1. 前言
在实现超级智能社会的途中,随着各国相继提出更先端的数字技术,打破了电路板上搭载元件的传统定义。
例如,利用互联网观看视频以及联网打游戏普及后,通信的数据量随之增加。为了能够高速处理大量数据,通信基础设施中使用的CPU等高性能设备随着能力的提高而越来越大型化。另外,在环境问题被高度重视的当下,更加环保的电动汽车发展势头迅猛,电池上使用的大电流接插件也变得越来越大。
在这篇文章中,我们会介绍在贴装高性能元件以及连接器等大型元件时遇到课题以及FUJI对此提供的解决方案。
贴装大型元件的课题
从复杂的元件形状及机器的规格限制方面例举了以下的课题。
- 创建影像处理数据费时
- 带脚元件定位困难
- 手工操作导致品质不稳
正如“大型异型元件”的字面所示,大型元件通常都是些形状复杂或者具备某种特征的元件,贴装它们的方法也需因物而异。
接下来我们就按照以下的项目逐个介绍FUJI为大家提供的解决方案。
2. 创建复杂影像处理数据时的强大支援能力
如果设置的影像处理数据不合适,则会因位置偏移或元件识别错误等问题而停机,进而造成时间损失。此外,市场需求的多样化导致生产品种日益增加,创建全新生产程序的作业量也随之增加,这就更要求作业员在短时间内创建出正确的数据。
然而,大型元件的贴装表面大都带有引脚或锡球,特别在创建一些端子排列不规则元件的影像处理数据时,单创建1个元件的数据可能就要花费10分钟以上的时间。
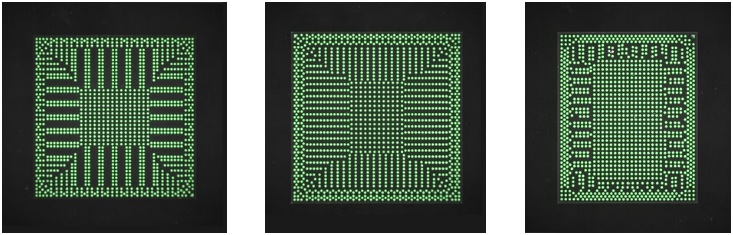
锡球不规则排列的BGA
我们即便在面对创建影像处理数据时需要花费大量时间的元件,也可以通过利用实际的元件影像在短时间内创建出正确的数据。
