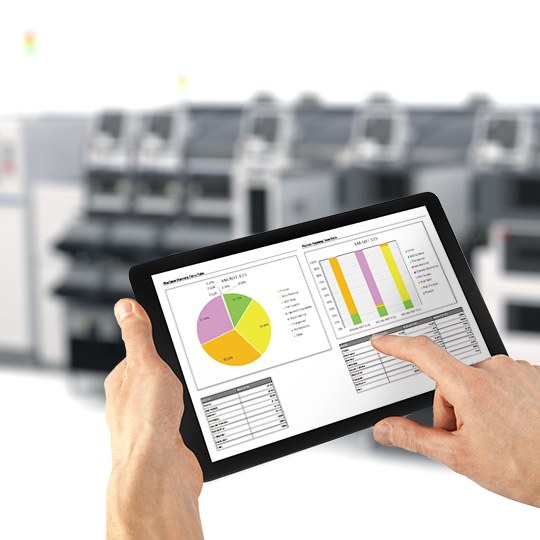
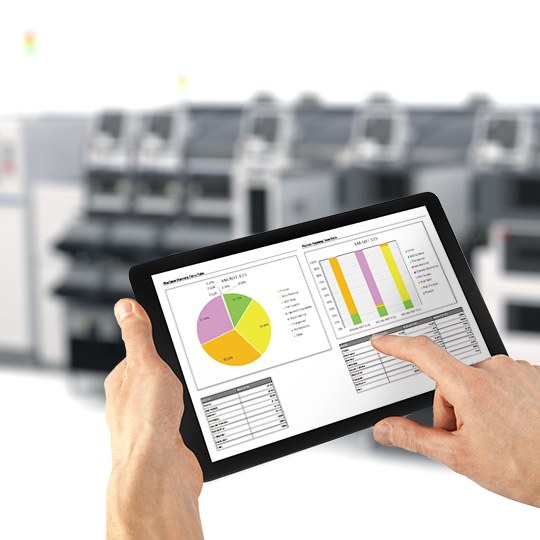
実装現場では高品質や高効率を常に求められ、その達成のための新設備の導入と維持には高いスキルや管理能力が求められます。そのような状況で役立つのがFUJI Kaizenサービスです。
当記事では、FUJI Kaizenサービスについて解説するとともに、具体的な進め方やポイントなどをご紹介します。現状よりもさらに良い現場づくりを目指している方は是非参考にしてください。
FUJI Kaizenサービスとは?
FUJI Kaizenサービスとは、設備メーカー独自の視点から生産現場やプロセスなどを見直して現状よりも更に効率化を図り、より良い状態を目指す取り組みのことを指します。
FUJI Kaizenサービスには大別すると導入提案、生産診断、生産支援の3つがあります。
1. 導入提案
設備構成・生産運用の最適化提案、FUJI 自動化推進のご提案
2. 生産診断
既存設備の有効活用術、生産の可視化・OEE向上のご提案、ロジステック診断、オペレータ作業軽減のご提案
3. 生産支援
実装技術者向けトレーニング、新しい部材の実装テスト・評価、共通部品配置表の代行作成、プログラム座標変換作業のサポート
FUJI Kaizenサービスの進め方
PDCAサイクル
・生産課題の抽出・洗い出しする
・課題に対する改善できるアイデア及び改善提案をする
・アイデア・提案の実行確認及び評価をする
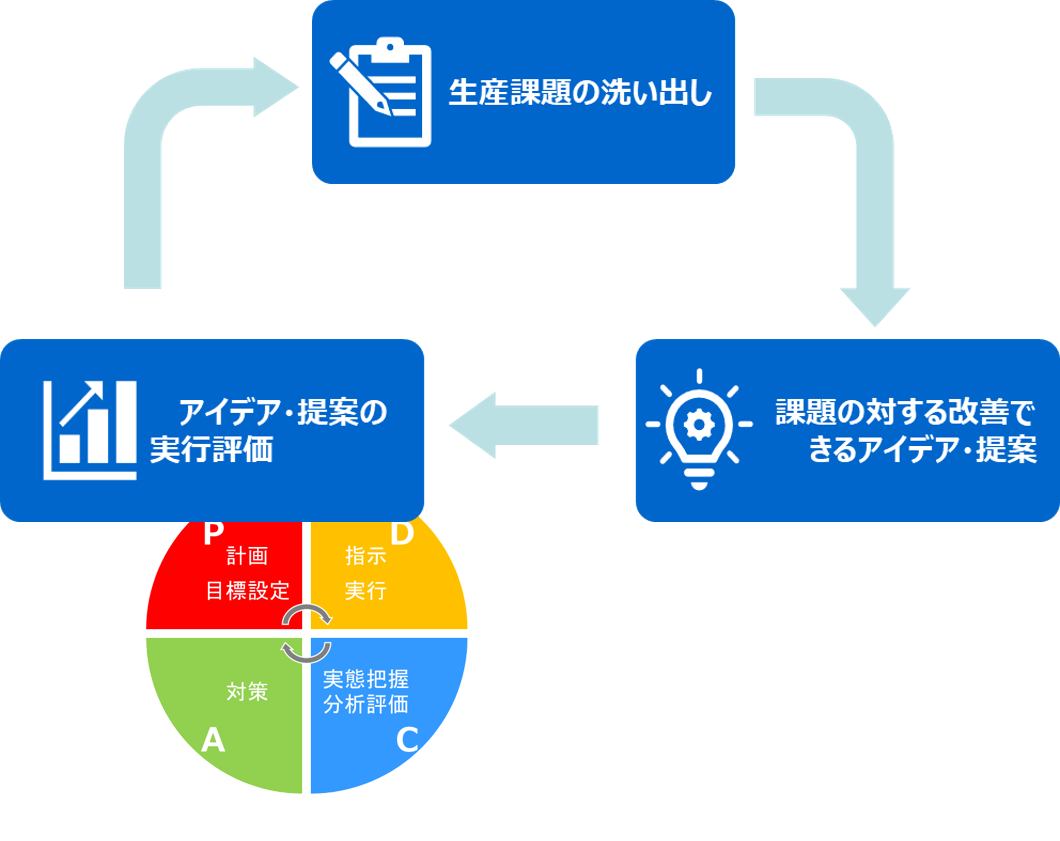
