基板・キャリアテープからの発塵やはんだペーストの付着などにより吸着エラーや接触不良を引き起こすことがあります。こうしたエラーを防ぐためには、部品の吸着・装着に直接関わるフィーダー、ノズル、ヘッドを常に良い状態に保つことが必要です。そのための機能やユニットをご紹介します。
常に状態の良いノズルで生産
ノズルは部品に直接コンタクトするため、ノズルの状態の良し悪しが、実装品質・生産性に直接影響します。
そのため、高品質な生産を継続するためには、常に状態の良いノズルを使用し続ける仕組みが必要です。
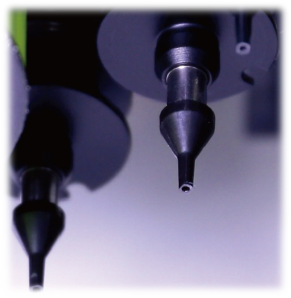
吸着エラー率の高いノズルを検出
ノズル統計異常機能
各ノズルのエラー状況を統計し、閾値に達したノズルを代替ノズルに交換して生産を継続します。
定期的なノズル交換で不良要因を排除
定期ノズル交換機能
設定した使用回数や生産枚数に達したノズルを自動で代替ノズルに交換して生産を継続します。
定期ブローでノズルの詰まりを防ぐ
定期ノズルブロー機能
設定した使用回数や生産枚数に達したノズル内部を定期的にブローし、目詰まりによる吸着不良を防ぎます。