2-1. 影像处理数据的创建支援软件
ASG这款设备可利用人工智能自动识别并设置在创建影像处理数据中最耗时的引脚跟锡球,将作业工时加少到1/3以下※1。
此外,使用它可以自动选择影像处理的Vision Type(影像处理数据类型),并离线完成识别的测试,可减少生产开始后的影像识别报错率,缩短大规模生产前的准备时间。
对于单边长度超过50mm的大型元件,通过分割拍摄的方式多次采集影像,也能够跟小型元件一样,在短时间内得到正确的影像处理数据。
※1 本公司的调查结果
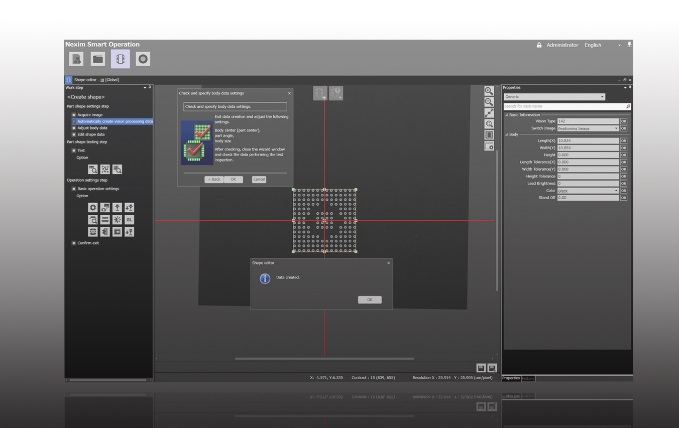
影像数据创建界面
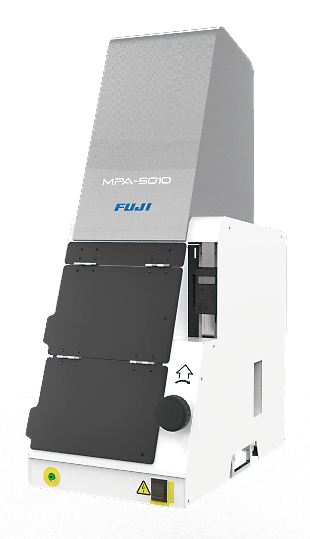
专用离线影像处理相机单元
某些元件在不同的生产批次之间存有很大的个体差异,在物料批次更换时有可能发生影像处理错误。面对这种情况,我们将使用贴片机上的相机所拍摄的影像,在机器上或者生产线服务器上编辑数据,让生产快速得到重启,从而使停线时间降至最小。
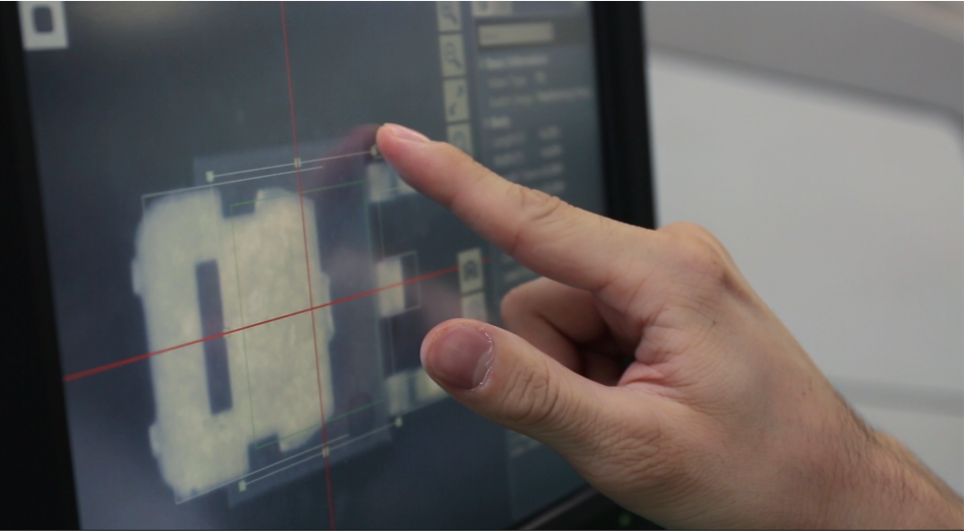
机上编辑示意图 AIMEXIII
3. 提供各种元件不同特征的最佳解决方案
为了能高品质高效率生产大型元件而有必要针对每种元件的特征(外形、尺寸、重量)做出对策。
在这里,我们例举了常见大型元件的特点和课题,并提出了针对这些元件的解决方案。
3-1. 正确定位带脚元件
大型元件贴装困难的原因之一是因为元件上有插脚。
因为这样的元件需要将插脚准确地插入电路板上的通孔中,所以除了元件的外形,还需要正确识别插脚的前端影像。然而,根据切割方法以及处理方法的不同,插脚的形状并不统一,所以正确识别插脚中心十分困难。
