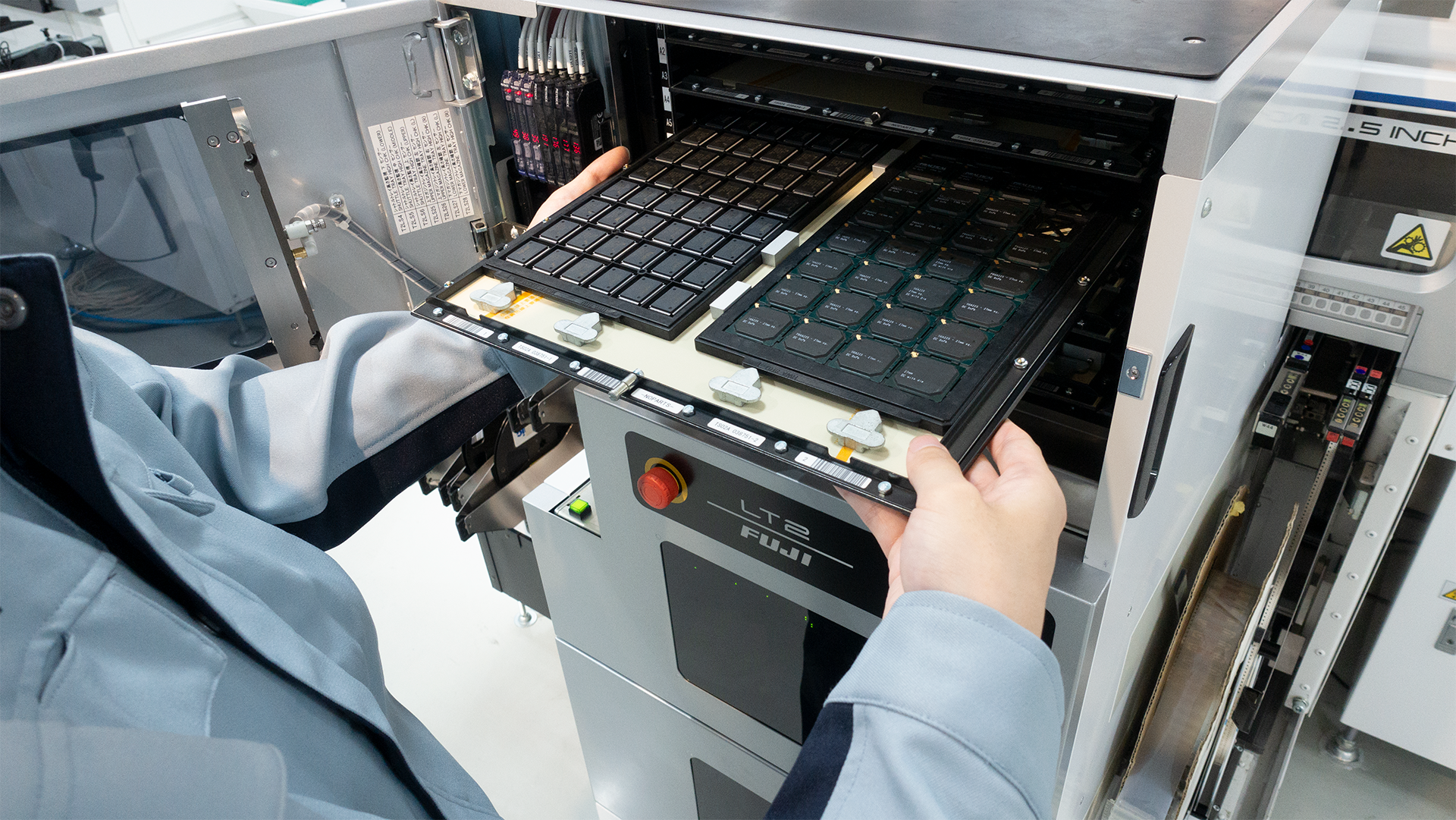
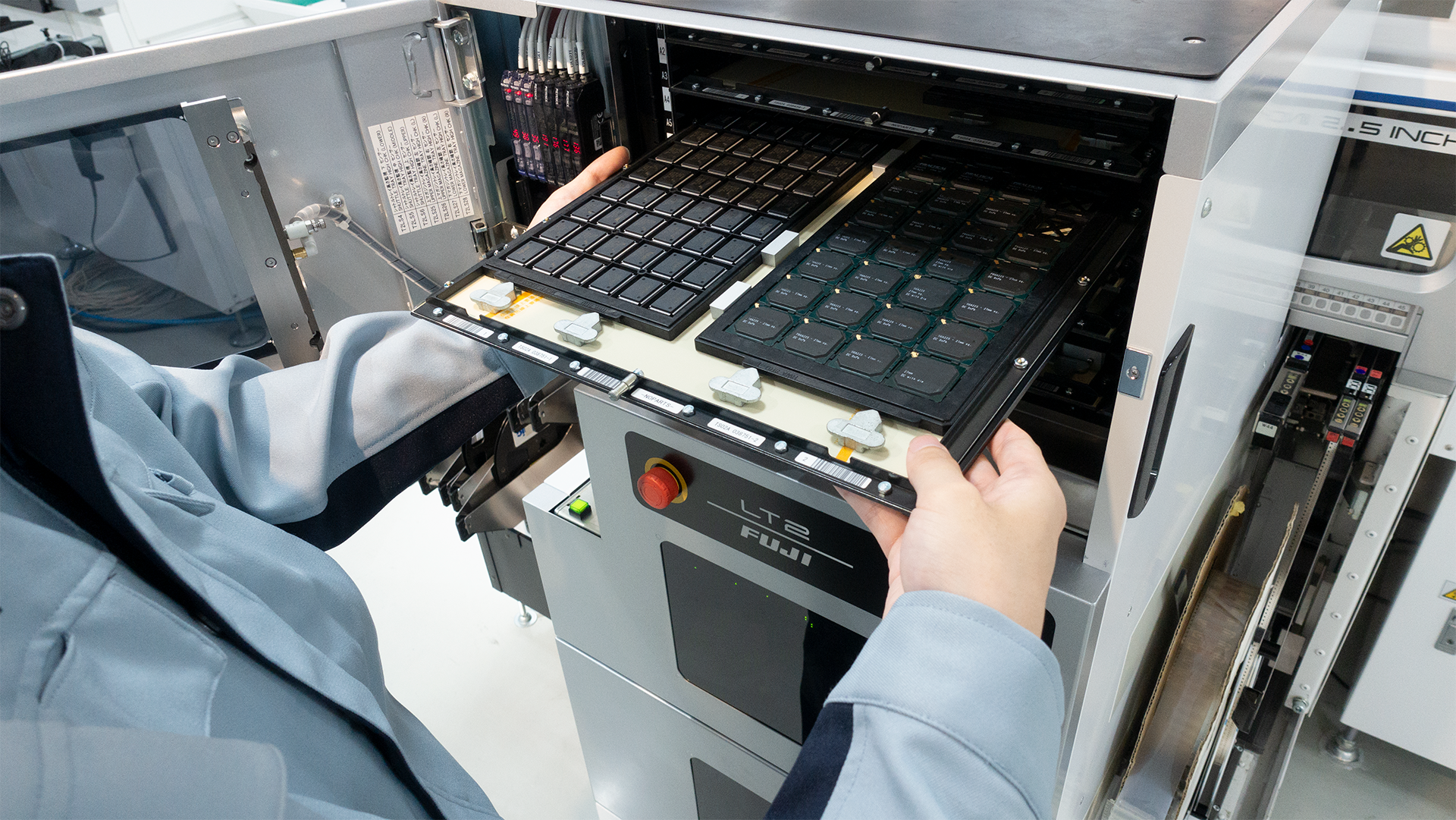
Considering tray parts tend to have properties that make them susceptible to humidity, it is not possible to prepare the parts in advance or use batch changeover methods for supplying or performing changeover with these parts. There is also a high rate of human error when supplying parts that have directionality to the machine, which is a major issue for factories.
We would like to introduce tray supply methods that address these issues.
Fuji tray units
There are two magazines into which trays can be set; an upper magazine and a lower magazine. The roles these two magazines play enable combinations that support a wide variety of situations in production.
Operation for minimizing production stop time when replenishing parts
When using large quantities of the same part type:
Set trays of the same part type in both the upper and lower magazines (AA mode)
The upper and lower magazines supply parts interchangeably, and the magazine currently not in use can be used to replenish parts while the other is still supplying parts to the machine. This enables continuous production over a long period of time.
Operation flow
1. If parts run out in the upper magazine, parts are then automatically supplied from the lower magazine.
2. The operator removes empty trays from the upper magazine, and replenishes tray parts.
3. If parts run out in the lower magazine, parts are then automatically supplied from the upper magazine.
4. The operator removes empty trays from the lower magazine, and replenishes tray parts.
If there is a large difference in quantities of each part type being used:
Always arrange the tray parts for replenishment in the tray drawers of the lower magazine (upper magazine priority mode)
his type of operation enables continuous production over a long period of time while minimizing the quantity of partially used trays of parts.
Operation flow
1. The operator sets tray parts into a tray drawer for resupply in the lower magazine before parts run out in the upper magazine.
2. If parts run out in the tray drawer for production in the upper magazine, it is automatically switched out with the tray drawer for resupply in the lower magazine.