ノズル外側に付着した埃を清掃
ノズル清掃機能
自動運転中に設定した間隔で、ヘッドにセットされているノズルをブラシを使って清掃します。
ノズルステーションタイプとフィーダータイプの2種類から選択できます。
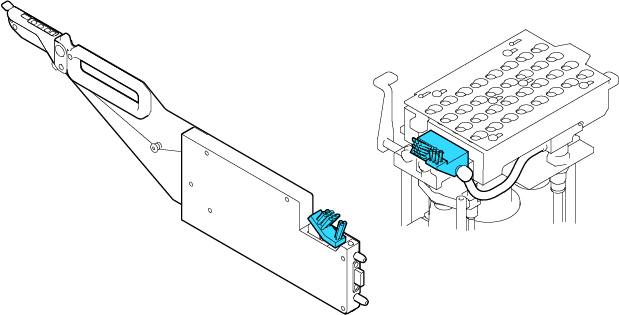
長期の使用でもヘタり、寸法変化なし
高硬度ノズル
ノズル評価テストにおいて、20,000,000ショット後も寸法変化やノズル欠けが発生しないことが確認されています。
長期間安心してご使用いただけます。
トレーニング、スキル不要の簡単メンテナンス 自動メンテナンスユニット
FUJIの実装機は、工具を使わずにヘッド等のユニットを簡単に取り外して交換できます。ユニットをメンテナンスする際も代替ユニットに交換して生産を継続し、その間にオフラインでメンテナンスを行えるため、メンテナンス時の生産停止時間を最小化できます。
また、システムと連携した運用により、デジタルファクトリーを実現するうえで必須となる作業データのデジタル化、ユニット状態の可視化が可能となります。
