There is always a demand for high quality and high efficiency at production sites and the introduction and maintenance of new equipment to achieve this requires a high level of skill and management ability. FUJI Kaizen Service is useful in such situations.
In this article, we will explain FUJI Kaizen Service and introduce concrete procedures and important points. If you are aiming to create an even better workplace than the one you currently have, this may help you to proceed.
What is FUJI Kaizen Service?
FUJI Kaizen Service is an initiative that aims to improve the current situation by reviewing the production site and processes from the unique perspective of the equipment manufacturer and making them more efficient.
FUJI Kaizen Service is broadly divided into three categories: introduction proposal, production diagnosis, and production support.
1. Introduction proposal
- Proposals for optimizing equipment configuration and production operation
- Fuji automation promotion proposals
2. Production diagnosis
- Proposals for making effective use of existing equipment
- Visualizing production, and improving OEE
- Logistics diagnosis
- Proposals for reducing operator workload
3. Production support
- Training for production engineers
- Placement tests and evaluation for new materials
- Creation of shared part position tables on behalf of the client
- Support for program coordinates conversion work
How to use FUJI Kaizen service
PDCA cycle
- Identifying production issues
- Ideas and proposals for improving issues
- Checking and evaluating the implementation of ideas and proposals
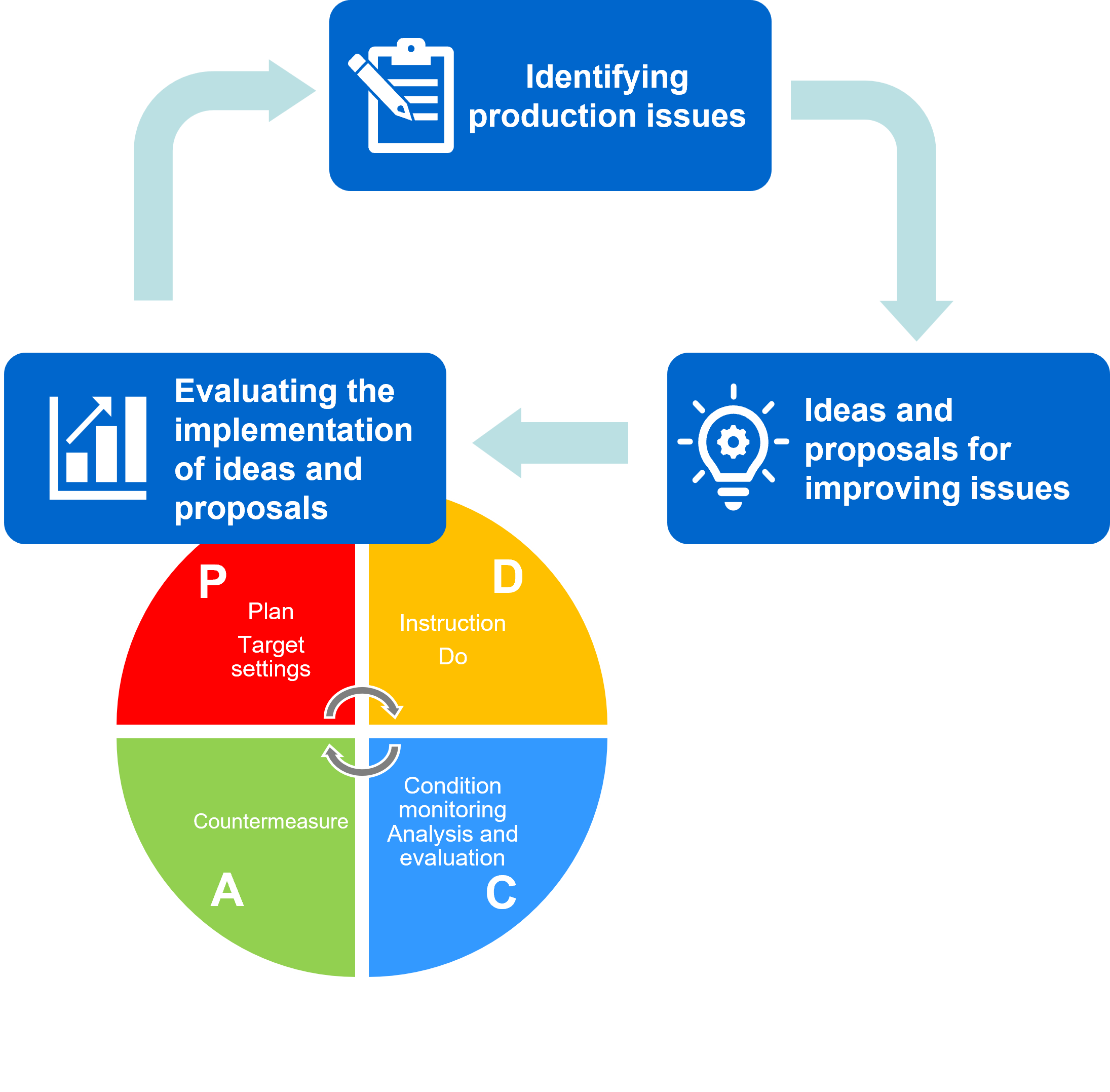
FUJI Kaizen Service examples
It is possible to combine various menus from FUJI Kaizen Service. We provide services that are tailored to your needs.