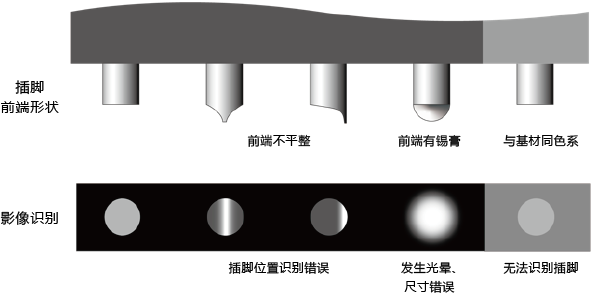
插脚的前端形状与影像识别结果的对照图
要想避免插脚前端形状差异导致的识别错误,防止插入不良,必须配备能正确识别插脚前端影像的相机与照明方式。
侧光相机利用激光照射插脚的前端,是一种能清晰识别前端影像的有效方法,它可以捕捉到各式各样前端形状的插脚中心并准确进行定位,防止插入不良。
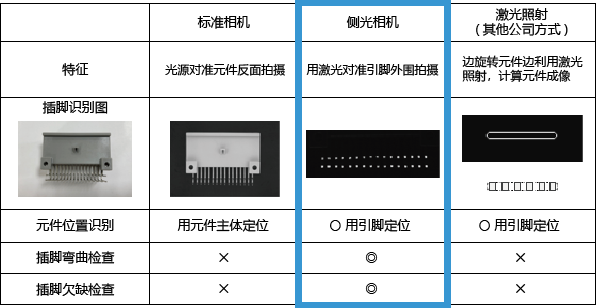
影像处理方式与插脚查看方法的对照
3-2. 可靠贴装带压针的元件
部分大型元件上会附带插脚来防止它们在移动过程中翻到、脱落或者在二次融化时浮起。在插装这些元件时会先对准1点施加压力将插脚部分压入电路板的插孔中,这种能确保大型元件插装稳定性的工作叫做压装功能。
万一被异物或元件等卡住而无法将插脚完全压入电路板内时,元件便会作为不良品被筛选出来。
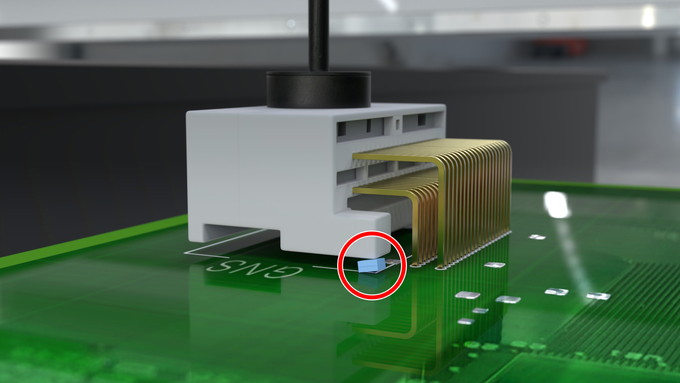
检测出压入错误
适用工作头: DX工作头(S1)、H01工作头、H01V工作头、H02工作头、H02F工作头、OF工作头
适用范围: 98N
同样是需要借助外力压入的元件,对于那些元件本身硬度不足及屏蔽盖等稍加用力就会导致变形的元件而言,还可以选择另一种元件压入功能。这种功能是在贴装元件后,从多个点向元件施加压力,能边控制元件的受力负担边将元件完全压入电路板。
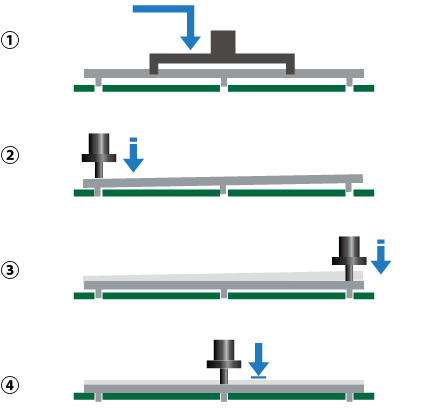
元件压入功能示意图
3-3. 支持高元件贴装