FUJI Kaizenサービス事例
FUJI Kaizenサービスのさまざまなメニューの組み合わせることができます。お客様の現状に適した寄り添ったサービスを提供しています。
いくつかの事例を紹介いたします。
1. オペレータ、プログラマ弱点補強支援型プラン (2-3Days)
FUJI Kaizenメニュー:生産診断
テーマ:設備の活用状況を診断し不足スキルの抽出及び現地教育
現場の課題・弱点を把握
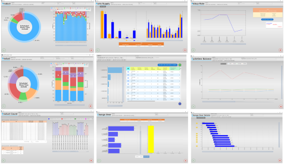
- 段取り時のフィーダー交換回数が多い
- 特定部品の装着ずれ
- 特定部品の画像処理エラー・吸着異常
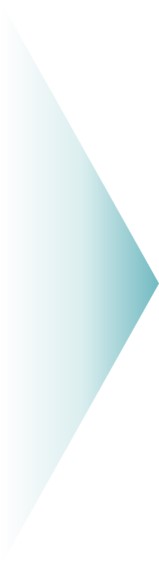
見直しスキルを抽出
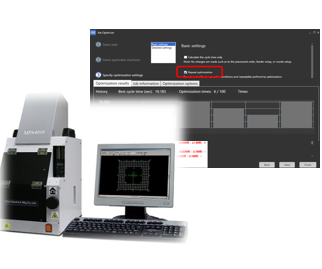
- オプチマイズ方法(グルーピング)
- 最適ノズル・設定の選択方法
- メンテナンスの判別・方法
- 画像処理データの作成方法
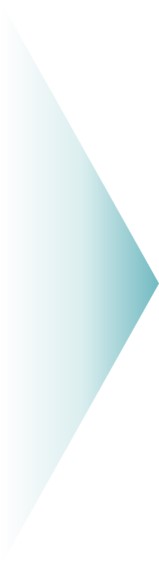
現地トレーニング
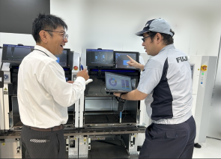
- Multi Job Line Balancer活用術
- オプチマイズ設定方法
- 装置機能設定と最適ノズル選択方法
- ASG活用術
- 画像処理データの詳細設定方法
2. OEE向上 提案型プラン (5Days)
FUJI Kaizenメニュー:生産診断
テーマ:実稼働時間を増やして、生産性向上及び安定化を目指す
