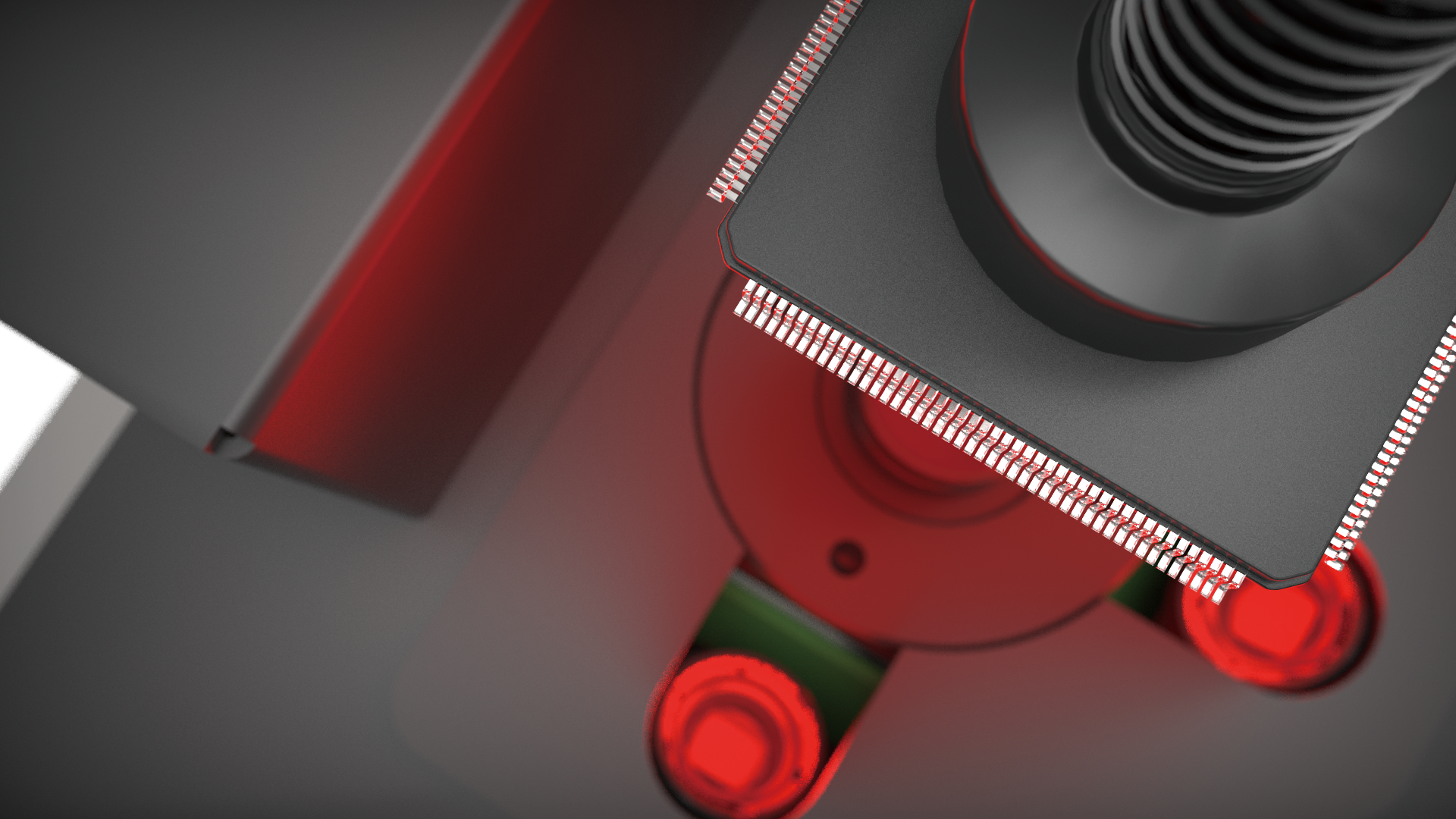
Excluding future defects attributed to parts
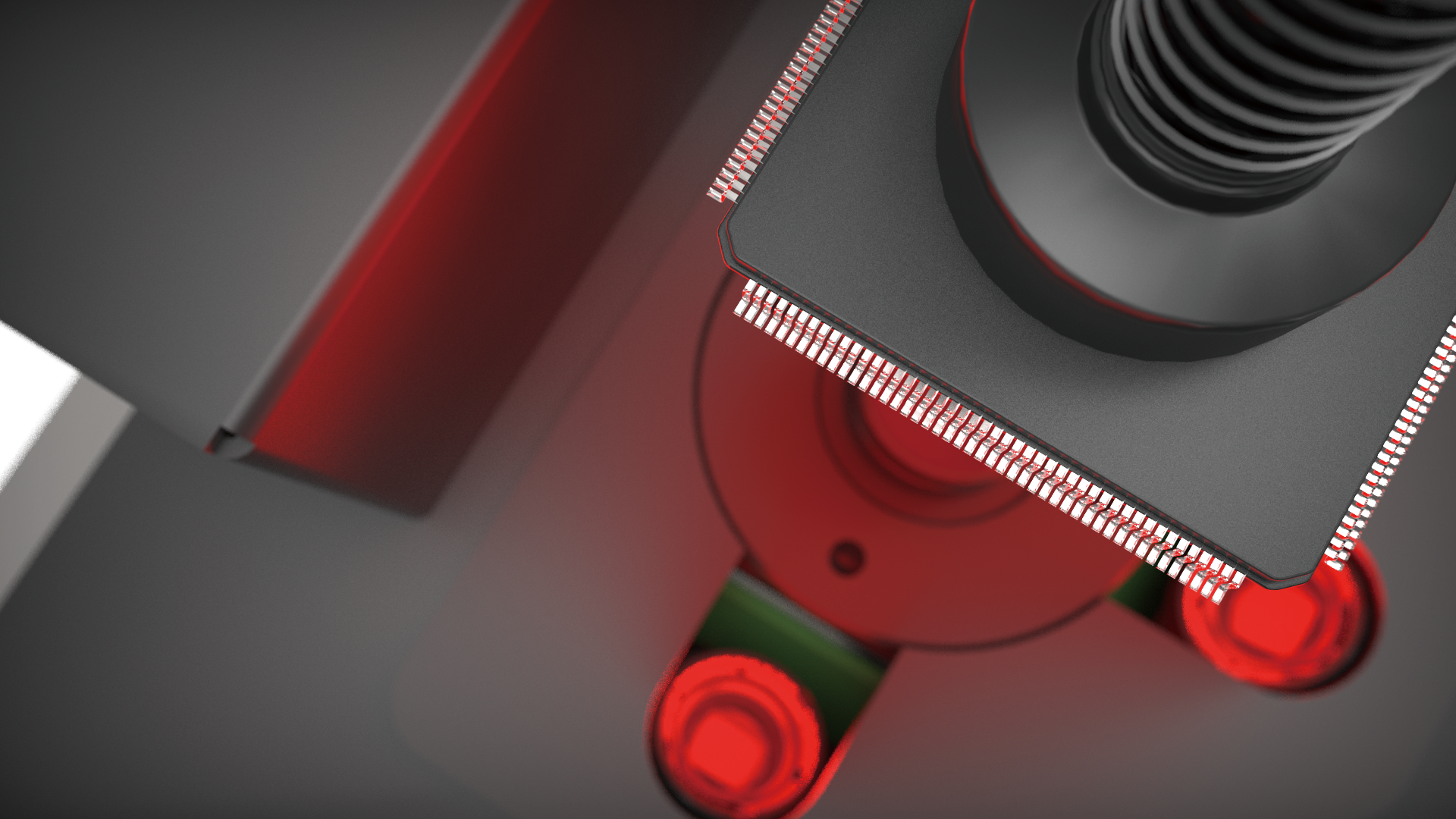
Highly accurate and functional placement machines do not always result in defect free production if the part to be placed is the source of the problem. To maintain high quality, it is very important to control production so that defective parts are not used, just as it is important to ensure good pickup and placement processes.
The following introduces applications to reliably detect defective parts and incorrect parts, and eliminate their usage.
This detects problems with packages and connector leads, and problems with the bumps on BGAs and CSPs. Because this method even detects deformation in the Z direction that is difficult to detect using part imaging cameras, it is possible to achieve elimination of deformed parts that are likely to cause connection issues.
Data from measurements can be saved to use for traceability purposes.
Because LCR values for parts are checked inside the machine which is free from human intervention, any part setting mistakes by human errors will be detected.
Measurement timing
· When starting and resuming operation
· When resupplying parts
· When performing a sampling check (under development)
Data from measurements can be saved to use for traceability purposes.
Unique features on the tops of parts, for example printing and marks, are recognized by vision processing to prevent placement defects due to a wrong angle. It is possible to determine the supply direction even for parts for which the bottom side does not have unique features identifiable for the direction.
Also, it recognizes special features such as alphabetical letters and numbers to prevent production from using the incorrect parts. This is effective for preventing mistakes in setting parts that people can easily confuse with other parts such as those that look alike but are different in specifications.
This application manages the usage history of package parts that are sensitive to moisture absorption and prevents parts that exceed the floor life from being used to avoid defects that occur during the reflow process.
Advanced Parts Management (dry component management)
· Manages the floor life after opening the package
· Supports moisture management
· Supports rebaking of parts to reset the floor life
· Manages the time that parts can be stored in moisture free storage