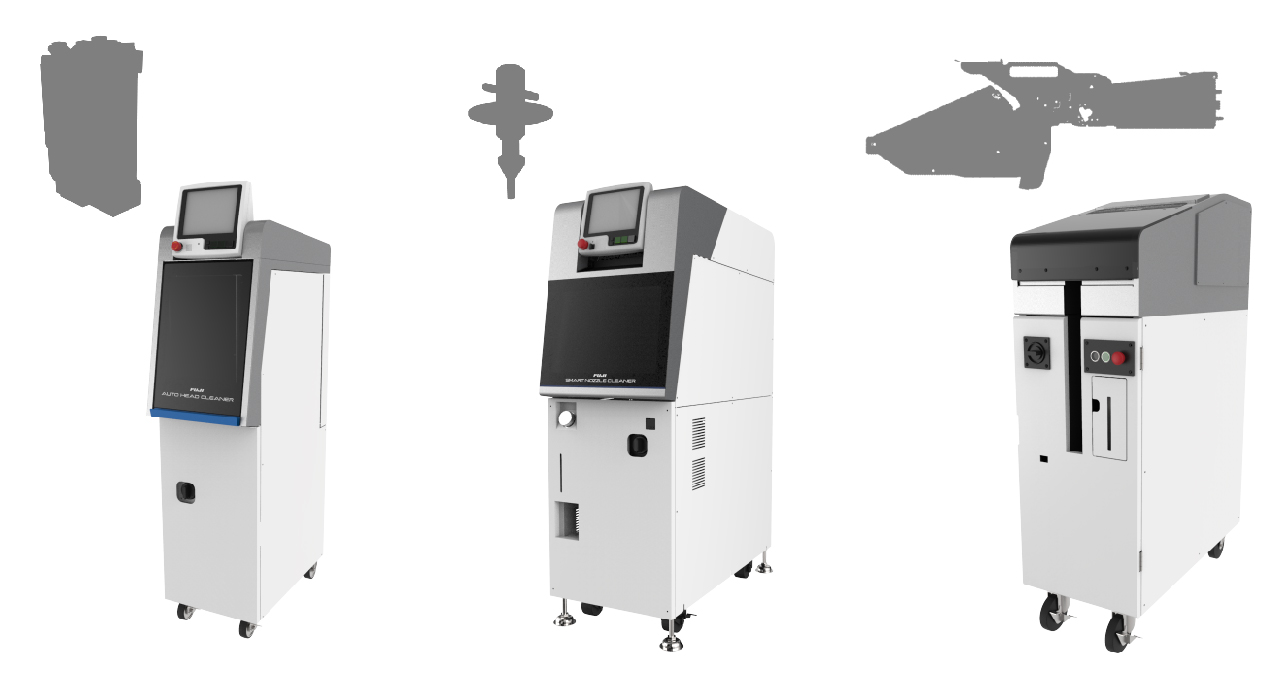
Preventing drops in machine performance
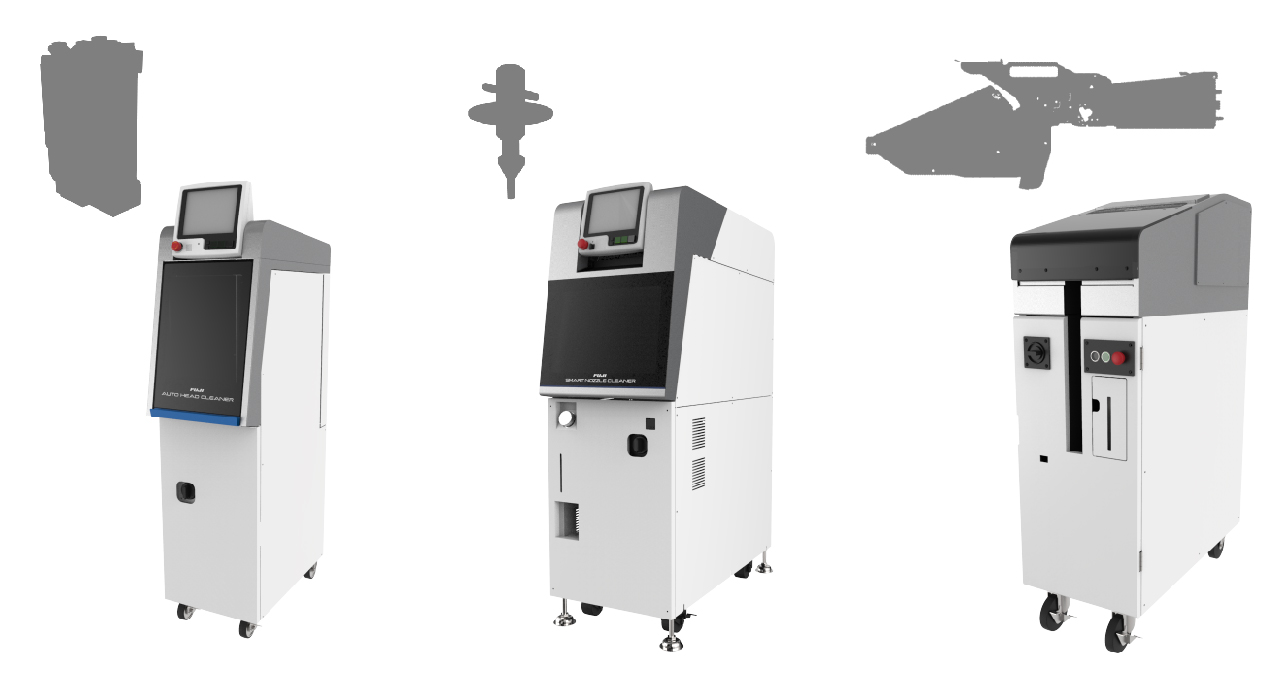
Pickup errors and contact issues may occur in association with adherence of solder paste and dust from the panels and carrier tape. To avoid any loss of production from these factors, it is necessary to keep the feeders, nozzles, and heads that are directly related to picking up and placing parts in top condition. The following introduces functions and units to cover this objective.
Nozzles contact directly with parts, so the condition of a nozzle directly affects placement quality and productivity.
This suggests that it is necessary to have a system that ensures always using nozzles that are in good condition to maintain high quality production.
Nozzle statistical error
Production keeps running while replacing nozzles with substitute nozzles when they reach thresholds according to the error statistics of nozzles.
Periodic nozzle exchange
Production keeps running while replacing nozzles automatically with substitute nozzles when they reach the specified usage count or the usage limit in terms of the quantity of produced panels.
Periodic nozzle blow
When nozzles reach the specified usage count or the usage limit in terms of the quantity of produced panels, the inside of the nozzles is blown to prevent pickup defects due to clogging.
Nozzle cleaning
Nozzles set on the head are cleaned using a blush at set intervals during production.
This application has two types to choose from: Nozzle station type and feeder type.
High-hardness nozzles
Nozzles undergo nozzle evaluation testing, which validates our nozzles to ensure that there is no deformation and nozzle chipping after 20,000,000 placements.
They can be used reliably for a long time.