3. The operator removes the empty trays from the tray drawer that was sent to the lower magazine, and replenishes tray parts.
Operation for reducing production stop time during changeover
The upper magazine is used in production, while the lower magazine is used for changeover (changeover mode)
By assigning the roles of each magazine as one being for current production and the other for next production, it is possible to prepare for next production while current production is being performed.
Operation flow
1. While the upper magazine is being used for production, the operator sets the tray parts to be used in next production in the lower magazine.
2. While the lower magazine is being used for production, the operator then sets the tray parts to be used in next production in the upper magazine.
(This process is then repeated)
Operation for preventing short stops and defects caused by setting mistakes
Allocate replenishment tray parts to any empty position (Dynamic alternate tray mode with RFID location check) *1
Tray parts can be recognized automatically using an RFID system.
The system automatically recognizes the registered tray and tray drawer combination for that part type when the tray drawer is set, so the operator is able to set the tray drawer to any available position.
*1. Option function
Automatic check of part supply direction (TVR function)
The lettering and marks inscribed on the tops of parts are checked by the machine using a camera to check the direction parts are being supplied in.
The direction of parts is checked when trays are set and when parts are returned. If parts are facing the incorrect direction, the part direction is corrected for placement*2. This prevents defects caused by parts placed in the incorrect direction.
*2. Applicable heads: H01, H02 series, OF, DX with S1 tool
Resupplying and performing changeover for tray parts is prone to high error rates, and reducing work time can be hard, but by selecting the operation method that works best for your factory's needs it is possible to reduce production stop time and prevent short stops and defects that are caused by setting mistakes.
For more details, contact us using the contact form. Casual inquiries welcome.