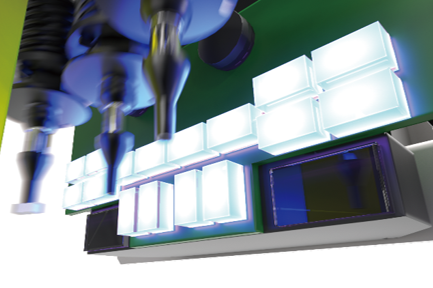
Preventing defective pickup and placement
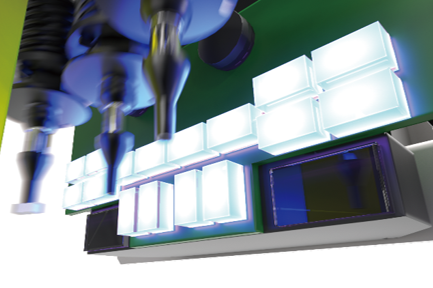
To keep the productivity high, factors that cause defects must be detected and eliminated through accurate recognition of the part state in a series of processes from pickup to placement.
The following introduces checks on part states for pickup and placement.
Every nozzle is checked before and after pickup, and before and after placement by a camera on the head, ensuring that no factor that may cause defects remains.
By checking picked up parts from the side, tombstoned chips and upside-down minimolds are accurately detected.
Measuring the part thickness from the side and reflecting it to the placement height prevents excess load from being applied to parts during placement.
By checking the part presence before and after picking and before and after placing the part, it ensures that no placements are missed due to dropped parts and parts remaining on the nozzle.
Prevents pickup defects from bent nozzles and stuck nozzles as well as trouble associated with defective nozzles such as interference due to nozzles being too long.
Detects dust and foreign objects on the tips of nozzles so that corrective actions can be taken to prevent pickup errors such as dropped parts during part transfer.
Dropped parts and parts remaining on nozzles after part pickup and placement, and also before and after rejecting parts are detected to prevent missing parts and other placement defects.
Operating with this check does not increase the cycle time.
The two sides of registers that are in different colors across the sides are identified to prevent the parts from being placed upside down.
The machine recognizes unique features on the bottom of the parts using the camera to check the top/bottom orientation and supply direction of the parts.