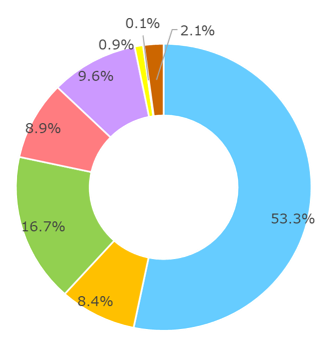
STEP1:
ライン稼働から改善
ポイントの追求
- 段取り作業の遅延
- 補給部材の事前準備
- 検査機の虚報
ライン稼働分析
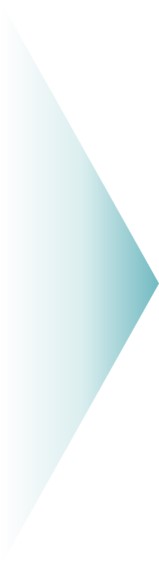
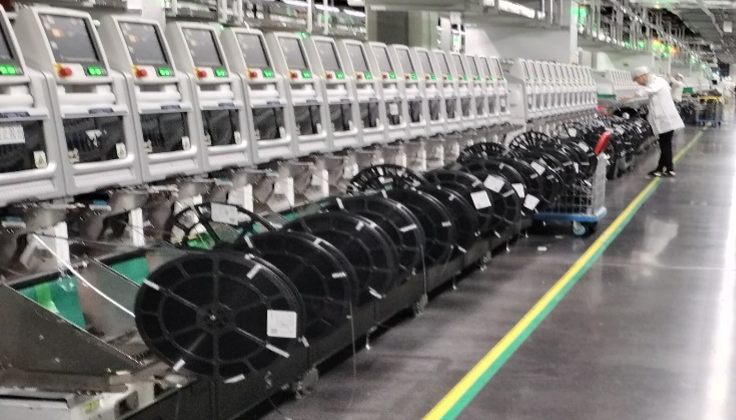
STEP2:
現場での課題を抽出
- 段取り作業の遅延
→開始タイミング、内段外段の区分け、作業ステップ - 補給部材の事前準備、補給タイミング・供給精度
→補給部品の捜索、部品切れ予告タイミングetc. - 検査機の虚報状況
→虚報率が高く、オペレータの対応遅延が発生
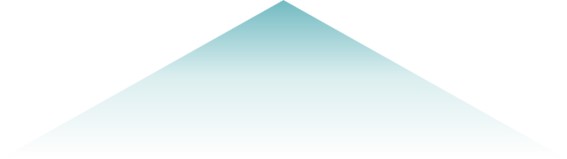
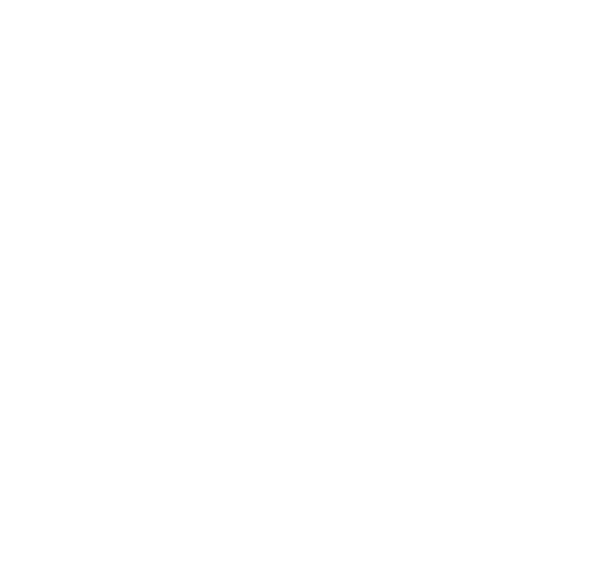
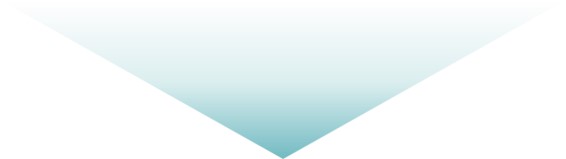
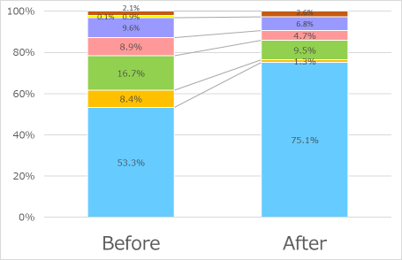
STEP4:
検討内容の効果確認
- 段取り時間の短縮
- オペレータ作業の簡略化
- 検査機 オフライン対応
効果測定
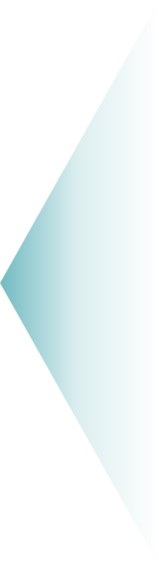
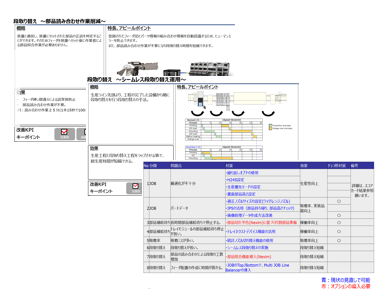
STEP3:
課題に対する検討
Action Tracker作成
- 各課題に対する対応策
- 対応効果の算出
- ToDoリストの作成
