Usage examples
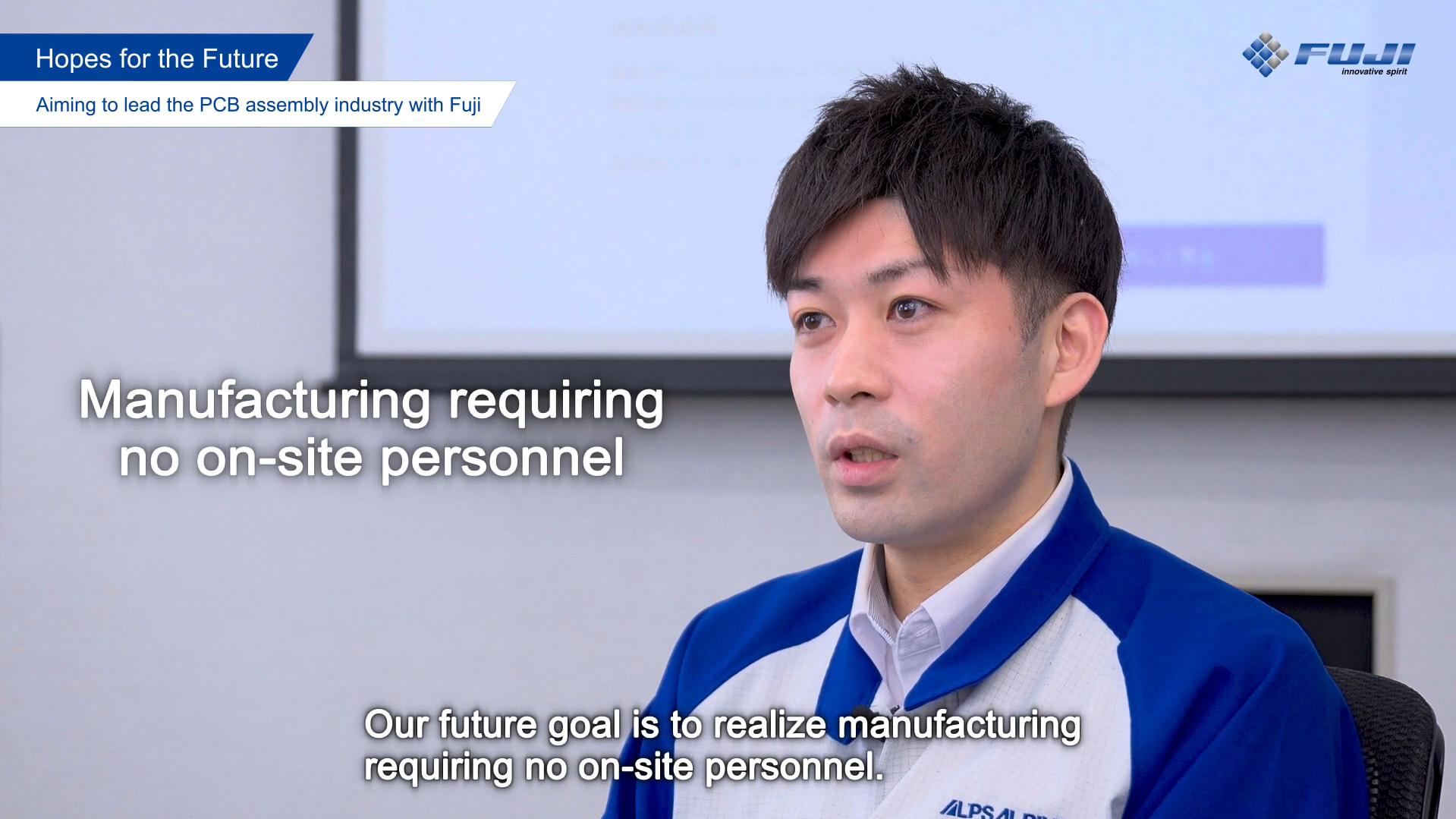
Automation made possible by FUJI Smart Factory – Case study: Alps Alpine Co., Ltd.
Alps Alpine Co., Ltd., a global company that focuses on electronic components and automotive information systems, faced challenges with equipment downtime due to changeover, short stops, delayed part replenishment. In 2024, they introduced FUJI Smart Factory to boost their productivity and quality. This introduction led to an increase in their operating rate and quality through fully automated feeder exchange without the need for operators. The automation rate soared from about 12% to 56%, a 44 percentage point jump, enabling 5 to 6 hours of unmanned automated production.