Some of them are introduced in this section.
1. Operator and programmer weakness reinforcement support plan (2 to 3 days)
FUJI Kaizen menu: Production diagnosis
Theme: Diagnosis of equipment utilization status, identification of lacking skills, and providing on-site training
Identifying issues and weaknesses at production sites
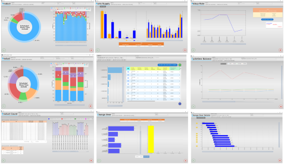
- The number of feeder exchanges during changeover is high
- Placement deviation for specific parts
- Vision processing errors and pickup errors for specific parts
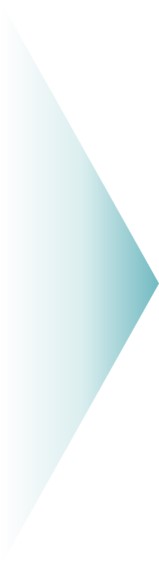
Identifying skills to be reviewed
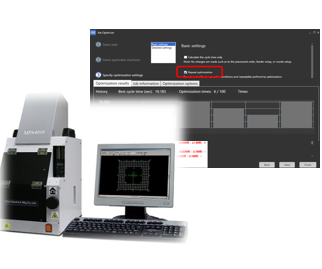
- Optimization method (grouping)
- How to select the optimal nozzles and settings
- Maintenance identification and methods
- How to create vision processing data
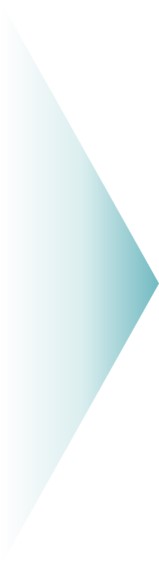
Onsite training
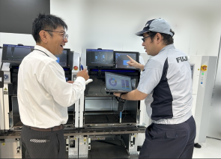
- How to use Multi Job Line Balancer
- How to specify optimization settings
- How to select machine configuration settings and optimal nozzles
- How to use Auto Shape Generator
- How to specify settings for vision processing data in detail
2. OEE improvement proposal plan (5 days)
FUJI Kaizen menu: Production diagnosis
Theme: Aiming to increase actual operating time and improve and stabilize productivity