フィーダー内部の洗浄と送り精度の自動補正 オートフィーダーメンテナンスユニット
フィーダー内部に溜まった埃と古いグリスを除去後、自動でグリスアップを行います。
その後、ギア部のトルクやテープの送り精度検査を行い、必要に応じてテープの送り精度を自動で補正します。
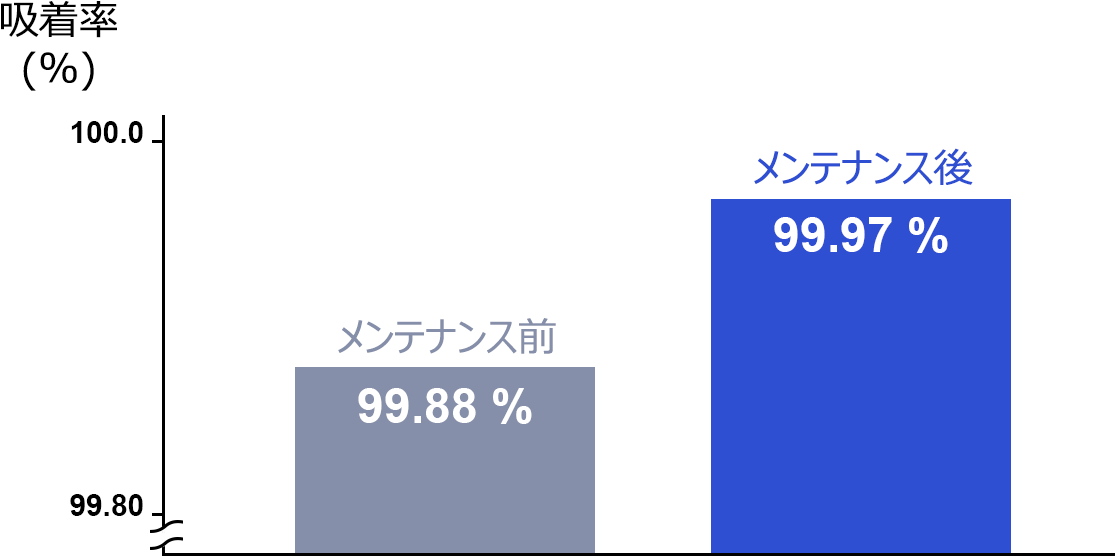
AFMU導入効果
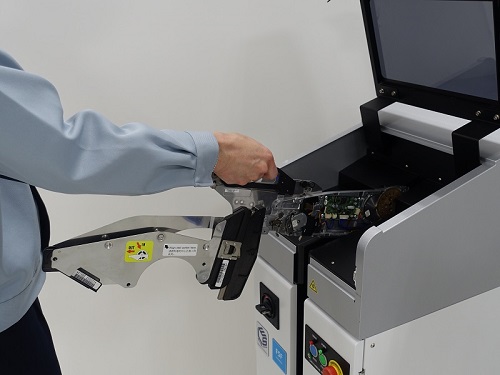
面倒なノズルの取り外し作業不要 スマートノズルクリン
実装機から取り外したノズルステーションをそのままセットしてメンテナンスを行えます。
ノズルを1本1本を着脱する必要がないため、簡単でスムーズな作業が可能です。メンテナンス後は、洗浄後のノズルに付いた水分の除去と機能検査を実施します。
最大1,140本のノズルを収納できるため、ノズルストッカーとしてもご利用いただけます。
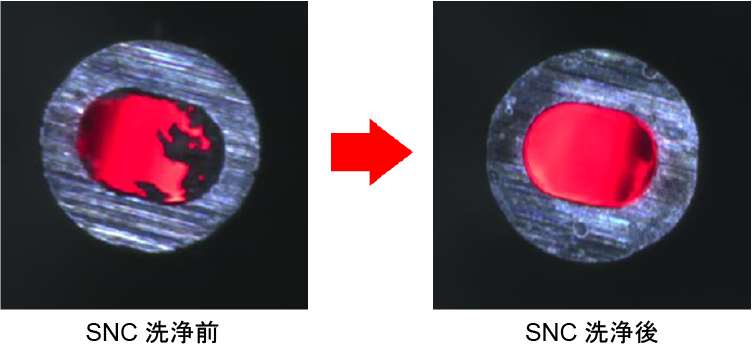
SNC導入効果