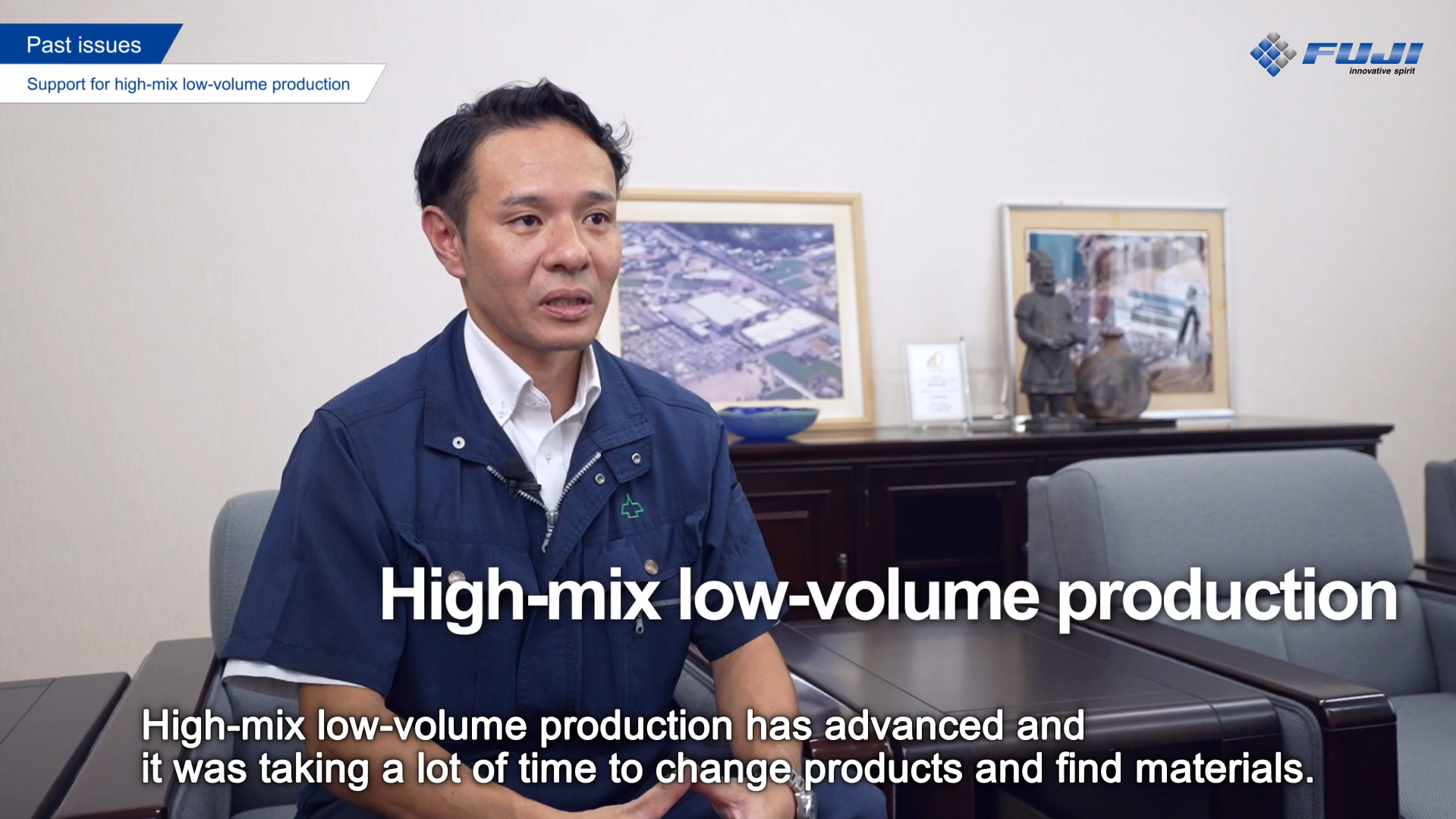
Automation made possible by FUJI Smart Factory – Case Study: Takaya Corporation
Takaya Corporation (Est. 1894, Okayama Prefecture) is a company with a long history in various electronics industries both in Japan and overseas. In recent years, Takaya has been focusing on reducing the time required for product changeover and searching for production materials, especially in the context of high-mix, low-volume production. In 2021, Takaya introduced FUJI Smart Factory (FSF) with its combination of system and automation technologies. As a result, product changeover and parts supply within the SMT line were automated, and significant labor saving was achieved. FSF also allows factories to entrust even new workers with managing production lines, with less time required for passing on know-how to new workers.