近几年的贴片机在X方向与Y方向大都具备了处理大型元件的能力,但是对于高度,因为机械构造的限制,普通的贴片机能应对的最大高度大约只到25毫米。然而,大型接插件包括插脚在内的高度通常要超过30毫米,如果超过机器适用的规格,便需要手工插装。
FUJI的贴片机能够贴装高度达到38.1毫米(1.5英寸)的元件,从而扩大了SMT生产线上自动装配元件的范围,同时还能解决手工作业中存在的品质不稳定以及生产用时不固定的问题。
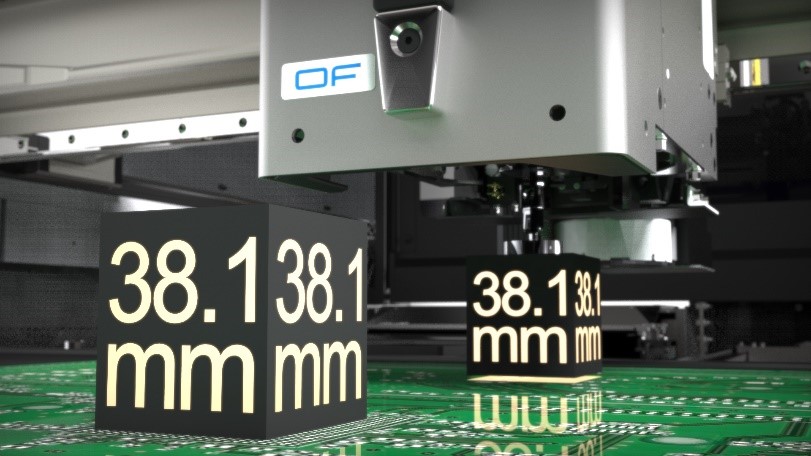
可贴装高度为38.1毫米(1.5英寸)元件
3-4. 可靠夹持贴装重型元件
边长超过100mm的超大型BGA或者大型的变压器重量有时会超过200g。FUJI工作头中载重能力最强的是DX工作头,它最高可夹持250g※2的重型元件。
但是,像这种重型元件在移动或旋转过程中非常容易脱落。为了防止吸取后元件脱落,我们推荐使用定制吸嘴。因为定制吸嘴是考虑元件的形状与重量的平衡状况去设计最合适的吸取位置的。
※2 实际值
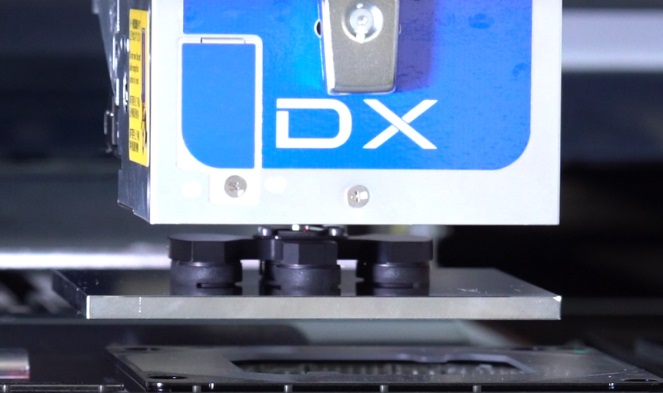
250g大型BGA的贴装
3-5. 窄间距贴装大型元件
元件上面没有平坦的表面供吸嘴吸取时,通常会采用机械夹夹持元件轮廓的方法处理。但是在面对DIMM插槽※3这种需要多个元件集中排列插装时,元件跟机械夹之间会发生干涉而导致元件损坏。这种情况下,可以采用机械夹从元件内部夹持的方法得到解决。
※3 计算机主板上的内存插槽。
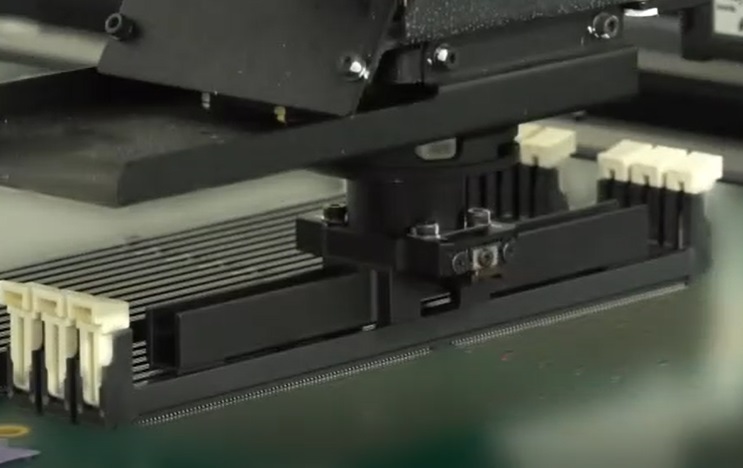
DIMM插槽的贴装
FUJI为了能够在短时间内向用户提供作定制吸嘴与定制机械夹,我们在全球各地的据点均设立了可以制作的体制。
