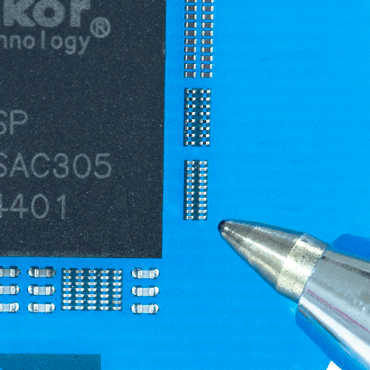
Solutions for issues in high density placement – Introducing the placement height adjustment function
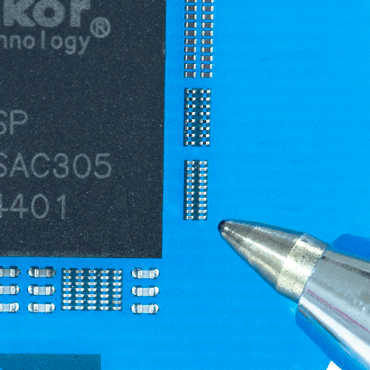
The annual amount of data generated by the world's IoT devices is increasing every year, and the accompanying electricity consumption for data storage is expected to reach about 15% of the world's total electricity generation by 2030.
Meanwhile, energy saving is an important issue for achieving SDGs and carbon neutrality and there is demand for smaller and higher-density panels that are used in all electronic devices, from mobile devices to automotive electronics, communication infrastructure, and servers.
To achieve this, stable placement quality must be maintained in production using panels designed for space saving and economical wiring.
This article introduces the placement height adjustment function, one of the solutions available for resolving issues in high density placement.
The following are typical quality issues found in high density placement.
The occurrence of solder bridges due to excess load during placement
Achieves high-quality placements by detecting whether the part has contacted the panel using the contact check sensor on the placement head.
The sensor detects that the part has contacted the panel
The following improvements can be obtained by using this function.
Using panel height adjustment reduces stress on parts that are susceptible to impact load when placing parts such as thin parts. It also prevents solder from collapsing.
Reducing placement load on upward warped panels
Preventing solder from collapsing
If excess vibration is applied to less rigid panels such as thin panels and multi-board panels, placed parts around the placement section will be deviated or the placement position for the part to be placed next will deviated.
Using placement height adjustment reduces vibration on panels caused by pushing too hard on parts.
Mid-air placements are prevented by releasing parts after detecting that the part has contacted the panel for downward warped panels.
Mid-air placements that occur when the panel is warped downward
The part height is measured using the intelligent parts sensor (IPS) and the placement height is then optimized based on this measurement. Then, by calculating the panel warpage with the placement height adjustment function using the contact check sensor and controlling the placement height according to the trend, it is possible to achieve high speed, low stress, and reliable placement.
Part height measurement using the intelligent parts sensor
Machine type | NXTR A model, NXTR S model |
---|---|
Head type | RH20, RH08, RH02, and RH01 |
Note: The part height check function using the intelligent parts sensor (IPS) is supported by RH28, RH20, and RH08 heads.
In addition to this, we also provide automatic maintenance units that prevent adverse changes in equipment caused by insufficient maintenance, advanced maintenance software solutions in Nexim, and a panel height detection function that measures the panel warpage before placement.
Please contact us if you have any further questions about these or any other solutions.