplied in packages that are intended to be handled manually, such as trays with a large degree of play in the cavities and loose supplied parts, as described above. To achieve a high automation rate, check to see what type of packaging will be used and up to what size the available supply units are capable of handling.
• Coverage of handling tools
Handling tools are just as important as supply units for increasing the rate of automation. The insertion process often involves odd-shaped parts and large, heavy parts that cannot be picked up and retained by nozzles. In addition to the size and weight of parts that can be handled using standard tools, check the availability of custom tools that cannot be found in catalogs and examples of their usage.
• Image recognition system performance
The performance of image recognitions systems differs depending on the manufacturer. Check the strong and weak points of each, and the part sizes that can be supported. If possible, we recommend that you ask the manufacturer to test automation for the target parts using actual equipment before purchasing.
■ Versatility
• Ease of changeover
The versatility and ease of exchange of the handling tool itself is an important point that impacts the operation rate of the machine and the amount of work required for changeover.
The method used to exchange handling tools and units loaded into insertion machines varies greatly depending on the robot type. The actual workability is hard to judge without actually operating the equipment. We recommend visiting the manufacturer's showroom or factory and check operation on the actual equipment.
• Workability and costs when relocating equipment and changing processes
When selecting an insertion machine, it is important to factor in workability and costs for relocation or process changes.
If a qualified person from the manufacturer or service agent needs to be dispatched to relocate equipment or make changes to processes, a fee will likely be incurred each time. When selecting an insertion machine, it is advisable to consider not only the initial investment but also the costs required after purchase.
■ Production quality
• Availability of a quality check system
Surely what customers considering automation expect most is an improvement in quality.
Insertion pins that protrude beyond the exterior of the part may have pitches outside the specifications, deformation, or missing leads due to external shocks during transportation. Under automatic operation, a quality check system that prevents the use of such substandard parts is essential. It is also important to have functions that can confirm whether a part has been inserted correctly, and that can prevent inserted parts from falling over or coming out of the panel.
• Visualization system
Unexpected problems are bound to occur with machinery. The availability of a system that makes it possible to visualize error statuses and progress is important in terms of how much work is required for management. Check whether there are any indicators that are necessary for your company's performance management and, if necessary, check whether they can be linked to existing management systems.
There is one thing you should be aware of when checking using the three keywords listed here of automation rates, versatility, and production quality. That is, in addition to improving the efficiency and quality of current production, it is important to cast your mind toward the future to consider how the products being made by your company may change in comparison to now. You may be able to get some insights from the technology trends being discussed in trade publications or from business meetings with suppliers.
Let's take a look at the main two types of insertion machines in Fuji's lineup.
■ Linear XY robot insertion machine - sFAB
• This machine is suitable for production using many part types, and that requires both speed and accuracy.
This machine has improved on the part handling capability that can be a weak point for linear robots, and is capable of handling parts up to 200 x 200 mm, with a maximum weight of 200 g. Various supply units and handling tools are used in combination to achieve high-speed, high-accuracy insertion and highly versatile production.
■ SCARA robot insertion machine - SmartWing BA
• Optimal for automation for two or three part types, and for use as a complimentary machine for a linear XY robot
SmartWing BA is a panel assembly robot cell that packages a conveyor, cover, and two cameras together with a SCARA robot. Because this is a packaged solution, the need for system integration work after purchase is reduced.
Unlike standard multijoint robots, motion settings can be programmed using the same coordinate input method as SMT machines (pick and place machines), rather than having to use robot teaching. This allows a company to relocate equipment and change processes on their own, thereby reducing SIer dispatch costs that incur after purchase.
It can be nerve-wracking to introduce new equipment. In particular, customers who have tried automation in the past but found it to be ineffective may not be willing to go ahead with any further automation, despite having an obvious need. We would like to invite such customers in particular to come and talk with us. With our robot technology that has evolved significantly over the last few years and a comprehensive support system, we are confident that we can provide you with optimal automation solutions for your production.
We also accept requests for automatic insertion viability tests.
If you provide us with the parts and panels you are considering for automation, we will confirm whether or not automatic insertion is possible in line with your requirements.
Contact your Fuji representative for details.