3-6. 可靠处理易变形元件
对于最新型智能手机上采用的中介模块这样主体既纤细又易变形的元件,只能使用吸嘴去吸取。然而,中介模块的吸取面上布满了锡球,吸取面十分不平整,这种条件下使用吸嘴吸取时容易发生漏气而无法保证吸取的稳定性。
虽然使用带橡胶垫的吸嘴吸取也能解决上述问题,但因为橡胶垫需要定期更换,反而增加了成本以及管理的工时。
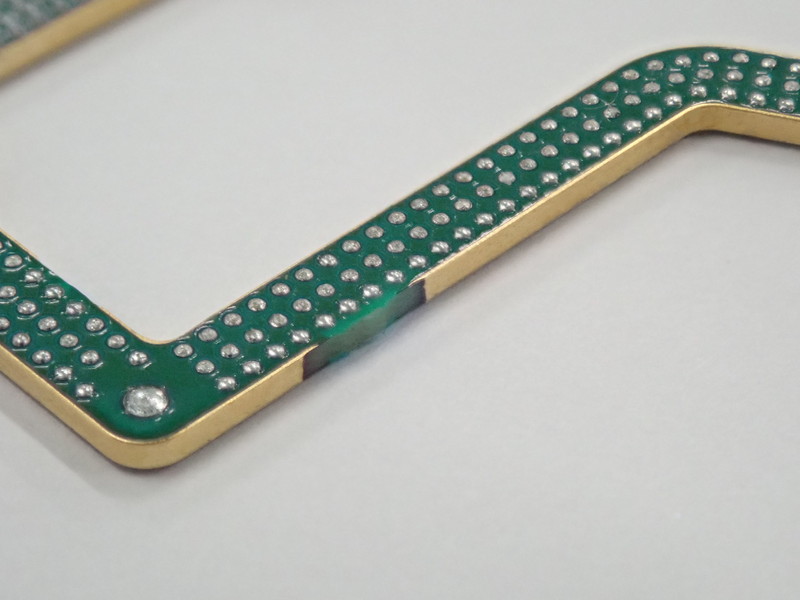
中介模块
为此,对于那些大规模使用易变形且吸取困难元件的用户,我们推荐使用增强了真空气流的大吸力H01V工作头。H01V工作头通过大幅提升真空流量,使元件吸持能力比之前增加4倍。如果H01V工作头与跟元件外形匹配的定制吸嘴组合使用,便可高速且稳定地吸取贴装那些容易变形且吸取时会漏气的元件,从而在不影响贴装品质的前提下提高生产力。
中介模块贴装视频
4. 解决大型元件的补料课题
通常大型元件都是以料盘的形式供应,由于每个元件都很大,1个料盘中能摆放的数量十分有限,因此,补料频率很高。这就会发生补错料的概率增加以及因补料延迟导致停机次数增加的问题。
4-1. 利用影像识别排查元件的搭载错误
如果元件搭载错误,虽然在开始生产后的影像处理工序中会实施一定程度的筛查,但是对于形状左右对称或者外形一样但规格不同的元件而言,单凭贴片机的影像处理很难识别,一旦目测没有发现问题,便有有可能贴错元件。
TVR元件核对功能※4使用定位相机拍摄元件在被吸取前的上表面特征。然后与数据进行核对,防止因上错料而造成的生产不良。因为通过印字核对也可进行元件的识别,所以这个功能还可以进行批次管理以及排查同一形状但规格不同元件的错料问题。
