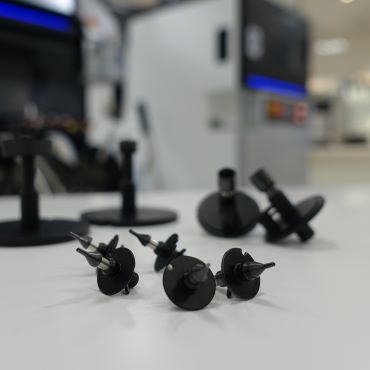
Automatic nozzle quality management for improving OEE
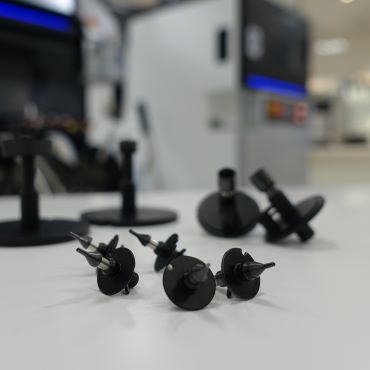
To respond to increasing and changing product variations in line with diversified consumer needs, production sites have been tackling high-mix low-volume production and variable-mix variable-volume production in recent years. Surface mounting technology (SMT) production sites are no exception. Smaller chip parts, heavier package parts, and increased types of custom parts are requiring a greater variety and quantity of nozzles for handling electronic components on a daily basis. In addition to this situation, nozzles for chip parts are very small and difficult to handle. It is highly likely that this has increased the man-hours required for production preparation, changeover, and maintenance.
Since the nozzle condition significantly affects the overall equipment efficiency (OEE), it is critical to monitor the condition of nozzles, even during production, and manage nozzles in order to ensure that nozzles in poor condition are not used in production.
In this article, we introduce various management functions that utilize individual nozzle ID management technology, focusing on reducing equipment-related losses (availability losses, performance losses, and quality losses) that lower OEE.
Parts picked up by nozzles in poor condition, such as nozzles with a stuck sliding section or chipped nozzle tip, are discarded due to errors detected for the pickup stance. If production is continued without noticing the issue, a large amount of parts will be discarded, causing a great loss. The nozzle statistical warning function is designed to prevent part loss and reduced productivity caused by such defective nozzles.
When the nozzle in use reaches the set pickup error count, the machine is stopped to prevent such losses. If replacement nozzles are set in the nozzle station, defective nozzles are automatically replaced with the replacement nozzles without stopping production. This makes it possible to minimize the loss of productivity while maintaining quality. Nozzles that have been subject to the warning cannot be used in production until the warning counter is reset.
Applicable machines | NXTR S model, NXTR A model, AIMEXR NXT, NXT II, NXT IIc, NXT III, NXT IIIc AIMEX, AIMEX II, AIMEX IIS, AIMEX III, AIMEX IIIc NXT-H, NXT-Hw |
---|---|
Applicable heads | NXTR and AIMEXR series: There are no head restrictions. NXT and AIMEX series: There are no head restrictions. NXT-H, NXT-Hw: H24 series, G04F(Q), H08M(Q) |
This function identifies nozzles requiring maintenance based on the nozzle pickup error rate, usage period, and other factors, and manages such nozzles to ensure that they are not mistakenly used on production lines.
Nozzles with the pickup error rate or usage period reaching the specified conditions are automatically replaced with replacement nozzles to continue production. If there are no replacement nozzles in the nozzle station, the machine will be stopped, prompting operators to replace the nozzles that require maintenance. This ensures that production can continue with nozzles in good condition at all times.
NXTR application: V1.10 or later
AIMEXR application: V1.00 or later
NXT application: V7.70 or later
AIMEX application: V3.30 or later
This function reduces the pickup force loss due to dust and other foreign objects inside nozzles.
Nozzles require periodic maintenance to maintain the pickup rate as they vacuum dust inside the machine during part pickup. Nozzles used in production sites running for long operating hours or nozzles used frequently often accumulate dust inside in a short period of time, with the error rate increasing before the next periodic maintenance.
Such cases can be handled by stopping production and performing maintenance only for specific nozzles with high error rates. However, this should be avoided as much as possible because the increased number of stops leads to lower productivity.
With the periodic nozzle blow cleaning function, the air channel inside each nozzle is blown every specified pick and place cycle to keep the nozzles clean and thereby reduce the pickup rate loss.
Applicable machines | NXT II, NXT IIc, NXT III, NXT IIIc |
---|---|
Applicable heads | H04, H08M |
This function is used to remove dirt from the nozzle surface to prevent misrecognition during vision processing and thereby prevent a decrease in the pickup rate.
Dust on the nozzle surface can affect vision processing, resulting in a lower pickup rate. Cleaning nozzles regularly using a brushing unit equipped with the machine can reduce the occurrence of vision processing errors.
Brushing units are available in two types: Nozzle station type and feeder type.
Note: Option item
Applicable heads | NXT and AIMEX series: H24 series, V12, H12HS(Q), H12(S), H12L, H08(Q), DX(R12) Note: DX(R12) heads are supported by feeder type brushing units only. |
---|
Our nozzles have a two-piece construction, with the tip and holder made of separate parts, to minimize the load on parts during pickup and placement. However, if the nozzle sliding section does not move smoothly, a greater load than expected may be applied during part placement, resulting in damage to parts or solder bridging.
To prevent such problems, this function periodically checks the movement of the nozzle sliding section (stuck or not) by pressing the nozzle against a specified location in the machine. When stuck nozzles are detected, the machine will be stopped, preventing pickup and placement failures caused by overloading.
Applicable machines | NXT II, NXT IIc, NXT III, NXT IIIc |
---|---|
Applicable heads | H24 series, V12, H12HS(Q) |
Intelligent part sensors (IPS) vision process the nozzle tip condition from the side to detect nozzle errors, such as unusual length, foreign object adhesion, or cracking.
By using IPS together with the nozzle statistical warning function described in section 2-1 and setting replacement nozzles in the nozzle station, detected defective nozzles can be automatically replaced with replacement nozzles without stopping production.
Unusual length
Foreign object adhesion
Applicable heads | RH28, RH20, RH08, H24 series, V12, H12HSQ, H08Q, H08MQ, DX (R12), G04FQ, G04Q |
---|
Management Monitor is a tool that constantly monitors production status.
This aggregates the pickup error counts for nozzles used in production for each nozzle ID and displays the results in a ranking format. By checking the pickup error ranking by part number and slot, which can be displayed in the same screen, it is possible to identify nozzles in poor condition.
Error-prone nozzle ranking display
We have introduced automatic nozzle quality management functions effective for reducing nozzle-caused losses for improved OEE.
Each nozzle is managed with a unique ID, which allows reliable nozzle management with all production-related information linked.
For more details on the functions, please feel free to contact us using the contact form. Casual inquiries welcome.