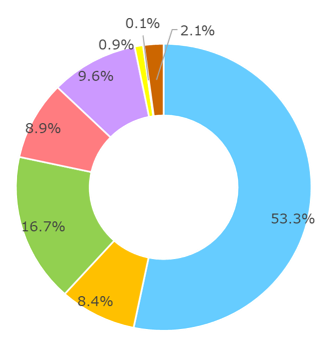
STEP 1:
Pursuing improvement points from line operation
- Delays in changeover work
- Preparation of materials to be supplied
- False alarms at inspection machines
Line operation analysis
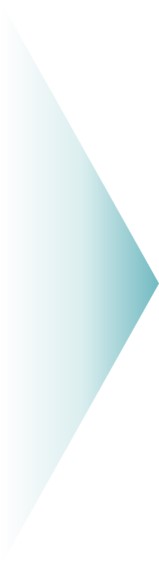
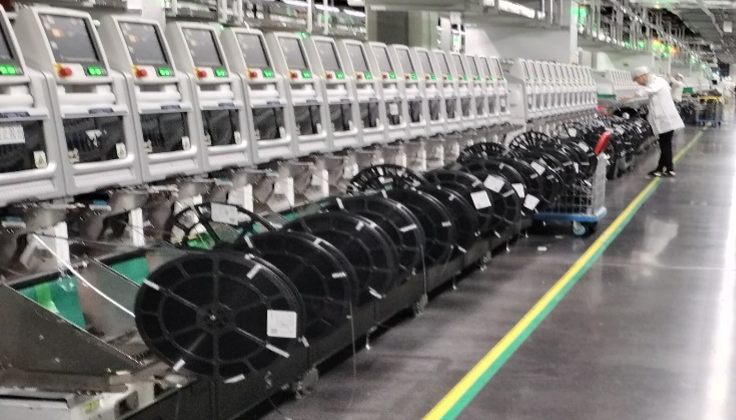
STEP 2:
Identifying issues at production sites
- Delay in changeover work
→Start timing, classification of online and offline changeover, and work steps - Preparation of materials to be supplied, supply timing, and supply accuracy
→Searching for replenishment parts and parts out warning timing - False alarm status of inspection machines
→The false alarm rate is high and there is a delay in operator response
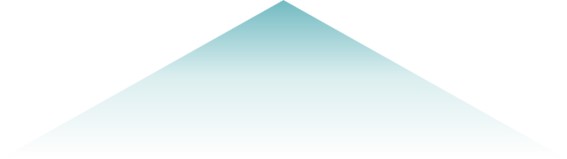
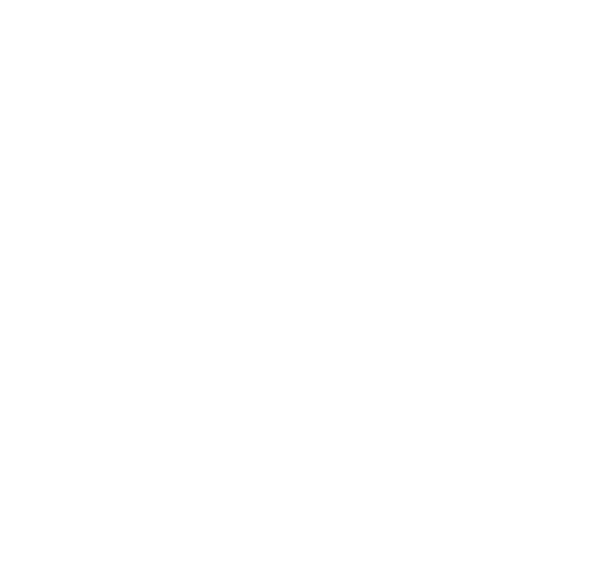
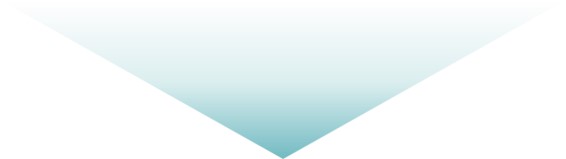
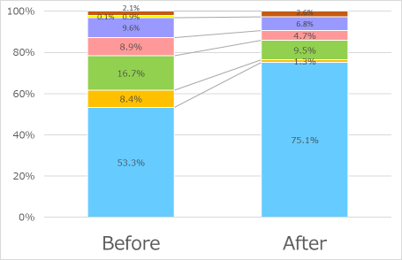
STEP 4:
Checking the effectiveness
- Reducing changeover time
- Simplification of operator work
- Offline inspection
Evaluation
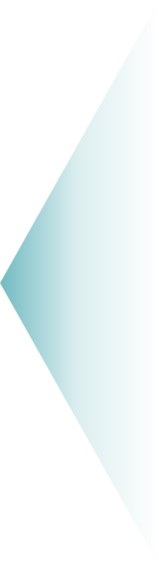
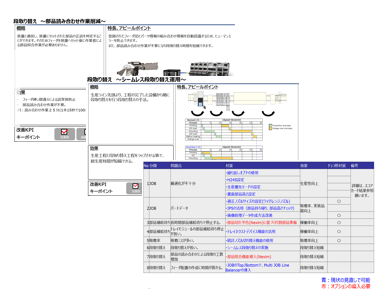
STEP 3:
Investigation for issues
Creating Action Tracker
- Countermeasures for each issue
- Calculating the effects
- Creating a to-do list
3. Equipment configuration optimization plan (5 to 10 days)