3. 設備構成最適化プラン (5-10Day)
FUJI Kaizenメニュー:導入提案
テーマ:生産フォーキャストに基づいたライン構成最適化提案
1. 既存設備の整理
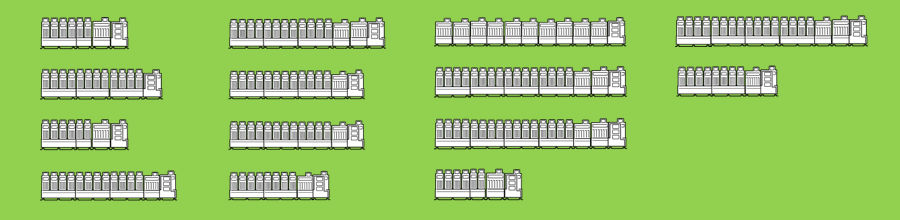
- 14ライン
- 158モジュール
- 生産時間
6128時間/月
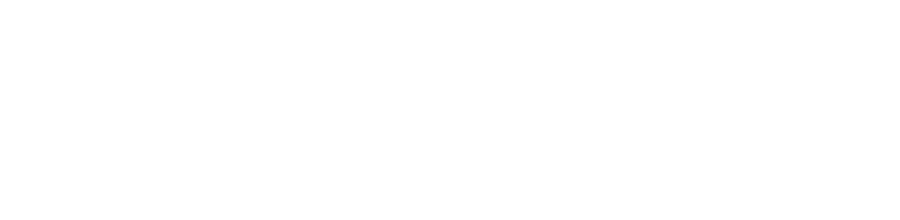
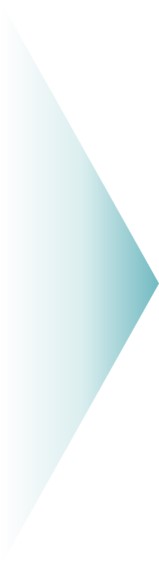
2. ライン構成の検討
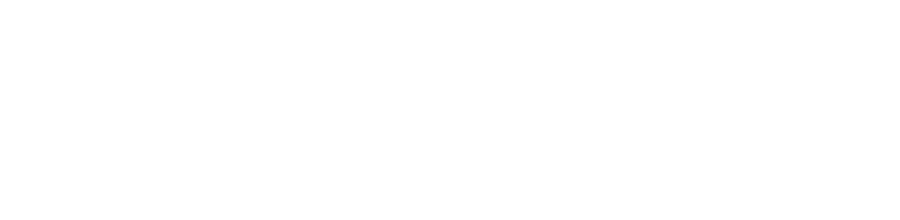
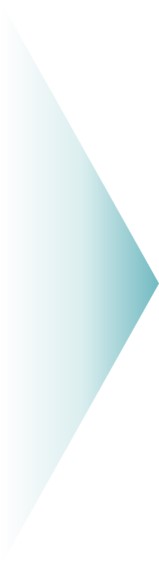
3. ライン構成の再構築
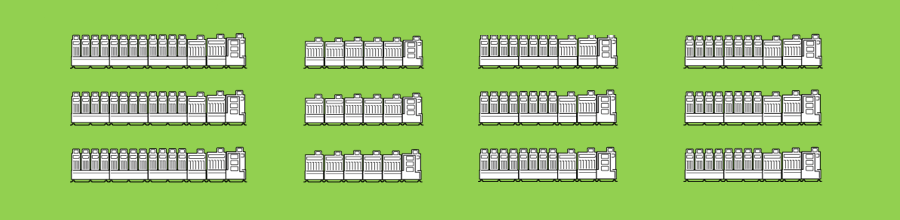
- 12ライン
- 128モジュール
- 生産時間
5317時間/月
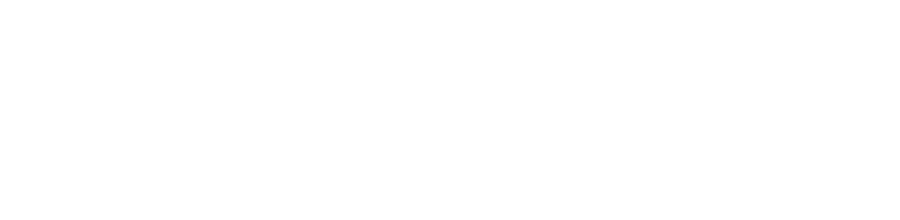
生産現場のお困りごとはございますか?
FUJI Kaizenサービスでは、様々な側面から生産現場のサポートを行っています。
下記はお困りごとの一例です。
1.設備を正しく使用しているのか、有効的に活用できているか知りたい
2.生産性が思っているほど上がらない
3.他社の生産現場と比べて、自社がどのような立ち位置が知りたい
4.段取り替え時間とサイクルタイムを短縮するにはどうすれば良いか知りたい
5.生産計画に合わせた効率のよい装置構成を検討したい
等々、生産現場のお困りごとは弊社営業へ是非ご相談ください!