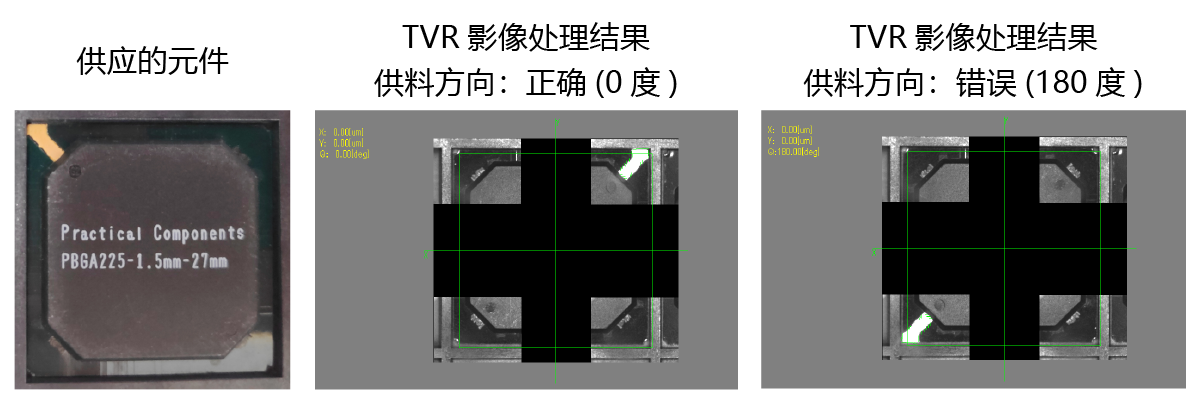
利用元件上表面的特征进行角度确认 TVR元件核对功能
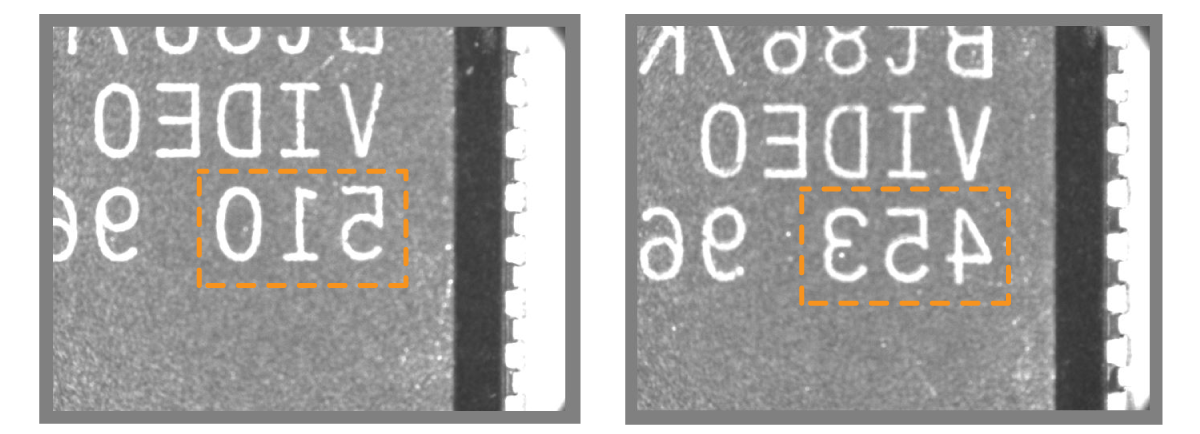
利用印字核对识别元件
对与激光雕刻等很难识别的印字,通过安装低角度照明单元※5来保证影像识别的清晰度,规避识别错误风险。
※5 适用机型: AIMEXIII、AIMEXIIIc
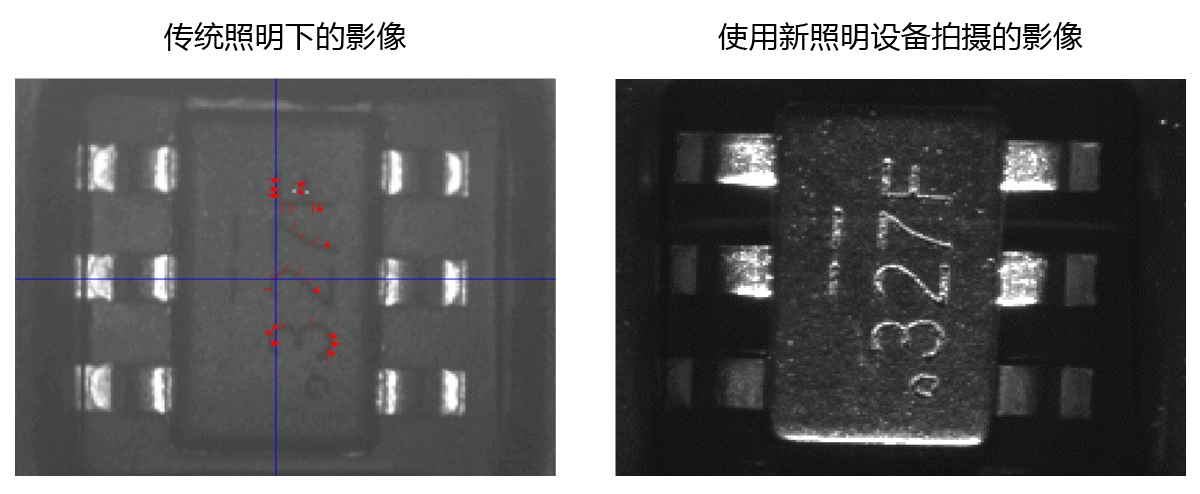
低角度照明单元
如果元件的反面上有标记或特征,可利用反面标记确认功能,使用机器相机确认元件的朝向判断元件搭载是否有误,由此防止贴装错误。
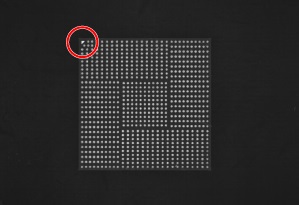
用元件反面的特征进行角度确认 反面标记确认功能
4-2. 料盘元件补料时的时间损失最小化
综上所述,因为用料盘供料的大型元件补料操作更频繁,所以补料操作的延迟有可能导致停机。
但是,FUJI的料盘单元内包含了上下两层料盘箱,通过一些操作上的配合,能够达到减少补料次数以及免停机补料的效果。
上下料盘箱搭配生产的视频
4-3. 减轻料管元件的补料负担
用料管供应大型接插件时,推荐使用水平叠放式管状供料器。料管可以堆叠摆放,当最下面的料管内元件用完时,料管会自动下落并换成下一个料管继续生产。这样可以减少使用量较多元件的补料频率,也能减轻操作员的作业负担。
水平叠放式管装料供料器
大型元件通常形状各异,通过使用符合各自特征的功能与单元,可在不降低品质与生产率的情况下完成生产。
本公司除了文中介绍的内容外,还有其他多种解决大型元件贴装课题的实用功能以及器材。
欢迎随时咨询更多详细内容。