FUJI Kaizen menu: Introduction proposal
Theme: Line configuration optimization proposal based on production forecasts
1. Organizing existing equipment
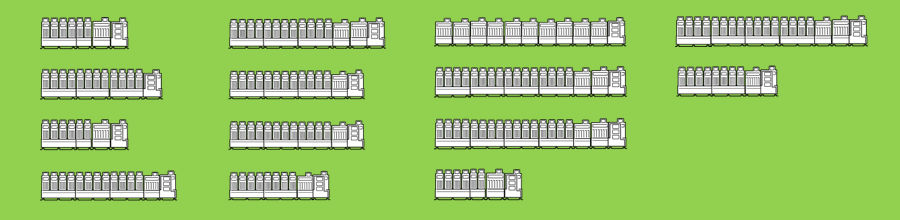
- 14 lines
- 158 modules
- Production time
6128 hours per month
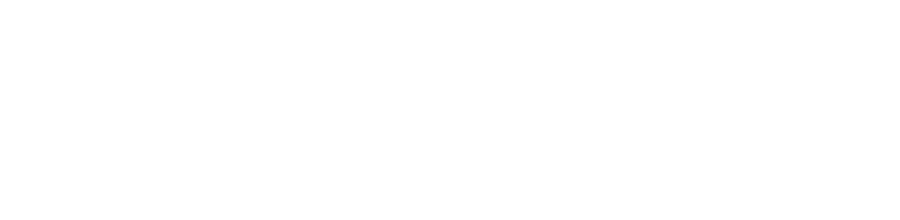
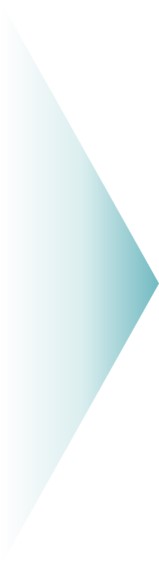
2. Investigating the line configuration
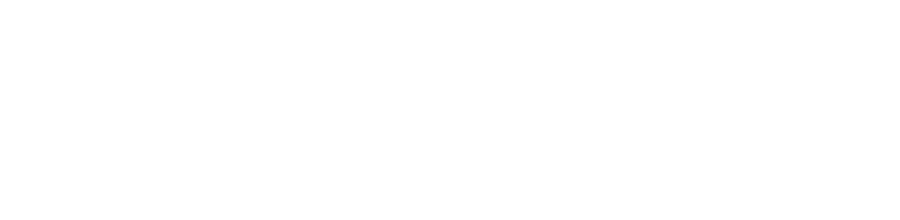
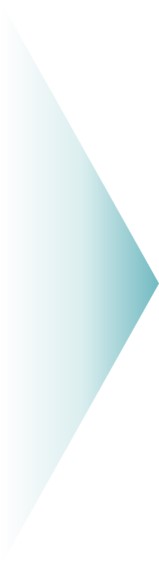
3. Reconfiguring the line configuration
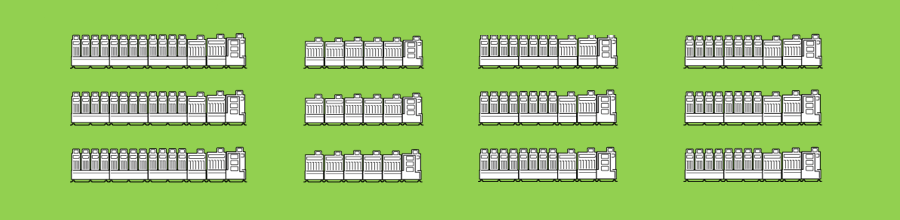
- 12 lines
- 128 modules
- Production time
5317 hours per month
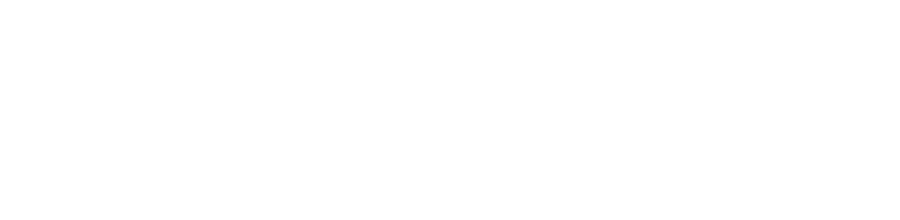
Do you have any problems at your production site?
FUJI Kaizen Service supports production sites from various aspects.
The following are just a few examples of problems.
1. Want to know if we are using the equipment correctly and effectively
2. Productivity is not increasing as expected
3. Want to know where our company stands in comparison to other companies' production sites
4. Want to know how to reduce changeover time and cycle time
5. Want to investigate an efficient machine configuration that matches the production plan
Consult with your Fuji representative if you have any issues that you would like to see remedied at your production site.