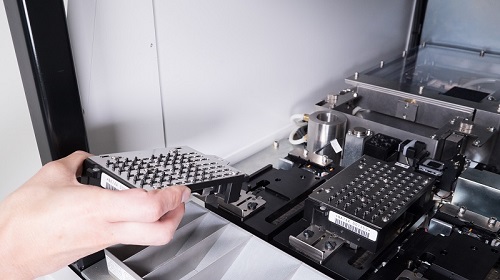
トレーニング不要な簡単ヘッドメンテナンス オートヘッドクリーナー
ヘッド内部のエアー経路を洗浄します。エアー洗浄とオイル洗浄の2つのメニューがあり、用途に応じて選択が可能です。
メンテナンス後は、各モーター、センサー部の同期状態、エアー流量を検査します。
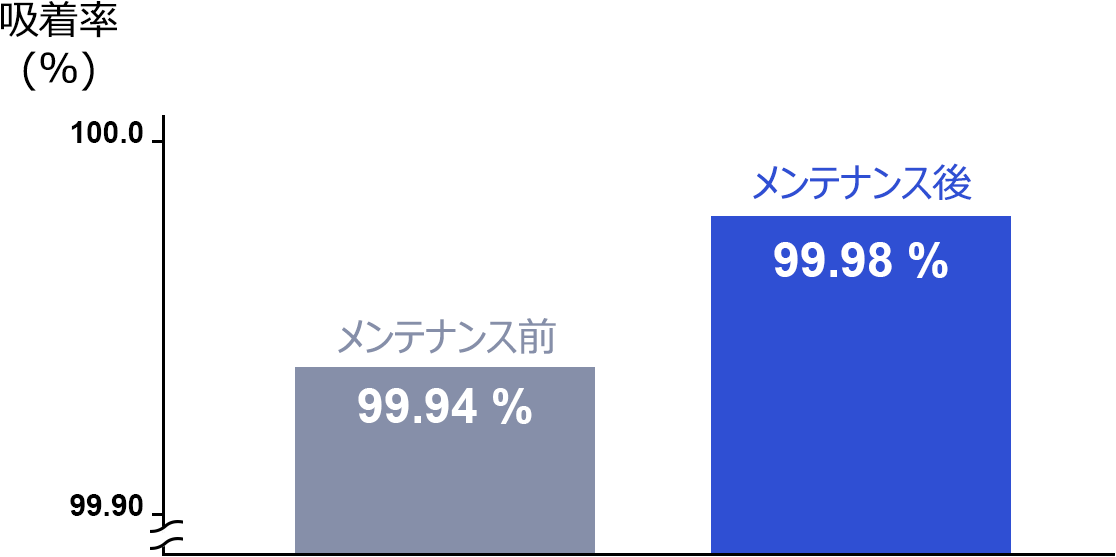
AHC導入効果
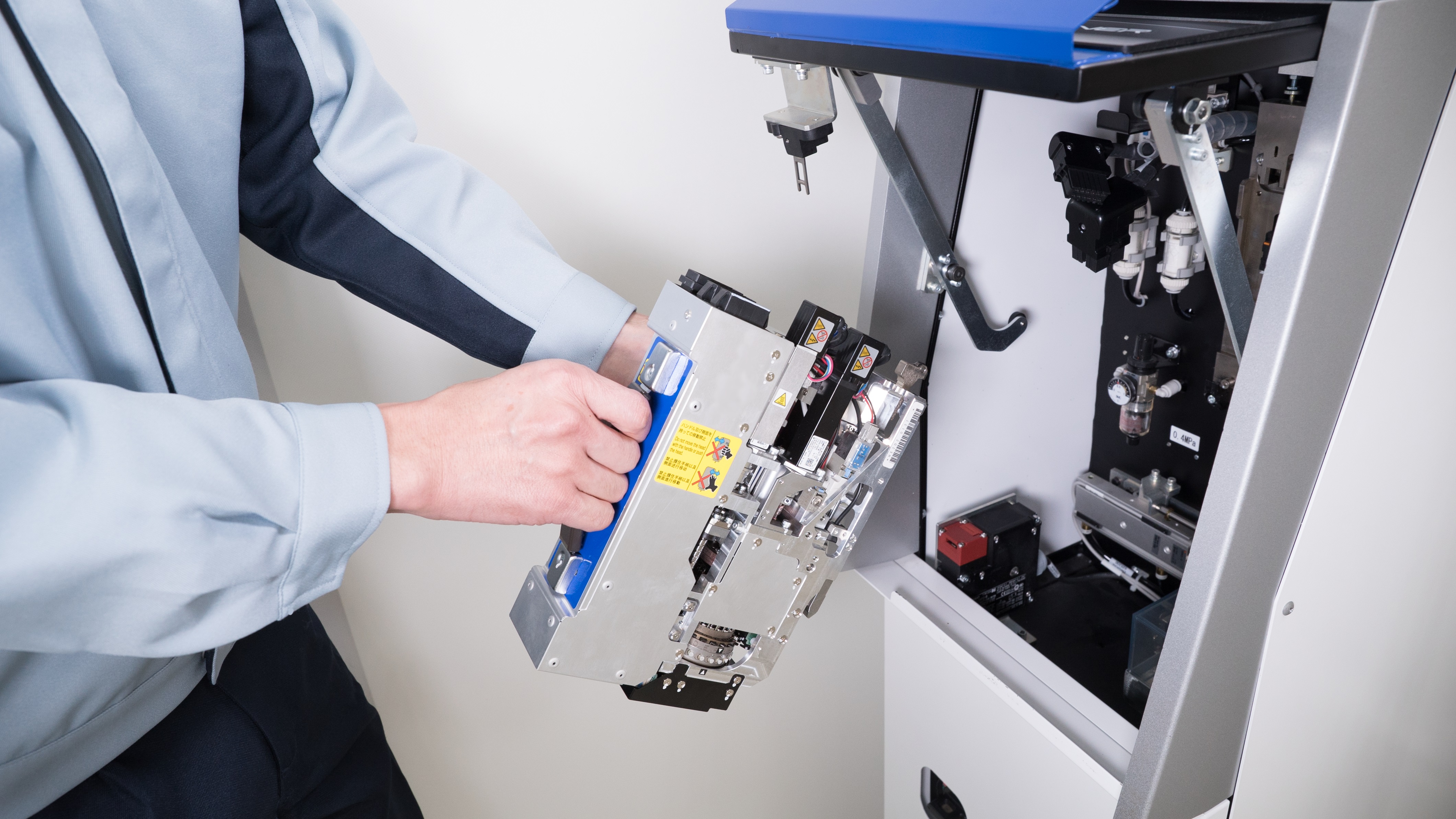
ユニット毎にメンテナンス履歴を管理 アドバンスドメンテナンス
フィーダー、ノズル、ヘッドのメンテナンス管理を支援するソフトウェアです。
ユニットが持つ個別のID毎に使用期間、吸着率などのデータを自動収集・管理し、設定した閾値に達したユニットのメンテナンスを促します。
画面に表示される案内に従ってメンテナンスを実施すれば、ユニットを常に良い状態に保ち、設備要因によるトラブルの発生を回避できます。
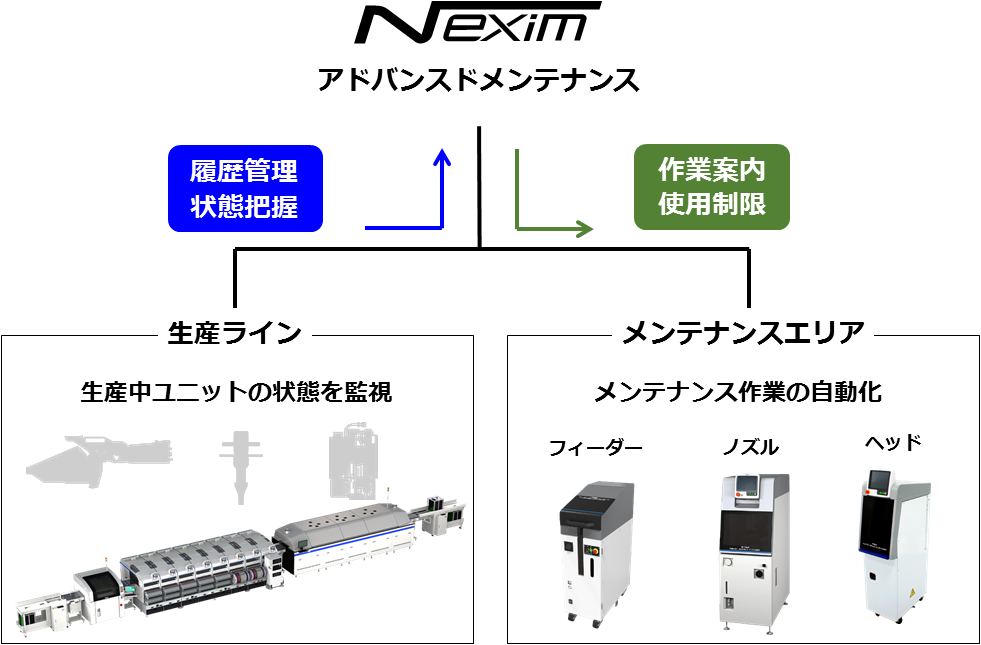