Fuji's placement machines feature easy, toolless compositions for exchanging heads and other units. Even when it comes to maintenance, production still can continue with substitute units, and in the meantime maintenance is performed offline. This minimizes production downtime due to maintenance.
In addition, by operating in coordination with the system, it is possible to digitize work results and visualize the unit statuses, which is essential for realizing a digital factory.
This unit cleans dust deposits and old lubricant from inside feeders, then automatically applies fresh lubricant.
The unit then inspects the torque of the gear sections and tape indexing accuracy, and automatically corrects the tape indexing accuracy if necessary.
Result using the Auto Feeder Maintenance Unit
The nozzle stations that supply nozzles in Fuji SMT machines can be taken from the machine and placed directly into the Smart Nozzle Cleaner.
Since nozzles do not have to be moved one-by-one, nozzle maintenance is simple and smooth. After the maintenance, a blow drier is used to clear moisture from cleaned nozzles and functional testing is performed.
The unit also doubles as a nozzle stocker, with the capacity to store up to 1,140 nozzles.
Result using the Smart Nozzle Cleaner
This unit cleans the air channels inside Fuji heads. There are two menus to select from; air cleaning or oil cleaning, depending on the type of cleaning required.
After maintenance, the unit checks air flow and checks whether each motor and the sensor sections are working in sync.
Result using the Auto Head Cleaner
This software is a tool for supporting feeder, nozzle, and head maintenance.
Units are identified by unique IDs and data such as the pickup rates and usage time for units is collected and managed by their ID. Once a unit has reached a predetermined threshold for conditions, it is flagged for maintenance.
Just by performing maintenance according to guidance screens, units can be kept in good condition all the time, which prevents trouble associated with equipment.