Quality is vital for medical devices. Product reliability is cultivated in our production processes.
Fuji has equipment and systems to eliminate defects and their causes to support high quality production.
It is possible to efficiently produce while maintaining high quality even when producing just the required quantities of many different types of products.
50 gf placement impact force
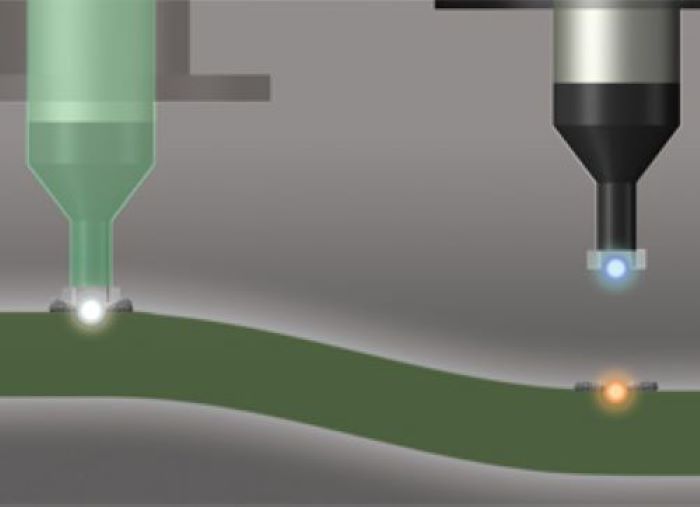
Fuji machines can detect the panel and part heights and then place at the optimum placing height.
In addition, even with a placing speed of 100%, parts can be placed with a force of around 50 gf (approx. 50 gf when placing 0402 (01005") parts), which is among the best in the world.
The presence of parts, the part's stance, and parts remaining on the nozzle after placement immediately before and after pickup and placement all can be detected for reliable placement.
Eliminates defects and catches causes of defects
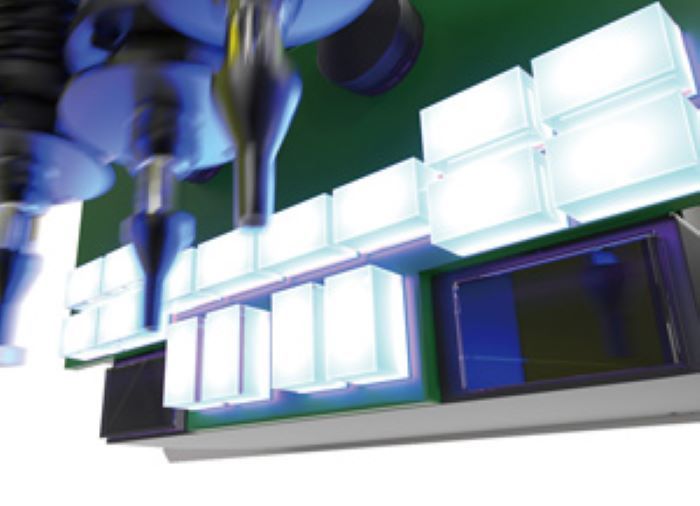
Fuji machines make quality products in the production stage so defective products are not passed to later stages.
The part misplacement prevention system, the lead and bump defect detection system, and the part electrical check system ensure that defective parts are not placed.
Traceability
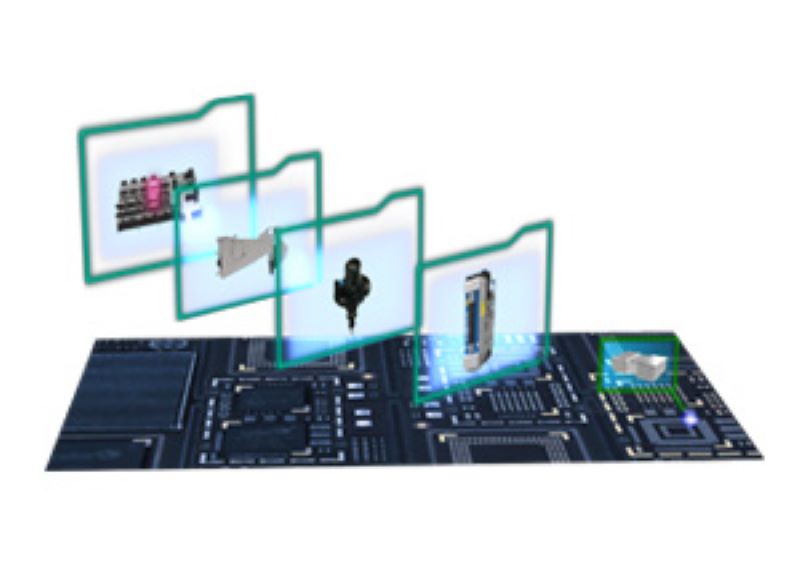
By linking the IDs used to manage the equipment that is thoroughly modularized and unitized to the placement data managed by individual references, it is possible to acquire detailed traceability data. This traceability data can be used to identify the related parts, machines, and units used for a particular panel ID or to identify the panels on which a particular part ID was placed.
Minimizes changeover work
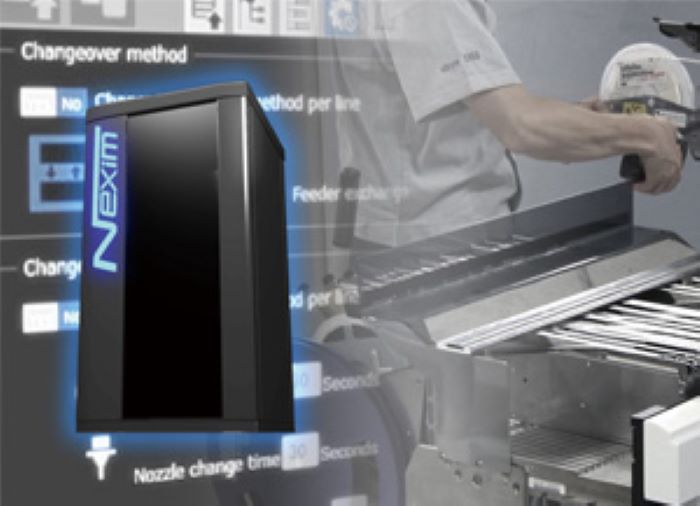
To deal with frequent changeovers necessary for the production in this field, Fuji provides a system in which the panel ID or barcode for the product is read and the program is automatically changed to the correct program. It is also possible to reduce the number of changeovers by using production schedule optimization.